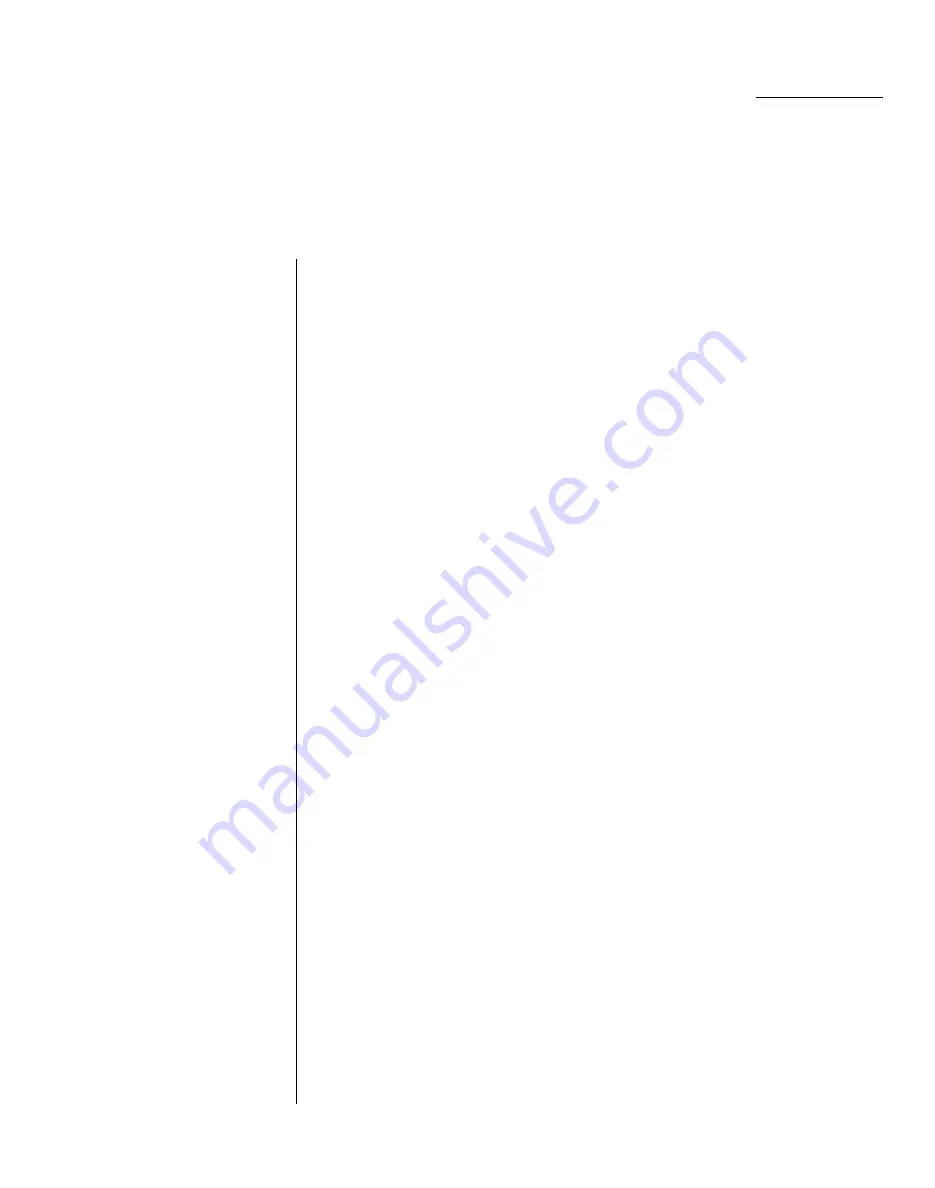
TAC-7X
MANUAL
4.
Normal
Operation
NOTE
This discussion originally assumes a contact is in the Transfer Tip after
Initial Turn-On.
When a properly stripped conductor is inserted into the wire funnel and
subsequently into the contact, it eventually bottoms out in the contact.
Continued pressure depresses the N-1 slide until N1 Slide Sensor
closes, which blocks the air bleed existing at the N1 Sensor. When this
air bleed is closed, sufficient air pressure exists to switch (S-1). Supply
for this air bleed is provided by (R-3). lmmediately upon the switching on
of S-1, the controller energizes the solenoid at (V-1). With V-1 activated,
air pressure is supplied to the extend portion of the Crimp Cylinder
(CR-1) initiating the crimp cycle.
This event is precluded from happening if no part
exists in the transfer tip.
The mechanics of the Crimp Cylinder are such that, unless the cylinder
moves (closes) enough to block the air bleed at the Crimp Head Forward
sensor (G Sensor) and allow air pressure to be applied to (S-4), the
system will terminate its cycle until reset. The purpose of this feature is
to insure the Crimp Cylinder has advanced to correspond to the G"
dimension set.
Supply for "G" Sensor Air Bleed is provided by (R-4).
If the Crimp Cylinder has travelled far enough to block the air bleed at
the "G" Sensor, sufficient air pressure will exist to change the state of
(S-4).
As soon as S-4 is switched on, the controller energizes the solenoid at
(V-3). Turning on V-3 turns off air pressure to the slide cylinder and turns
on air pressure to the Wire Funnel Cylinders (FC-1). It is at this point in
the cycle that the operator removes
·
·
the crimped contact/conductor.
With no contact now in the transfer tip, Vacuum Sensor Switch (S-6) is
turned off. With S-6 off, the PLC controller energizes (V-2) sending the
Transfer Arm (TA-1) to the vertical (pick-up) position.
Содержание TAC-7AE
Страница 6: ...Figure 1 1 TAC 7X Front View ...
Страница 8: ... Figure 1 2 Wire Insertion Through Funnel ...
Страница 12: ...Figure2 1 Pneumatic Hook Up ...
Страница 14: ... Fiqure 2 4 Track Drop Tube Escapement ESCAPEMENT SYSTEM _ _ _ BR ASSEMBL I TRA ...
Страница 18: ... ARBOR COVER PLA TE REMOVED Figure 3 1 Crimp Cylinder Arbor Open ...
Страница 20: ... ARBOR COVER PLAT E REMOVED Figure 3 2 Crimp Cylinder Arbor Closed ...
Страница 23: ... Crimp Inspection Points Improper Crimps ...
Страница 33: ...Figure 6 1 TAC 7X Components ...
Страница 34: ...Figure 6 2 Control Box Components Figure 6 2 TAC 7X Components Right View ...
Страница 35: ...PLC Controller Switching Power Supply Vibratory Feed Controller Figure 6 3 TAC 7X Components Left View ...
Страница 37: ...Figure 6 3 Contact Track Feed Air Adjustments ...
Страница 42: ... Figure 6 4 Indenter Plate Removal ...
Страница 43: ...HOSE CLAMP CAREFULL Y REMOVE Figure 6 5 Indenter Replacement ...
Страница 47: ...Figure 6 6 Indenter Adjustment ...
Страница 52: ...TAC 7X Pneumatic Diagram ...