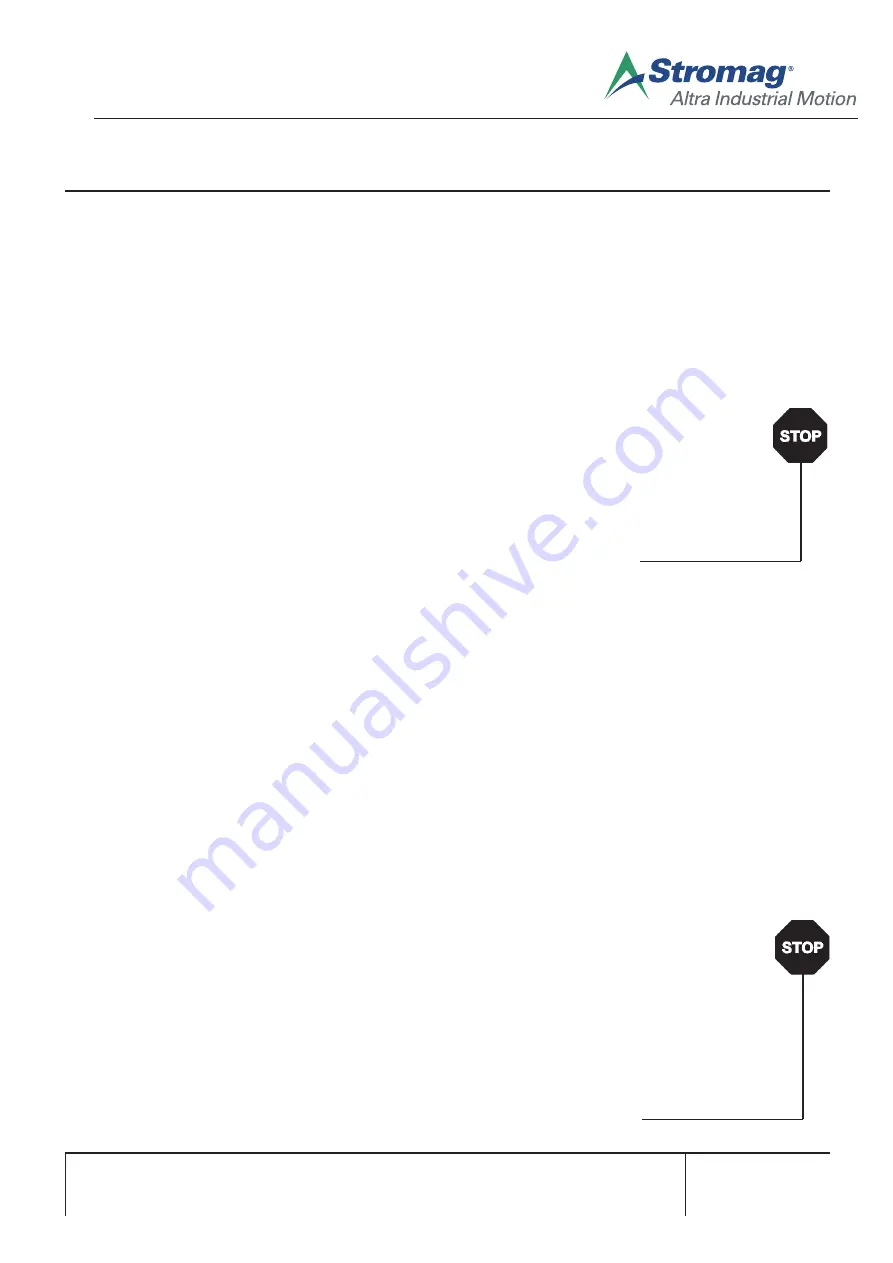
SIME Brakes
13/05/16
M10054-02-A
Installation and maintenance
SIDEOS Box 2
4/17
Non contractual photographs.
Instructions of this manual must be adhered to, to obtain the performance and the safety of operation of the equipment.
Encoder and limit switch 51 questionnaire
No. Q01390-01
Dimensions limit switch 51
No. T10003-01
Installation and maintenance SIDEOS One
No. M10054-01
Limit switch 51 - Stromag
Catalog
No. D142
Installation and maintenance No. 151-00004
EMC
No. 900-00001
2 - OUTPUTS CONTACTS USE
2-1 Use of overspeed outputs
Triggering of the secured contacts outputs : Overspeed C4
(terminals : 25-26) and C5 (terminals : 27-28), indicates an
emergency situation and must drive, directly or via a safety
relay, the redundant contactors of the safety brakes supply
(mechanical stop of type 0).
See diagram examples on chapter : 4.
The information output : Overspeed C6 (terminals : 29-30) can
be used to give triggering information signal to the customer
PLC, the stop control being processed otherwise via the secured
Overspeed contacts.
2-2 Use of System Fault outputs
Triggering of the secured outputs : System fault C1 (terminals:
19-20) and C2 (terminals : 21-22), indicates an operation fault
of the monitoring system :
Those signals must be processed in order to maintain the ma-
chinery in a safe state.
>
Mechanical stop (stop of type 0): the secured contacts out-
puts must drive directly or via a safety relay the redundant
contactors of the service brakes supply.
>
Electrical stop (stop of type 1) : the secured contacts out-
puts must drive the electrical stop of the hoidting motion, the
customer PLC giving back the signal that the System Fault
information is taken into account by 2 loops feedbacks.
See diagram examples on chapter : 4.
The information output System Fault C3 (terminals : 23-24) can
be used to give the triggering information signal to the customer
PLC, the stop control being processed otherwise via the secured
Overspeed contacts.
Restart
:
As indicated in the diagram examples in ch.4, restart of SIDEOS
Box 2 (reset) must not restart the installation, but only allows
the restart of the machinery from a control position with good
visibility of the hazardous area.
Periodical checking
:
When activation of
SIDEOS Box 2
outputs is not frequent (hois-
ting normal application), a procedure of switching off / switching
on of the
SIDEOS Box 2
must be defined by the integrator of
the SIDEOS One system, to carry out periodically the automatic
and global TEST of the
SIDEOS box 2
unit.
3 - INPUTS CONTACTS CHARACTERISTICS
>
Ascent order
(terminals 13-14)
Ascent contact is closed during a hoisting Ascent working order.
>
Descent order
(terminals 15-16)
Descent contact is closed during a hoisting Descent working
order.
>
High Speed order
(terminals 17-18)
High Speed contact is closed during a hoisting High Speed
working order.
ATTENTION !
The High Speed connection cable is imperatively
shielded to avoid the risk of short-circuit in the
connection cable.
Otherwise, connect the High Speed contact
between terminals 15 and 18, and this contact
must imperatively be open (Low Speed order)
when a Hoisting Stop order is present (Ascent
and Descent order absent).
>
Loop feedback : System Fault
(terminals 31-32 + 33-34)
-Output contacts C1 and C2 are used to drive directly
2 internal relays of the customer PLC, which contacts drive
a mechanical stop through the service brakes or an electri-
cal stop through the controller.
-A NC contact of each of these relays is inserted in the res-
pective System Fault feedback loop. Those contacts must
imperatively close, when the contacts C1 and C2 open, to
indicate a System Fault. This allows to the
SIDEOS Box
2
to check the opening of the associated relays and the
customer PLC taking into account.
-
Reminder of EN ISO 13849-2 standard
:
Short-circuits between conductors are excluded in an elec-
trical enclosure (enclosure and connection must comply
with the requirements of CEI/EN 60204-1standard).
-If this exclusion is not possible, it will then be necessary to
include a contact indicating the service brakes closing or
the electrical stop in each feedback loop.
-In case of C1 and C2 contacts use in an input loop of a
safety relay, those loop feedbacks can be shunted.
ATTENTION
!
In this case, taking into account of the System
Fault triggering by the customer PLC and pos-
sible short-circuits in the connection cables of C1
and C2 contacts are no more controlled by the
SIDEOS box 2
unit.
The customer will make sure that all these faults
will be detected by its system (for example : sa-
fety relay with input loops control).
The achieved performance level will then de-
pend on the performance level achieved by the
safety relay.
SIME Brakes
www.stromag.com -
Customer service / Tel. : +33(0)1 49 90 32 20 / Fax : +33(0)1 49 89 06 38