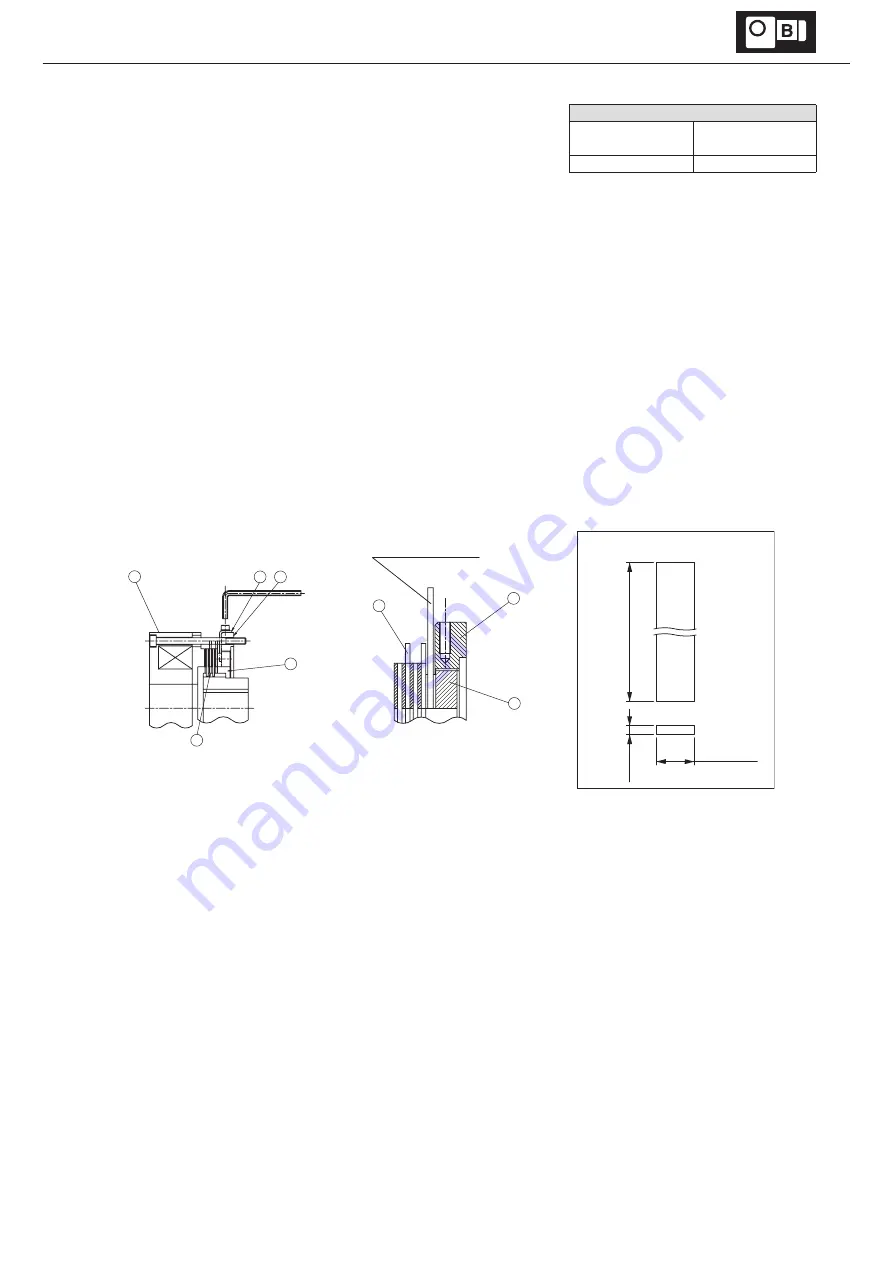
54
8. Daily Inspection and Maintenance
55
4
16
1
2
14
Gap adjusting bar
2
1
14
Gap Adjusting Bar Dimension
14.7±0.1mm
150m
m
3.5m
m
- Gap Inspection
(1) Remove the cover [8].
(2) Insert a gap gauge between the field [4] and the armature [12] and measure the
gap. Measure in 4 locations around the circumference.
(3) Adjustment is required if the gap value is near the limit.
- Gap Adjustment
(1) Manually release the brake following the procedure on P70.
(2) Loosen the stopper [16] on the periphery of the center ring [1], and remove. This will free the gap adjusting screws [2].
(See Figure 8-15)
(3) Insert a gap adjustment bar (An angle plate should be prepared by customer. See Figure 8-17) into the groove of adjustment screw
(2) between the outer disk [14] and the center ring [1].
Rotating to the left as seen from the field [4] side, will narrow the gap. (See Figure 8-16)
(4) Six attachment bolts [3] and lock bolts [11] alternately pass through the space between the outer disc [14] and the center ring [1].
Rotating the gap adjustment bar will make the bar touch these bolts. There are 8 equally distributed holes for gap adjusting screws
[2]. Adjust the gap G to the required value by repeating (3) each time the gap adjusting bar contacts a bolt.
(5) Select the point where hole and screw hole are closest to the required gap and attach the stopper [16] there.
(6) After returning the manual brake release to its original state, turn power on and off to check brake action.
(7) Attach the fan [7] and cover [8]. At this time coat the fan set screw [10] with Three Bond TB2365.
Figure 8-15
Figure 8-16
Figure 8-17
Gap Value G (mm)
Required value
(original value)
Limit value
0.7
2.0