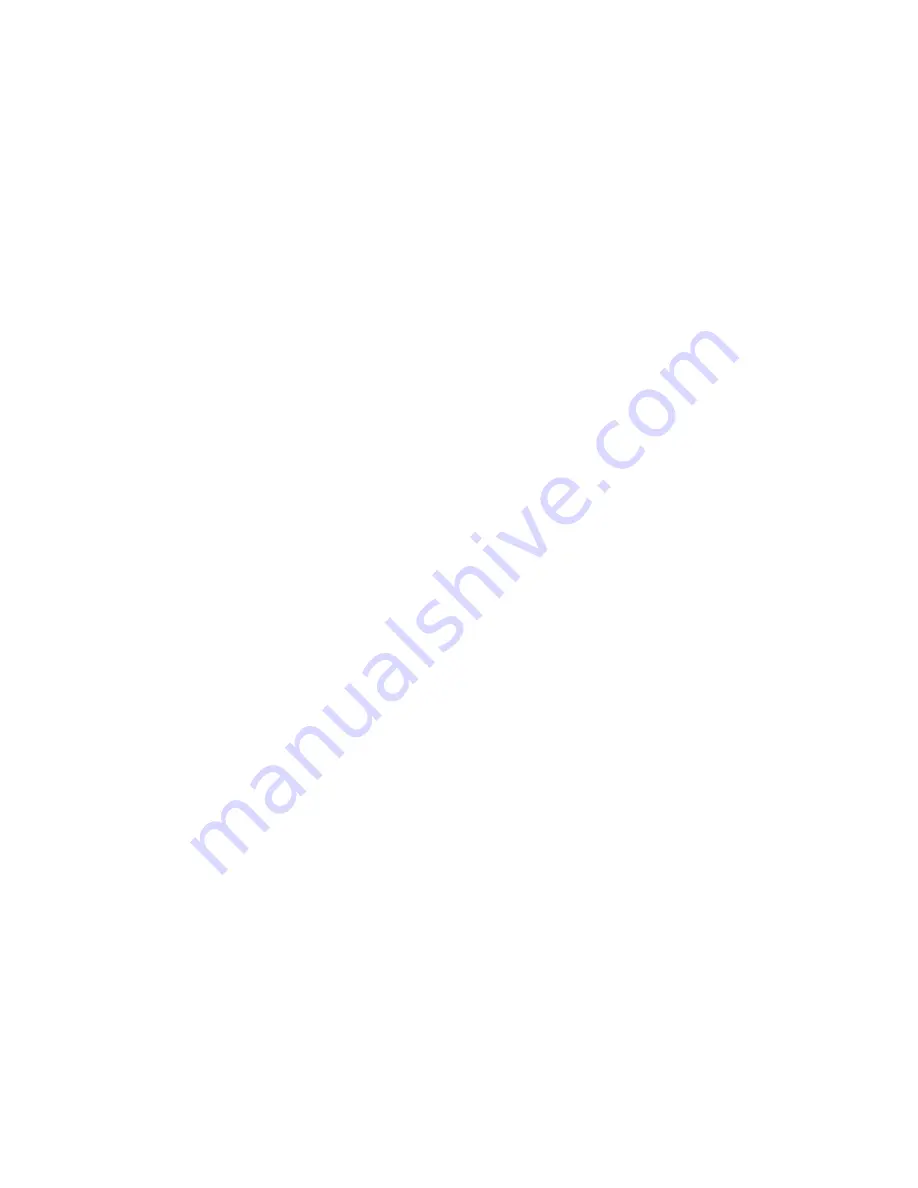
where both techniques (correlative and tool-specific) are employed, the possibility of confu-
sion exists. This also adds to the cost of training new calibration personnel, as well as
increasing the probability of error.
The record keeping requirements for the tool-specific approach are slightly larger than those
for the correlative approach. Each tool must have, in addition to the filter selection for each
tool, a record of the exact washer configuration for the tool/joint combination. Any devia-
tion from the exact washer configuration will result in a differing joint rate, and on most
tools, show up as a shift in torque output.
Example
Power tool brand D, serial number 2345, is used on joint "Y", which is a medium joint
requiring about 270 degrees of rotation to get from 10% of installation torque specification
to 100% of installation torque. Experimentation determines that to obtain results from test-
ing the same as those on the line, it is necessary to use 12 washers in the joint simulator,
stacked in a configuration where the direction of every third washer is reversed, and with
filter 3 selected.
For each calibration of that tool for use on that joint, the technician must (1) look up the
proper washer configuration, (2) disassemble the joint simulator, (3) properly configure the
washer stack, (4) reassemble the joint simulator, (5) install the joint simulator on the tester,
and finally (6) conduct the tests. At least three pitfalls exist (1, 3, and 1 and 3 together)
which offer the possibility of error which will show up as discrepancy in power tool per-
formance. When the power tool shows performance on the tester not consonant with
requirements, the technician must conduct a fairly detailed analysis to determine whether
the problem is test error or a tool problem.
It is for the reasons given above that different plants arrive at different decisions on the
approach to be taken in power tool calibration. The small plant with four power tools of the
same make and model faces an entirely different situation from the very large plant with
500 power tools of differing types, makes, and models.
Information required for implementation of either approach is given in the following chap-
ters in this manual.
Automatic Shutoff Tools
All automatic shutoff tools use the joint for feedback to the shutoff mechanism. This means
that the joint is part of the control loop which determines the shutoff point, and the final
torque, achieved on the fastener by the tool. The tool affects the joint by tightening the fas-
tener, which affects the tool by resisting further rotation, which affects the shutoff mecha-
nism. This loop starts when the tool is activated while engaged with the fastener, and ends
shortly after the shutoff mechanism activates.
Содержание 10191
Страница 2: ......
Страница 6: ......
Страница 8: ...This page intentionally left blank...
Страница 12: ...This page intentionally left blank...
Страница 34: ...This page intentionally left blank...
Страница 40: ...This page intentionally left blank...
Страница 46: ...This page intentionally left blank...
Страница 51: ......