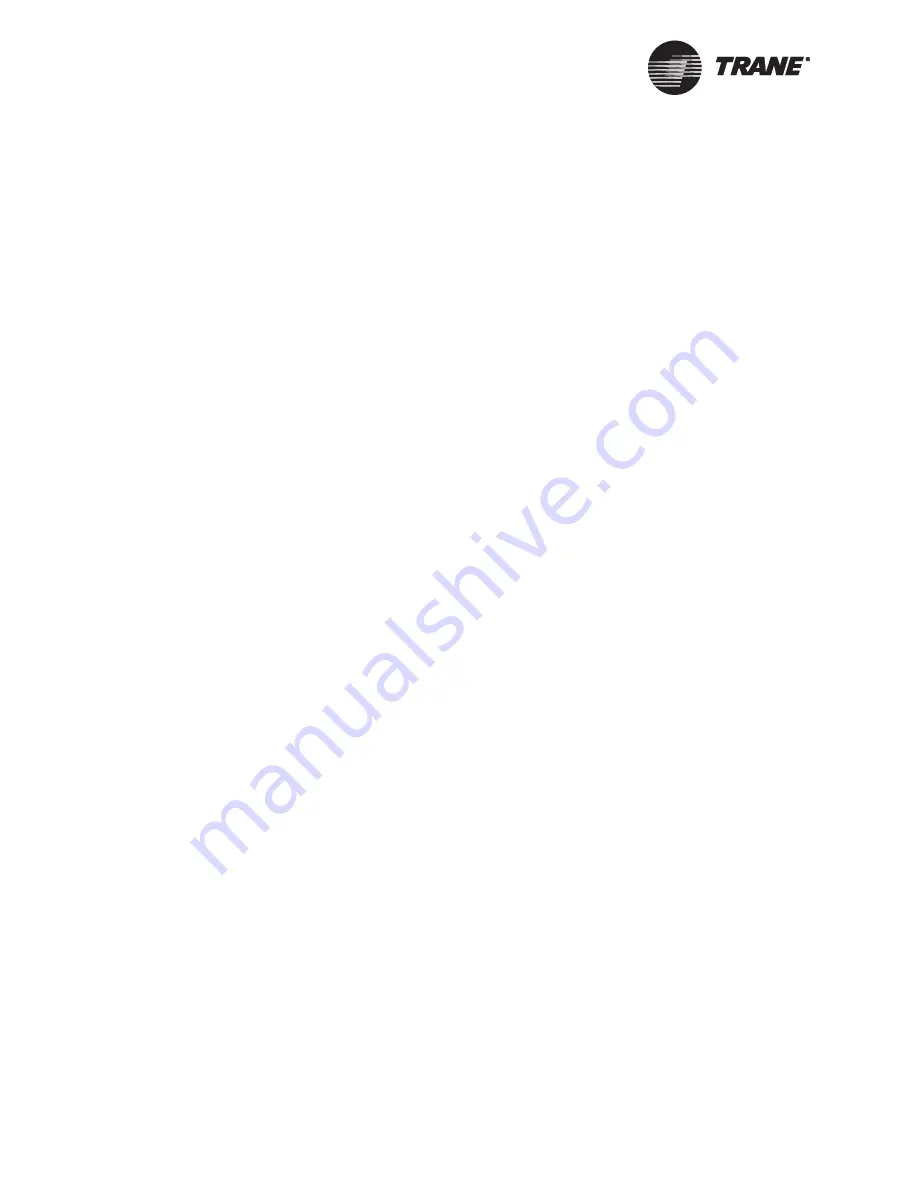
Chapter 9 PID control
64
CNT-SVX12C-EN
PID calculations
PID algorithms perform three calculations: the proportional calculation,
the integral calculation, and the derivative calculation. These calcula-
tions are independent of each other but are combined to determine the
response of the controller to the error.
Proportional calculation
The proportional calculation responds to how far the measured value is
from the setpoint. The larger the error, the larger the output of the calcu-
lation. The proportional calculation has a much stronger effect on the
result of the PID algorithm than either the integral or derivative calcula-
tions. It determines the responsiveness (or aggressiveness) of a control
system. Though some systems use only proportional control, most Trane
controllers use a combination of proportional and integral control.
Proportional-only control loops require an error to produce an output. If
the setpoint and the process variable are the same, the error is zero, so
the system does not have an output. In an HVAC system, this can cause
an actuator to open or close. The integral calculation solves this problem.
The recommended range for the proportional calculation in the Tracer
ZN517 is 4–16. Restore PID factory defaults by clicking the Use Defaults
button.
Integral calculation
The integral calculation responds to the length of time the measured
value is not at setpoint. The longer the measured value is not at setpoint,
the larger the output of the calculation.
The integral calculation uses the sum of past errors to maintain an out-
put when the error is zero. Line 1 in Figure 20 on page 65 shows that with
proportional-only control, when the error becomes zero, the PID output
also goes to zero. Line 2 in Figure 20 shows the integral output added to
the proportional output. Because the integral calculation is the sum of
past errors, the output remains steady rather than dropping to zero when
the error is zero. The benefit of this is that the integral calculation keeps
the output at the appropriate level to maintain an error of zero.
The value of the integral calculation can build up over time (because it is
the sum of all past errors), and this built-up value must be overcome
before the system can change direction. This prevents the system from
over-reacting to minor changes, but can potentially slow the system down.
The recommended range for the integral calculation in the Tracer ZN517
is 1–10. Restore PID factory defaults by clicking the Use Defaults button.
Содержание Tracer ZN517
Страница 1: ...CNT SVX12C EN Installation and Operation Tracer ZN517 Unitary Controller...
Страница 2: ......
Страница 3: ...Installation and Operation Tracer ZN517 Unitary Controller CNT SVX12C EN April 2005...
Страница 4: ......
Страница 12: ...Table of contents vi CNT SVX12C EN...
Страница 38: ...Chapter 4 Sequence of operations for the 2 heat 2 cool configuration 26 CNT SVX12C EN...
Страница 56: ...Chapter 6 Sequence of operations for the 4 cool configuration 44 CNT SVX12C EN...
Страница 92: ...Chapter 10 Status indicators for operation and communication 80 CNT SVX12C EN...
Страница 104: ...Chapter 12 Troubleshooting 92 CNT SVX12C EN...
Страница 110: ...Index 98 CNT SVX12C EN...