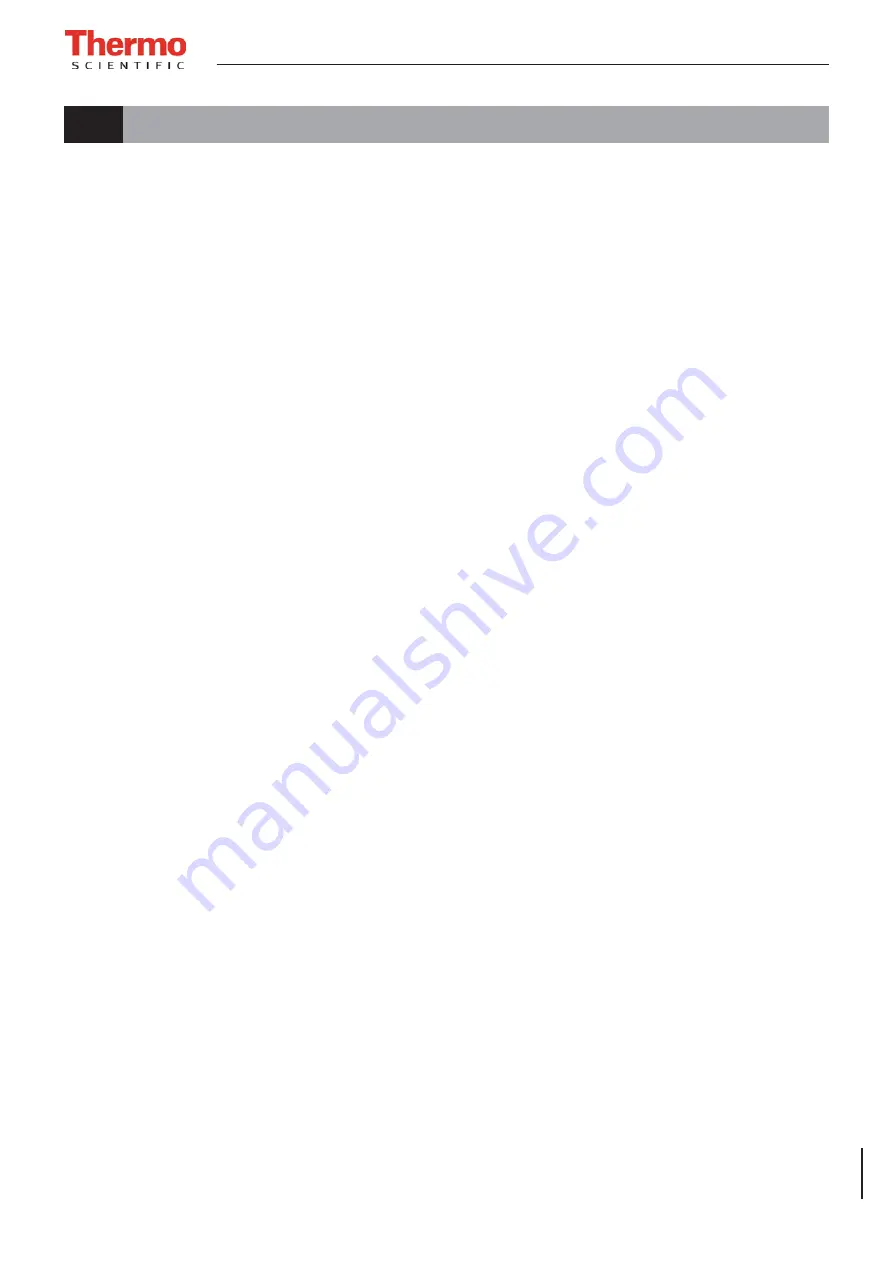
CO
2
Incubator BB 150 Operating Instructions
67
14.
Principles of good microbiological practice
1
General information:
• Keep windows and doors at the place of location closed while carrying out
work.
• Do not eat, drink or smoke in the work area.
Do not store food in the work area.
• Wear laboratory frocks or other protective clothing in the work area.
• Always use auxiliaries when pipetting.
• Do not use syringes and hollow needles unless absolutely necessary.
• For all manipulations, try to avoid aerosol formation.
• After completion of the work and prior to leaving the work area, wash your
hands thoroughly and disinfect and regrease them, as required.
• Keep the work area tidy and clean. The work tables should contain only the
required devices and materials. Store stocks only in the designated contai-
ners and cabinets.
• Check the identity of the used agents at regular intervals as required for as-
sessing the potential hazard. The intervals depend on the potential hazard.
• When handling agents, employees are subject to a verbal, job-related instruc-
tion prior to starting work and subsequently at least once a year.
• Employees with little or no experience in microbiology, virology or cellular bi-
ology must be carefully instructed, guided, and looked after.
• Vermin must be exterminated at regular intervals, as required.
The following additional principles apply to the handling of causatives:
• Disinfect all workplaces every day. If required, the growth of resistent germs
must be prevented by using a different disinfectant.
• Do not wear protective clothing outside the work area.
• Autoclave or disinfect contaminated devices prior to cleaning.
• Germ-contaminated waste must be collected safely and destroyed by autocla-
ving or disinfecting.
• If infectious material is spilled, the contaminated area must be immediate-
ly blocked and disinfected.
• When handling humanopathogenic germs for which an effective vaccine is
available, all employees must be vaccinated and immunity has to be
checked at regular intervals using appropriate measures.
• The health conditions of the employees must be monitored using occupa-
tional medicine check-ups, i.e. initial examination prior to starting work and
annual follow-ups. For the check-ups, particularly the guidelines G24, “Skin
Diseases”, and G42, “Infection Diseases”, of the German trade associations
apply; these guidelines are used as generally acknowledged occupational
medicine guidelines by physicians to rate, evaluate, and acquire examina-
tion results based on identical criteria.
• For handling genetically manipulated organisms, viruses, and subviral agents
with potential hazards, proceeding according to guideline G43, “Biotechno-
logy”, of the German trade associations is required.
• First aid instructions for accidents with pathogenic microorganisms and vi-
ruses must always be freely accessible in the work area. All accidents must
be reported immediately to the supervisor in charge.
Further safety measures in dependence of the potential hazard:
• Usage of safety cabinets (airflow directed away from the experimentator)
according to Class I, Class II (type-tested)
2
or Class III.
• Restriction and monitoring of the access to certain areas.
• Usage of special protective clothing and breathing equipment.