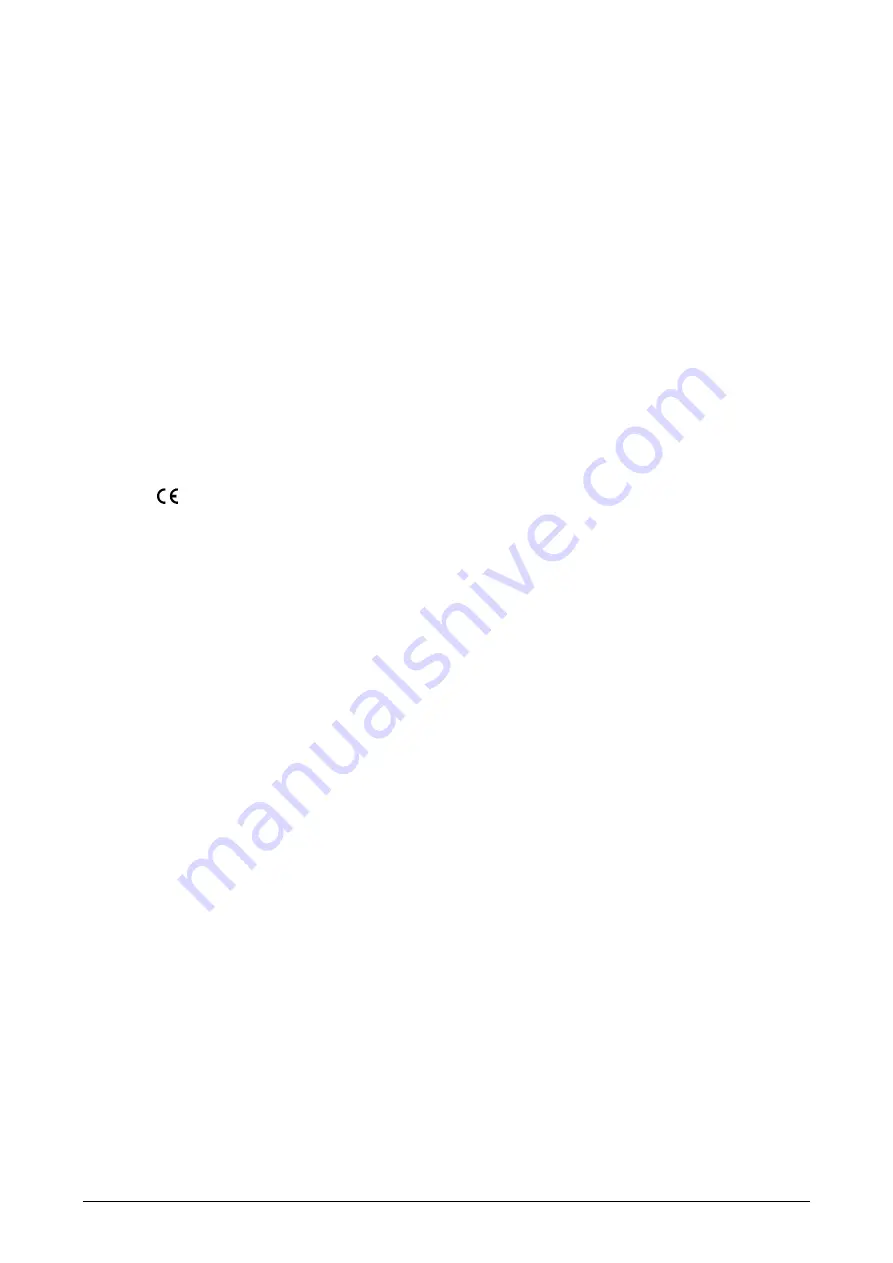
- 7 -
Fan assembly:
It is made up by one or more low noise emission and high-performing centrifugal fans, powered by an electric
engine connected to a pulley and belt driving system. If possible, the engine is equipped with a variable-pace
pulley, which ensures that the machine will easily adapt to the destination plant.
Control and safety thermostat:
The machines are equipped with thermostats; their sensor shall be placed on the air outlet (prepared and
electrically connected in the manufacturing plant), with the following functions:
•
"FAN" function
(FAN thermostat
–
calibration: +25/+35°C), it activates the fans max. 60 seconds
after the burner has started and it stops them approx. 4 minutes after it has stopped. Thus, it prevents
unpleasantly cold air from being released in the room when the machine is activated and the thermal
energy accumulated by the heat exchanger can be exhausted, by completely using it before the
machine stops.
•
“SAFETY” function
(TR safety thermostat - pre-set calibration: +80°C ). It is installed on the 3÷8
types. It stops the burner if the air is anomalously overheated. It is automatically restored. It shall be
correctly calibrated when it is used for the first time.
•
"LIMIT" function
(LM Thermostat - sealed calibration: +100°C): it stops the burner if the air is
anomalously overheated. It shall be manually restarted.
Smoke discharge inlet
The machine is fitted with a round inlet where a metal pipe should be safely inserted and fixed, in order to
discharge the combustion products.
The flue to be used must be in accordance with and certified
standard
.
Condensate drainage connector
Since the combustion products are expected to function with an output of condensation, the device is equipped
with a threaded connection for the discharge of condensation; it must be connected according to current
standards in force.