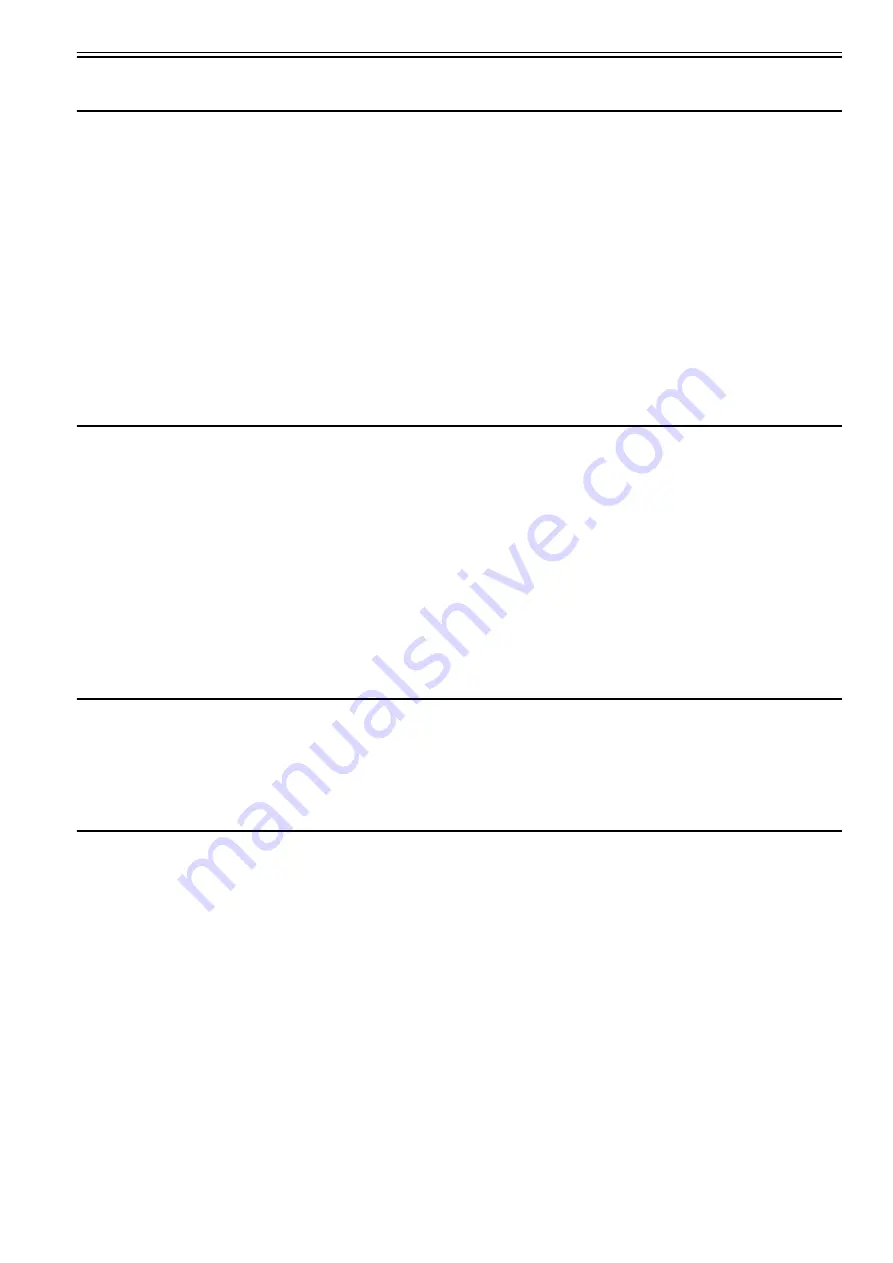
Safety Precautions
2-3
ELECTRICAL
Microprocessor Service
Precautions must be taken to prevent electrostatic discharge when servicing the microprocessor controller and related
components. Potential differences considerably lower than those which produce a small spark from a finger to a door knob can
severely damage or destroy solid-state integrated circuit components.
The following procedures must be rigidly adhered to when servicing units to avoid microprocessor damage or destruction.
1. Disconnect all power to the unit.
2. Avoid wearing clothing that generates static electricity (wool, nylon, polyester, etc.).
3. Do wear a static discharge wrist strap (TK P/N 204-622) with the lead end connected to the microprocessor’s ground terminal.
These straps are available at most electronic equipment distributors. DO NOT wear these straps with power applied to the unit.
4. Avoid contacting the electronic components on the circuit boards of the unit being serviced.
5. Leave the circuit boards in their static proof packing materials until ready for installation.
6. If a defective controller is to be returned for repair, it should be returned in the same static protective packing materials from
which the replacement component was removed.
7. After servicing the controller or any other circuits, the wiring should be checked for possible errors before restoring power.
Welding of Units or Truck Bodies
When electric welding is to be performed on any portion of the temperature control unit, truck or truck chassis when the
temperature control unit is attached, it is necessary to ensure that welding currents are NOT allowed to flow through the electronic
circuits of the unit.
These procedures must be rigidly adhered to when servicing units to avoid damage or destruction of the controller.
1. Disconnect all power to the unit.
2. Disconnect all wire harnesses from the controller.
3. Switch all of the electrical circuit breakers in the control box to the OFF position.
4. Weld unit and/or container per normal welding procedures. Keep ground return electrode as close to the area to be welded as
practical. This will reduce the likelihood of stray welding currents passing through any electrical or electronic circuits.
5. When the welding operation is completed, the unit power cables, wiring and circuit breakers must be restored to their normal
condition.
High Voltage
When servicing or repairing a temperature control unit, the possibility of serious or even fatal injury from electrical shock exists.
Extreme care must be used when working with a refrigeration unit that is connected to a source of operating power, even if the
unit is not operating. Lethal voltage potentials can exist at the unit power cord, inside the control box, at the motors and within
the wiring harnesses.
Low Voltage
Control circuits used in the temperature control unit are low voltage (24 volts ac and 12 volts dc). This voltage potential is not
considered dangerous, but the large amount of current available (over 30 amperes) can cause severe burns if shorted or grounded.
Do not wear jewelry, watch or rings. These items can short out electrical circuits and cause severe burns to the wearer.
Содержание T-1000R
Страница 14: ...Safety Precautions 2 6 Warning Decals 2e24151g0 ...
Страница 18: ...Specifications 3 4 ENGINE CLUTCH Engagement 600 100 RPM Dynamic Torque 66 fT lb 89 5 N m minimum 1600 RPM ...
Страница 34: ...Maintenance Inspection Schedule 4 10 ...
Страница 57: ...Unit Description 5 23 Purge Mode UT Series 1 3 4 5 2 ...
Страница 67: ...Unit Description 5 33 Zone 1 Cool and Zone 2 Cool UT SPECTRUM Units ...
Страница 69: ...Unit Description 5 35 Purge Mode UT SPECTRUM Units ...
Страница 71: ...Unit Description 5 37 Zone 1 Cool and Zone 2 Heat UT SPECTRUM Units ...
Страница 72: ...Unit Description 5 38 ...
Страница 74: ...Diesel Electric Menu 6 28 Adjust Brightness 6 29 Time 6 30 ...
Страница 120: ...Operating Instructions Standard HMI 7 18 ...
Страница 152: ...Engine Maintenance 9 14 T Series Fuel and Oil System Components TK 376 ...
Страница 154: ...Engine Maintenance 9 16 T Series Fuel and Oil System Components TK 270 ...
Страница 156: ...Engine Maintenance 9 18 UT Series Fuel System Components AMA768 ...
Страница 172: ...Engine Maintenance 9 34 T Series Engine Mounting Components for 2 Cylinder Engine ...
Страница 184: ...Engine Maintenance 9 46 ...
Страница 238: ...Refrigeration Maintenance 10 54 ...
Страница 246: ...Clutch Maintenance 11 8 ...
Страница 258: ...Structural Maintenance 12 12 ...
Страница 264: ...Mechanical Diagnosis 13 6 ...
Страница 265: ...14 Electric Standby Diagnosis ...
Страница 268: ...Electric Standby Diagnosis 14 4 ...
Страница 269: ...15 Refrigeration System Diagnosis ...
Страница 272: ...Refrigeration System Diagnosis 15 4 ...
Страница 280: ...Remote Evaporators 16 8 ...
Страница 282: ...Wiring Diagrams and Wiring Schematics 17 2 ...