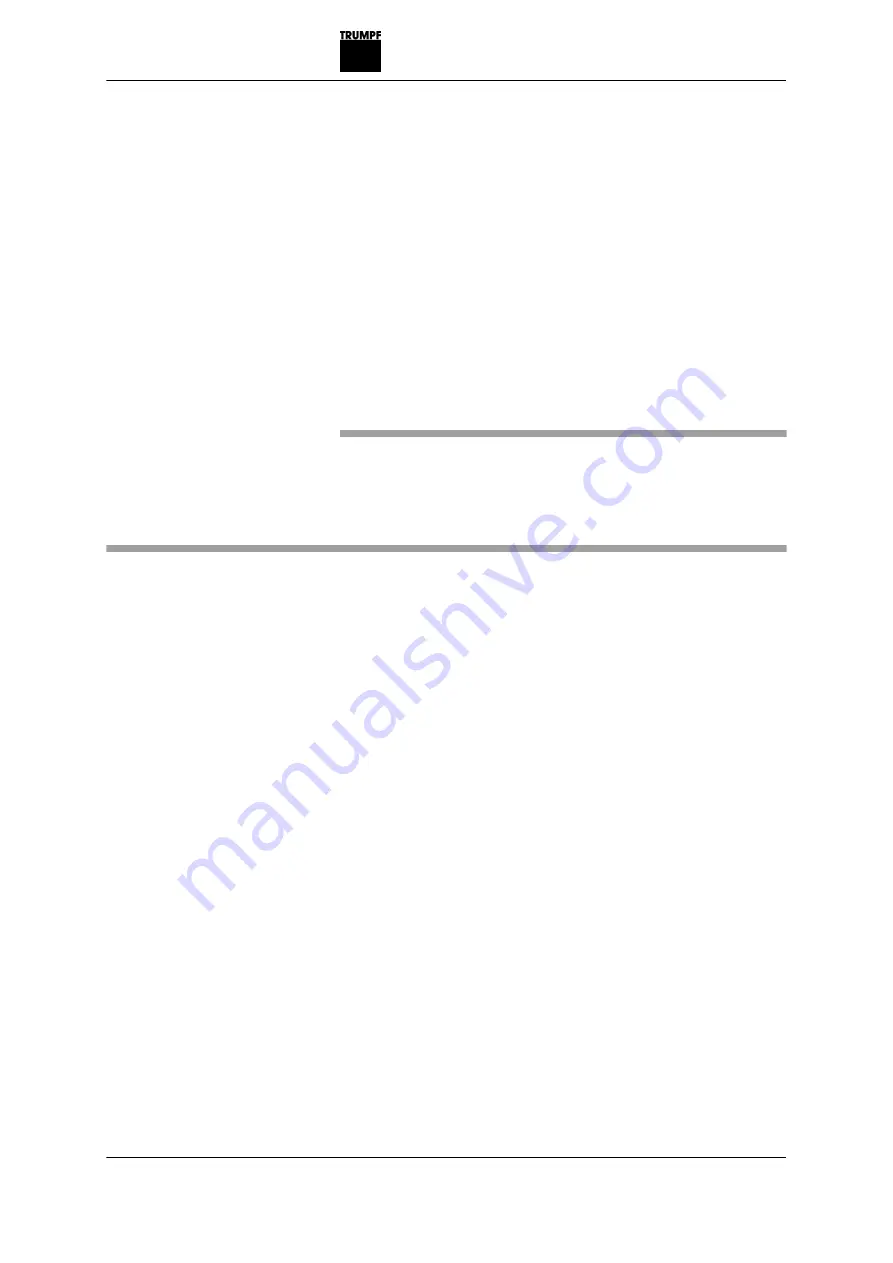
Chapter 1
Safety
1
Safety concept
2
Regulations and guidelines
3
Terms
4
Operational safety
4.1
Intended use
4.2
Significant change to the machine
4.3
Authorized personnel
5
Hazards
5.1
Mechanical dangers
Dangers of slipping, tripping or falling
Moving robot axes
Tilting and falling workpieces
B1154en
2020-09-01
Safety
1
‐
1