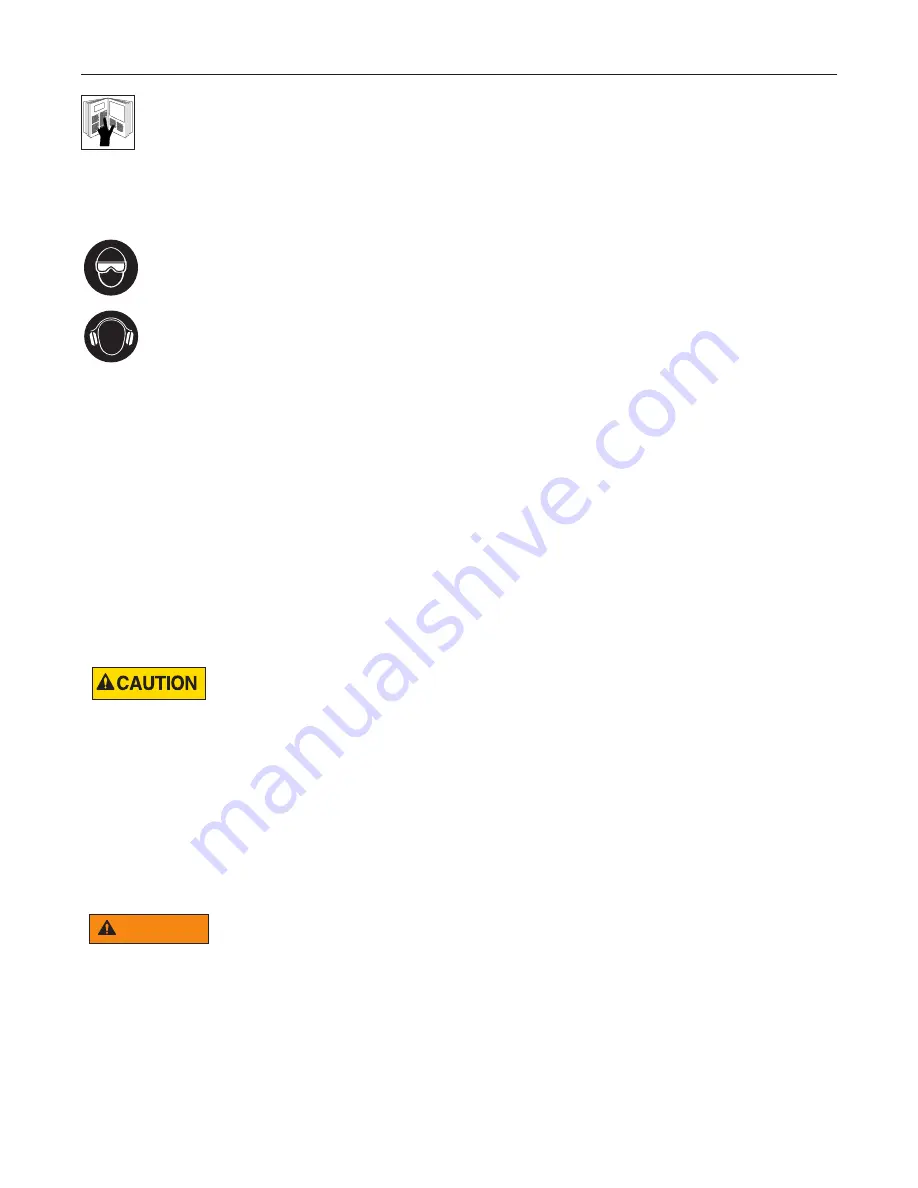
© 2014 SPX CORPORATION
9
Form No. 1000773
Rev. 0 August 12, 2014
SAFETY PRECAUTIONS CONTINUED
• Read and understand the Operating Manual before operating this equipment. For
the latest version of the instruction please visit the “Resources” page on our Web
-
site (www.PowerTeam.com)
•
IMPORTANT:
For instructions specific to the various system components refer to
the related individual manufacturer’s instructions that have been included with the
MCS.
•
IMPORTANT:
The following procedures must be performed by qualified, trained
personnel who are familiar with this equipment. Operators must read and under
-
stand all safety precautions and operating instructions included with the MCS Mo
-
tion
Control System. If the operator cannot read these instructions, operating instruc
-
tions and safety precautions must be read and discussed in the operator's native
language.
• The motion control system is designed for general use in normal environments.
These products are not designed for lifting and moving in special work environ
-
ments such as: explosive, flammable, or corrosive. Only the user can decide the
suitability of this
system for use in these conditions or extreme environments. Power Team will
supply information necessary to help make these decisions. Consult your nearest
Power Team facility.
• Safety glasses and hearing protection must be worn at all time by the operator and
anyone within sight of the unit. Additional personal protection equipment may in
-
clude: face shield, goggles, gloves, apron, hard hat, and safety shoes.
• The owner of this motion control system must ensure that safety-related decals are
installed, maintained, and replaced if they become difficult to read or understand.
• Disconnect electrical power prior to opening electrical cabinet.
To prevent operator error, perform all of the following steps to develop a
lift plan for therequirements including and especially concentrating on the controlled movement
with an assistant
operator whose sole task it is to double-check and verify any input and operational action taken
by the main operator.
IMPORTANT:
All movements to be performed by the Motion Control System must be
ordered and approved by the person responsible at the job site. SPX Power Team will assist in
operating the Motion Control System, but cannot be responsible for static or strength calcula
-
tions of the structure or load to be moved.
After setting up the MCS, the system needs to be tested for correct map
-
ping of circuit number on the screen versus displacement sensors and correlation with the
2-way valves. Extend each displacement sensor individually for approximately 100 mm and
verify the displacement
indication on the screen to show the same change of values. Set the system into “Manual”
mode and activate each circuit one by one. Verify the function of the related 2-way valve by
checking the
movement of the spool-core.
WARNING