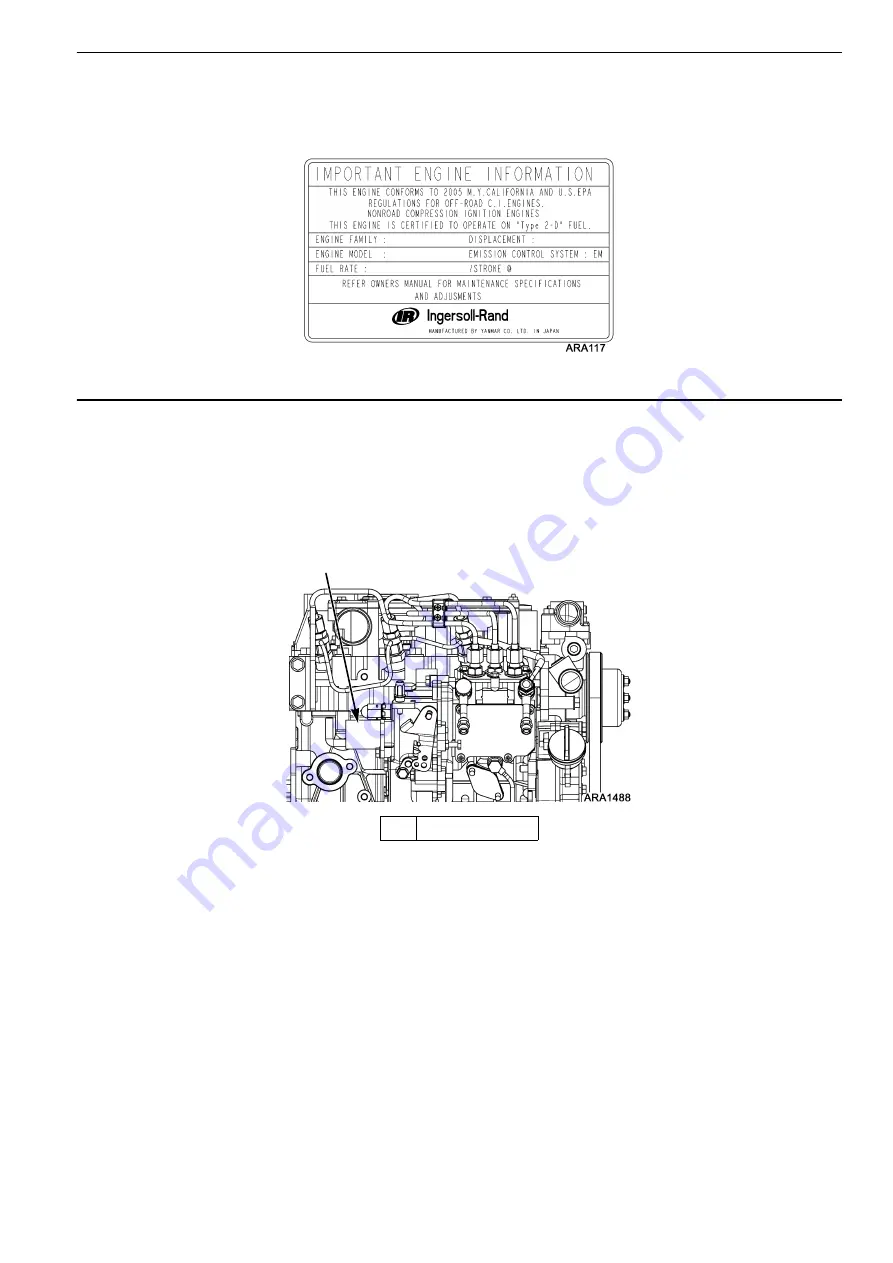
Engine Maintenance
9-25
Fuel Limit Screw
The fuel limit screw is not adjustable. It is equipped with an anti-tamper cap to fulfill requirements for CARB (California Air
Resources Board) emission regulations. Service technicians must be CARB certified to perform service on the fuel limit screw
for equipment operating in California.
Emission Control Label
Fuel Solenoid
The fuel solenoid is located on the end of the injection pump. It contains two coils: the pull-in coil, and the hold-in coil. The
pull-in coil draws approximately 35 to 45 amps at 12 volts. The hold-in coil draws approximately 0.5 amps at 12 volts.
The pull-in coil must be momentarily energized to move the fuel rack to the on position. Once the fuel rack has been moved
to the on position, the hold-in coil will then hold the fuel rack in the on position until the 8D circuit is de-energized. The pull-in
coil must be de-energized after a few seconds to keep it from being damaged. The pull-in coil is controlled by the microprocessor
through the fuel solenoid pull in relay (K6).
Testing the Fuel Solenoid
The fuel solenoid pull-in coil will require 35 to 45 amps to turn on the fuel. The unit’s battery must be in good condition. If
the battery has enough power to crank the engine over, it has enough power to energize the fuel solenoid pull-in coil.
If you suspect that the engine does not run because the fuel solenoid is not operating correctly, use the following procedure:
1. Use the Mechanics/Premium HMI Control Panel to enter the Interface Board Test Mode. Refer to the appropriate
Microprocessor Diagnostic Manual for specific information about the Interface Board Test Mode.
2. Energize the run relay with the Interface Board Test Mode. The fuel solenoid relay is momentarily energized when the run
relay is energized with the Interface Board Test Mode. This energizes the fuel solenoid, which makes a definite click when
energized.
3. De-energize the run relay with the Interface Board Test Mode. This de-energizes the fuel solenoid, which makes a definite
click when de-energized.
4. Repeat steps 2 and 3 a few times to check the operation of the fuel solenoid.
1.
Fuel Solenoid
Fuel Solenoid Location
1
Содержание T-1000R
Страница 14: ...Safety Precautions 2 6 Warning Decals 2e24151g0 ...
Страница 18: ...Specifications 3 4 ENGINE CLUTCH Engagement 600 100 RPM Dynamic Torque 66 fT lb 89 5 N m minimum 1600 RPM ...
Страница 34: ...Maintenance Inspection Schedule 4 10 ...
Страница 57: ...Unit Description 5 23 Purge Mode UT Series 1 3 4 5 2 ...
Страница 67: ...Unit Description 5 33 Zone 1 Cool and Zone 2 Cool UT SPECTRUM Units ...
Страница 69: ...Unit Description 5 35 Purge Mode UT SPECTRUM Units ...
Страница 71: ...Unit Description 5 37 Zone 1 Cool and Zone 2 Heat UT SPECTRUM Units ...
Страница 72: ...Unit Description 5 38 ...
Страница 74: ...Diesel Electric Menu 6 28 Adjust Brightness 6 29 Time 6 30 ...
Страница 120: ...Operating Instructions Standard HMI 7 18 ...
Страница 152: ...Engine Maintenance 9 14 T Series Fuel and Oil System Components TK 376 ...
Страница 154: ...Engine Maintenance 9 16 T Series Fuel and Oil System Components TK 270 ...
Страница 156: ...Engine Maintenance 9 18 UT Series Fuel System Components AMA768 ...
Страница 172: ...Engine Maintenance 9 34 T Series Engine Mounting Components for 2 Cylinder Engine ...
Страница 184: ...Engine Maintenance 9 46 ...
Страница 238: ...Refrigeration Maintenance 10 54 ...
Страница 246: ...Clutch Maintenance 11 8 ...
Страница 258: ...Structural Maintenance 12 12 ...
Страница 264: ...Mechanical Diagnosis 13 6 ...
Страница 265: ...14 Electric Standby Diagnosis ...
Страница 268: ...Electric Standby Diagnosis 14 4 ...
Страница 269: ...15 Refrigeration System Diagnosis ...
Страница 272: ...Refrigeration System Diagnosis 15 4 ...
Страница 280: ...Remote Evaporators 16 8 ...
Страница 282: ...Wiring Diagrams and Wiring Schematics 17 2 ...