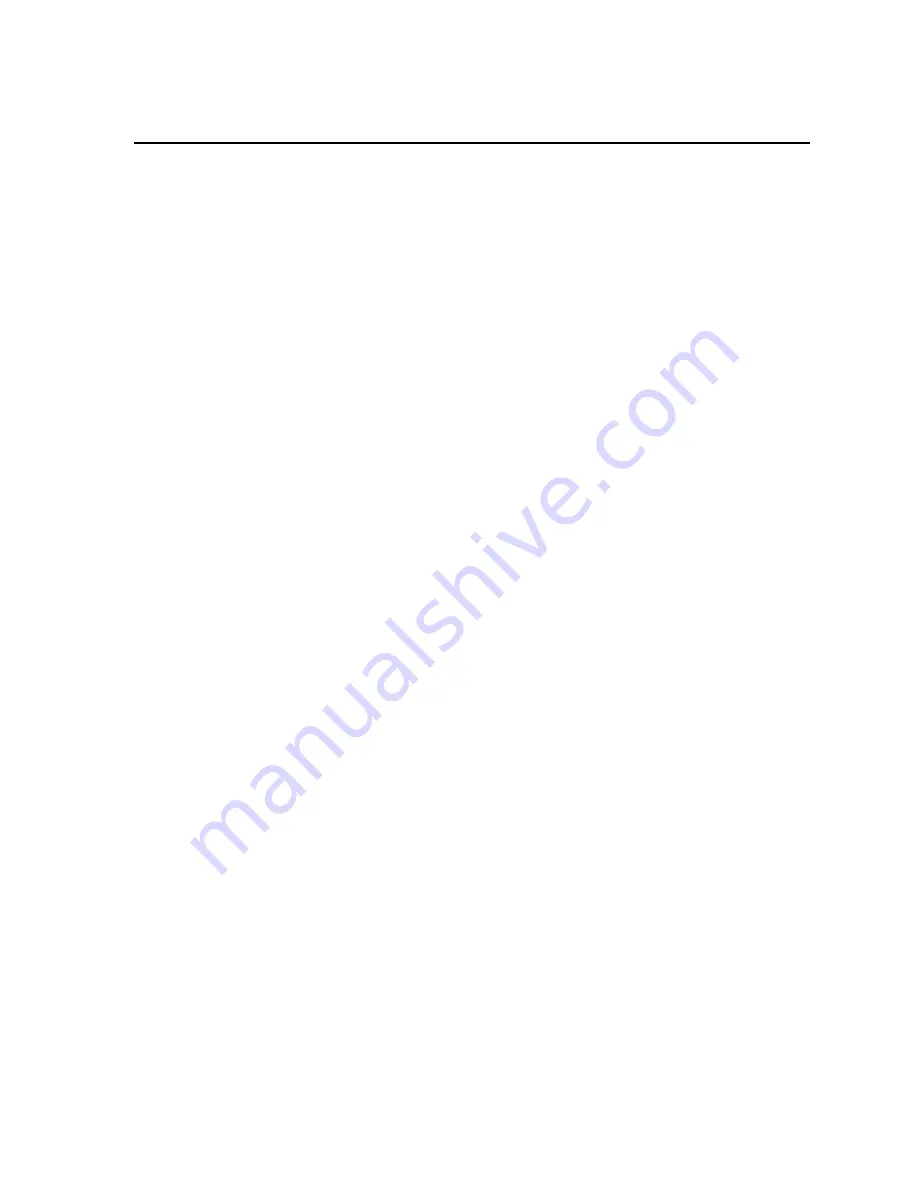
Chapter 10 - Calibration
The calibration procedure for each model differs primarily in the arm and weight combina-
tion required to reach the calibration points for the model's torque capacity. Each procedure
requires the use of:
*
A computer equipped with a serial port and terminal software.
*
A serial cable.
*
Calibration weights, drive squares, arms, and platforms for the model to be tested.
*
Refer to the "
Calibration Table -
Torq-Tronics
® Models
" at the end of this chapter.
Calibration Procedure
1) Turn on the
Torq-Tronics
®
unit. Allow it to warm up for one (1) hour in Track mode.
2) Connect
Torq-Tronics
®
unit to computer via serial cable.
3) Start terminal software.
4) For a summary of the calibration commands, type
:CM
into the terminal software, then
press the "Enter" key.
5) Press the ZERO key on the
Torq-Tronics
®
unit, then type
:CM2
into the terminal soft-
ware and press the Enter key. Observe acknowledgement of calibration zero.
6) Obtain the proper calibration arm. The correct arm can be found in the "
Calibration
Table -
Torq-Tronics
® Models
" at the end of this chapter.
7) Make certain the calibration arm is properly counterbalanced.
8) Attach the drive square of the calibration arm to the drive of the tester in the clockwise
direction, and press the Zero key.
9) Hang the weight platform (hook) and the full-scale weights (100%) (found in the
"
Calibration Table -
Torq-Tronics
® Models
") on the calibration arm - gently, and
imparting as little motion to the weights as possible. Wait until the weights have com-
pletely stopped moving, then remove the full-scale load.
10) Wait one minute, then press the ZERO key on the tester.
11) Repeat steps 9 and 10 two more times, then proceed to step 12.
12) Hang the 1st calibration point (10%) weights, as found in the "
Calibration Table -
Torq-Tronics
® Models
", on the arm, gently. Wait for the arm to completely stop mov-
ing, then enter
:CM1
into the terminal software and press the Enter key. Observe
acknowledgement of the 10% clockwise calibration point.
Содержание 10191
Страница 2: ......
Страница 6: ......
Страница 8: ...This page intentionally left blank...
Страница 12: ...This page intentionally left blank...
Страница 34: ...This page intentionally left blank...
Страница 40: ...This page intentionally left blank...
Страница 46: ...This page intentionally left blank...
Страница 51: ......