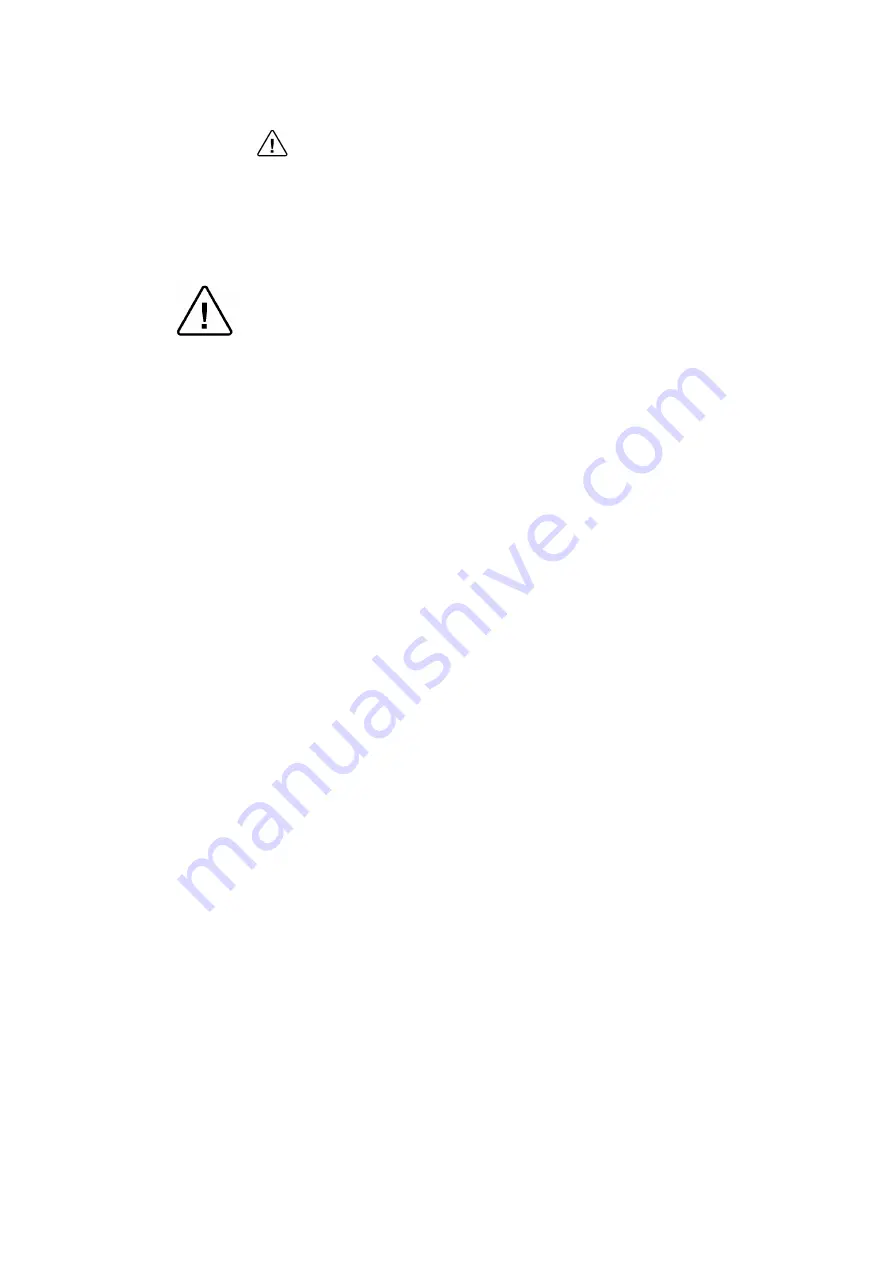
Page 72 of 85 Pages
are displayed on the screen. Refer to "Displayed Error
Messages/Symbols".
Pressing the START/STOP key cancels the displayed message and
enables opening the door.
If the door is not opened, the vacuum pump will stop automatically
after 30 minutes.
Warning
The load has not completed a sterilization cycle, therefore it is not
sterile. Handle it as contaminated load.
10.10
Start Cycle by Clock mode
1. This mode enables the operator to define the time of the
beginning of the cycle. The maximum possible delay is 24
hours.
Содержание 5050
Страница 2: ......
Страница 6: ...Page 4 of 85 Pages TABLE OF CONTENT Cont DRAWINGS PAGE NO FRONT VIEW 17 REAR VIEW 18 ...