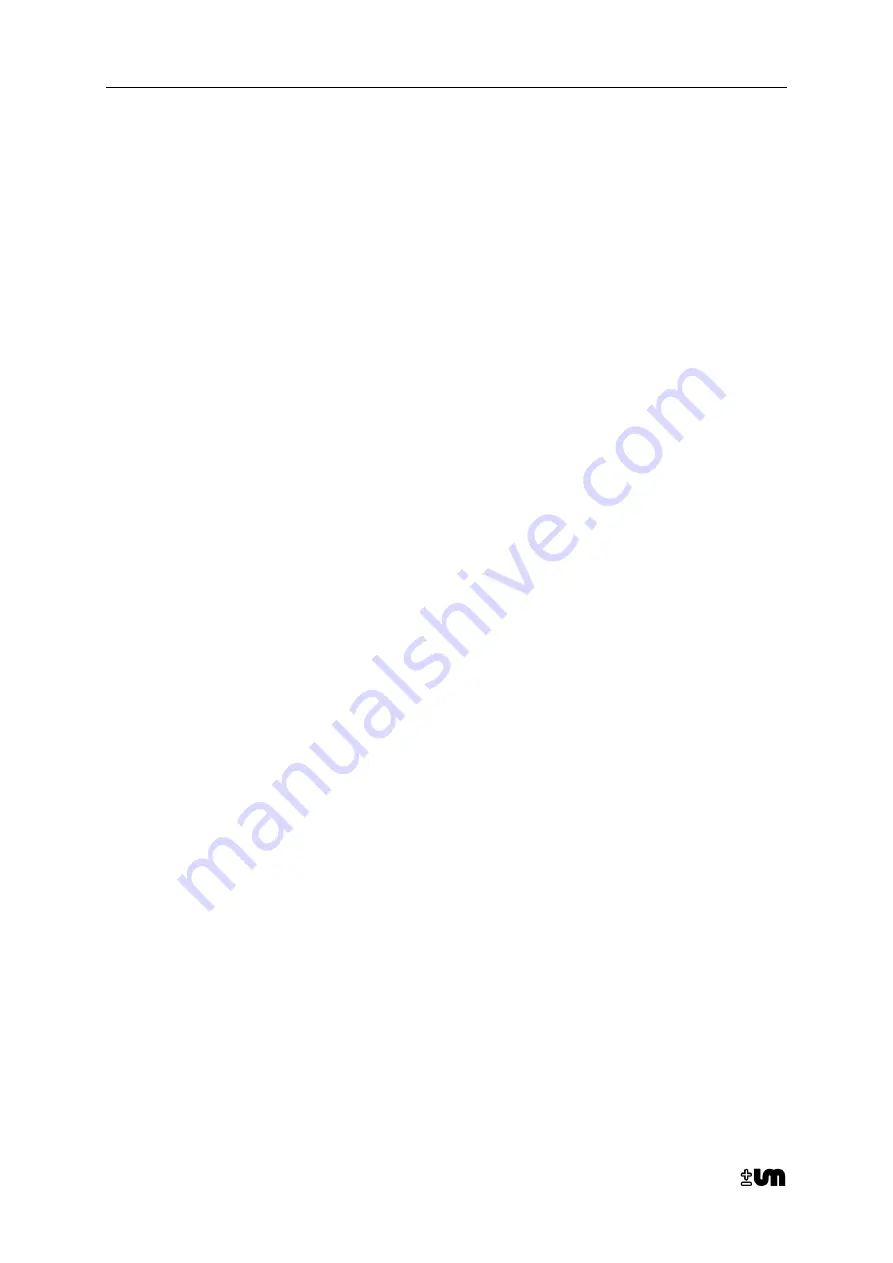
Measurement principle
Manual CWD 2005
___________________________________________________________________
84
Manual CWD2005.doc
9.
Measurement principle
The measurement of process gases by the CWD 2005 is based on a thermopile
principle that has been proven over many years in every type of industry. The
thermopile used is of unique construction and the use of a high-speed thermopile
sets the CWD 2005 apart from all other indirect BTU measuring methods since high
speed response is usually preferred in control applications
9.1.
Heating Value measurement, an overview
Analyzers that measure the components of the process gas (G.C.) are well known
and are sometimes used if only some of the gas components are required to be
measured. Often in the process industry the inability of the G.C. columns to detect all
of the components (leading to errors), slow response speed with the long cycle times
render it unsuitable for dynamic process control applications due to long blind periods
with no measurement response between cycles.
Some manufacturers use an expanding temperature element to measure
temperature rise but the removal of this type of element for cleaning during service is
usually an issue and the use of very small pneumatic nozzles in a position sensing
control system (to maintain element temperature) are subject to blockage.
Other less well known manufacturers measure other parameters than the above to
report calorific value by measuring residual oxygen in exhaust gas and pass-off the
measurement of Combustion Air Requirement Index or CARI as being the ”same as“
heat release value.
Note:
Indirect measuring methods using Zirconia oxide sensors (ZrO
2
) were only
developed for applications where the gases are stable and remain in the same
family, (usually Natural gas) and may require many calibration gases to curve fit the
results of waste, flare or other unknown gases into a useable linear output. Errors
from CO, H
2
or O
2
in process gas can be up to 100% per % of component. For
example: 5% fuel based O
2
produces a potential 5% error that would only be noticed
if the user happened to use a series of calibration gases that reflected this effect as
the unit will always repeat if the same calibration gas is used. This and the fact they
are really measuring fuel/air ratio and not BTU has kept these units out of
mainstream use on process fuel gas applications.
Conductivity, catalytic or optical sensors have surfaced over the years, but for
various reasons, they have been withdraw or not been accepted by the market.
The water bath combustion calorimeter was for many years the gas industry standard
with its many moving parts submerged in water. Slow response, weekly calibration
with an open hydrogen flame, lack of product development and its orphan status by a
large corporate owner ensured its demise as the industry looked for new features.
The CWD 2005 combustion calorimeter responds to all components contained in the
process gas and reports them online as heating value and the measurement is fast,
direct and simple to maintain online.