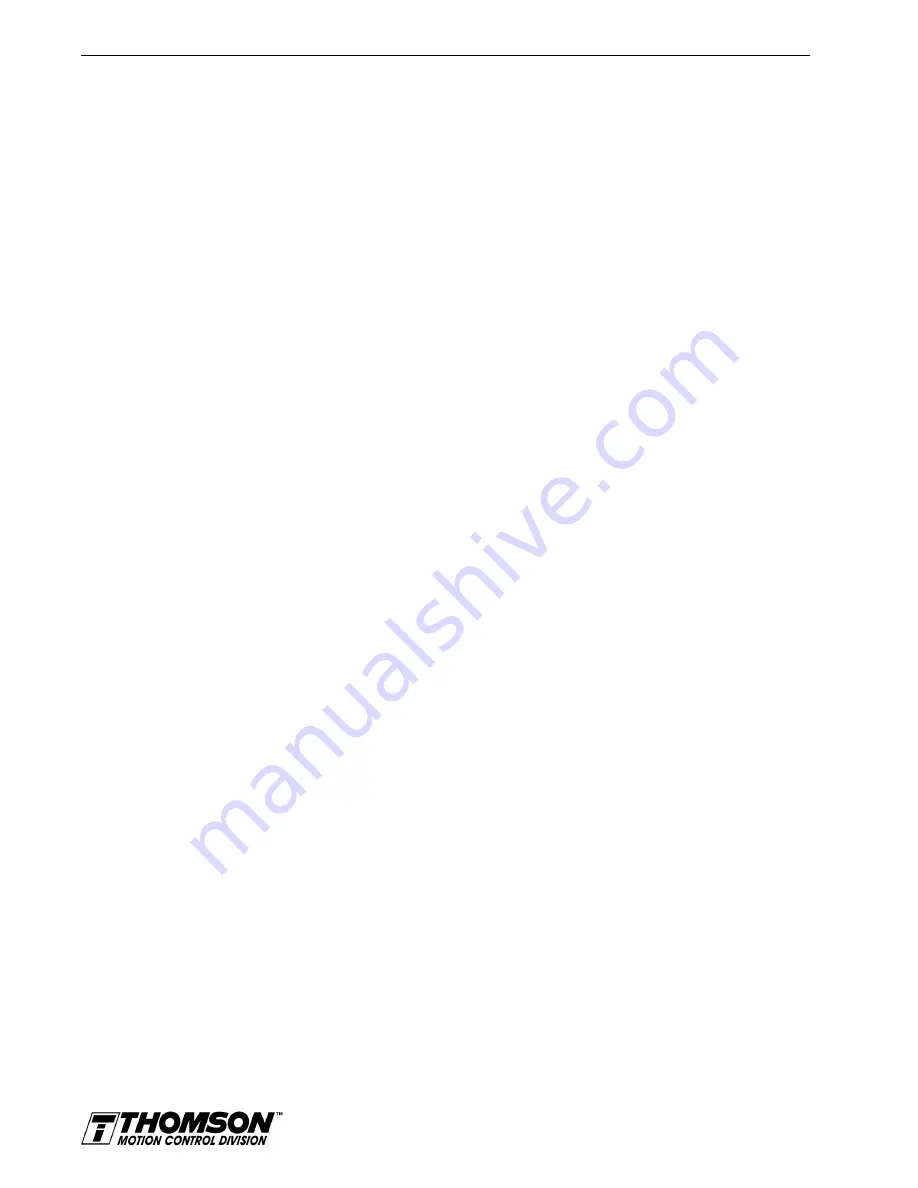
B-2
Creating Custom Motor Files
Drive and Motor File Configuration with OMNI LINK
At startup OMNI LINK examines the contents of the /MOTORDIR subdirectory to determine the list of
motors it will display. If a custom motor file is to appear, it must be copied into the /MOTORDIR directory
before OMNI LINK is started. Each motor file is a binary file that contains:
•
the motor parameter set,
•
a table ID number, and
•
a text string.
Because they are binary files, only OMNI LINK can be used for editing and generation (i.e., you cannot
edit motor files using a text editor.)
Motor Parameter Set
The motor parameter set configures the OMNIDRIVE to control a specific motor. Motor parameters
provide information about the electrical properties, ratings and construction of the motor. Subsequent
sections of this appendix explain these properties with meaningful depth. For now it is sufficient to know
that accurate and complete definition of the motor’s properties is necessary to achieve good performance.
Table ID
The table ID number tells OMNI LINK whether the motor file represents a standard motor or a custom
motor:
•
Standard motor table IDs occupy the range 0 to 65534.
•
The custom motor table ID is 65535 (also known as “-1”).
Standard motor parameter sets are stored in the drive as well as in the motor file. Thus OMNI LINK needs
to transmit only the table ID to select the motor model from the drive's personality EEPROM. For custom
motor files, OMNI LINK must transmit not only the custom motor’s table ID but also the complete motor
parameter set from the custom motor file.
Text String
The text string allows OMNI LINK to display a meaningful name in the motor model window. The text
string displays one of three possible messages when a motor is loaded into the drive:
•
“BLX232A2”, or equivalent if a valid motor model number is loaded.
•
“Custom” if a custom motor file is loaded.
•
“Unknown” if an unrecognized motor file is loaded.
The text string translates the table ID into a real motor model number for display.
Motor Phasing
The phasing of the back-EMF and Hall feedback signals must be verified before a custom motor file can
be created. Thomson Industries motors use back-EMF and Hall feedback signals phased as shown in
Figure B.2. Motors not manufactured by Thomson Industries require the back-EMF and Hall feedback
signals be phased to match those of Thomson Industries motors. Often this requires swapping of the R-,
S- and T-phase control signals with each other, as well as swapping the Hall A, Hall B, and Hall C signals
with each other.
Back-EMF and Hall Signals
Figure B.2(a) shows the required phasing of the
line-to-line
back-EMF signals and Figure B.2(b) shows
the proper phasing of the Hall feedback signals, when the motor is rotating clockwise (CW)
as seen
looking at the motor shaft from the load
.
Artisan Technology Group - Quality Instrumentation ... Guaranteed | (888) 88-SOURCE | www.artisantg.com