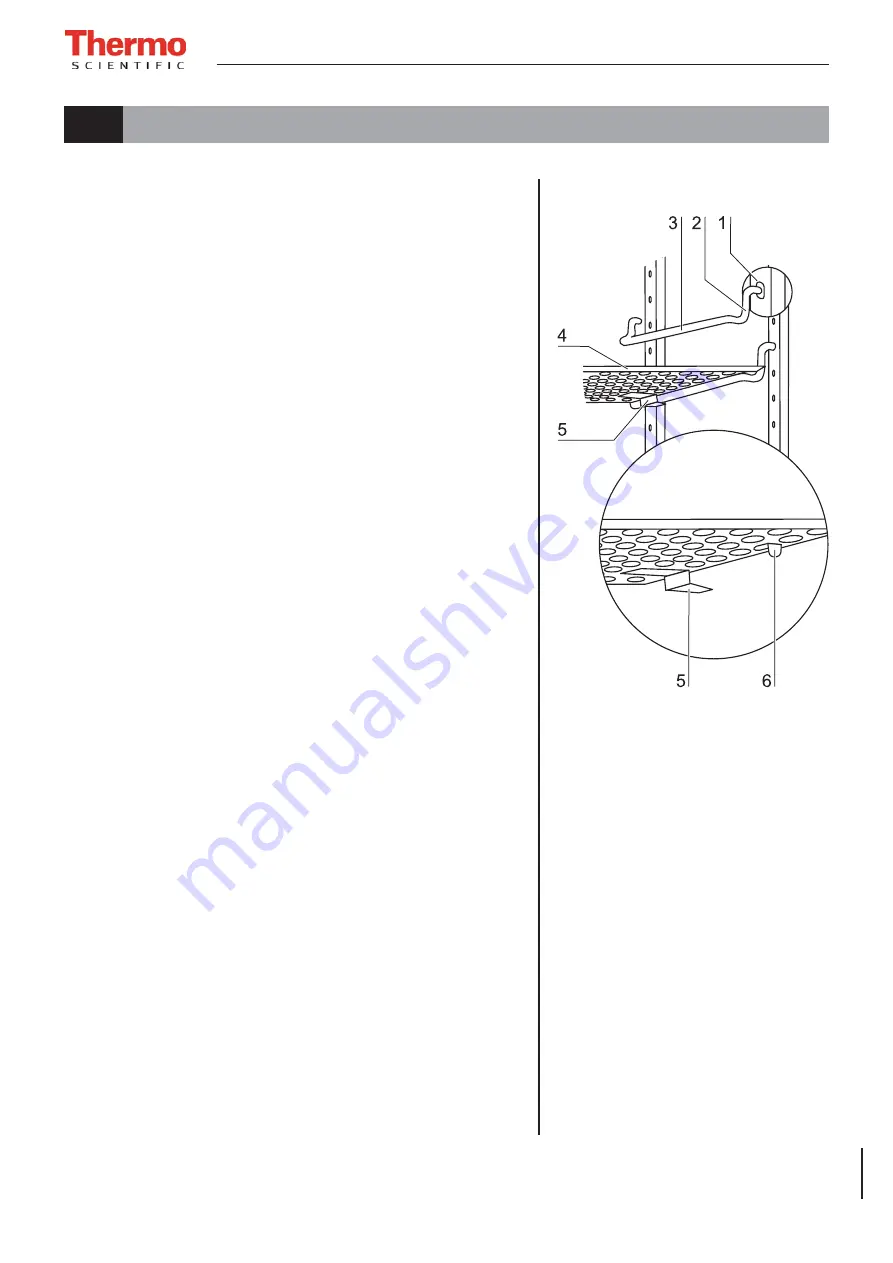
CO
2
Incubator BB 150 Operating Instructions
25
5.
Start-up
Installing the shelf supports:
1.
Fig. 13:
Insert the shelf supports [3] into the perforations
[1] of the support rail with the bar facing down.
2. Make sure that the two vertical elements [2] of the shelf
support are flush with the support rail.
Installing the shelves:
1.
Fig. 13:
Push the shelf [4] onto the shelf supports with the
tilt protection [5] facing the rear panel of the device. The tilt
protection [5] is also used as a guide for the shelf.
2. Slightly raise shelf so that the withdrawal stop [6] can be
routed over the shelf supports.
3. Make sure that the shelf supports are positioned in the two
tilt protectors in a way that it can move freely.
Levelling the device:
1. Position a bubble level on the center shelf.
2. Rotate the adjustable device stands using the supplied 24
mm wrench until the shelf is positioned horizontally in all
directions. Perform the adjustment of the device stands from
left to right and from rear to front.
Fig. 13
Shelf support/sheet/
insert installation