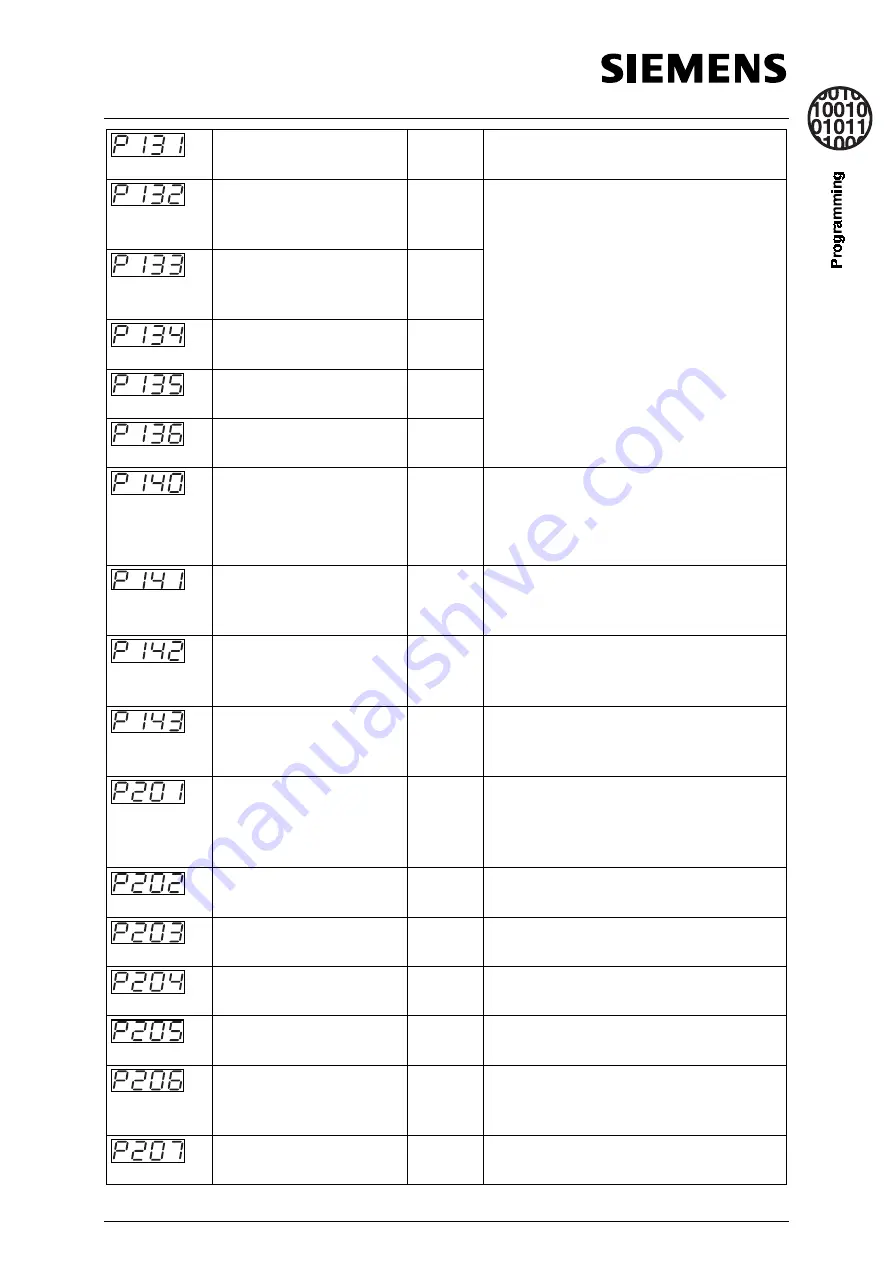
ECO REFERENCE MANUAL
13-19
Frequency setpoint (Hz)
0.0-
150.0[-]
Motor current (A)
0.0 -
300.0
[-]
Motor torque (% nominal
torque)
0 - 250
[-]
Read-only parameters. These are copies of
the values stored in P001 but can be
accessed directly via the serial link.
DC link voltage (V)
0 - 1000
[-]
Motor RPM
0 - 9999
[-]
Output voltage (V)
0 - 1000
[-]
Most recent fault code
0 - 255
[-]
Read only. The last recorded fault code (see
‘Fault Codes’) is stored in this parameter. It
is cleared when the inverter is reset.
This is a copy of the code stored in P930.
Most recent fault code -1
0 - 255
[-]
Read only. This parameter stores the last
recorded fault code prior to that stored in
P140/P930.
Most recent fault code -2
0 - 255
[-]
Read only. This parameter stores the last
recorded fault code prior to that stored in
P141.
Most recent fault code -3
0 - 255
[-]
Read only. This parameter stores the last
recorded fault code prior to that stored in
P142.
PID closed loop mode
0 - 1
[0]
0 = Normal operation (closed loop process
control disabled).
1 = Closed loop process control using
analogue input 2 as feedback.
•
P gain
0.0-999.9
[1.0]
Proportional gain.
•
I gain
0.00-99.9
[0]
Integral gain.
•
D gain
0.0-999.9
[0]
Derivative gain.
•
Integral gain scaling
1 - 2400
[1]
The integral action time is multiplied by this
value
•
Transducer filtering
0 - 255
[0]
0 = Filter off.
1 - 255 = Low pass filtering applied to
transducer.
•
Integral capture range (%)
0 - 100
[100]
Percentage error above which integral term
is reset to zero.