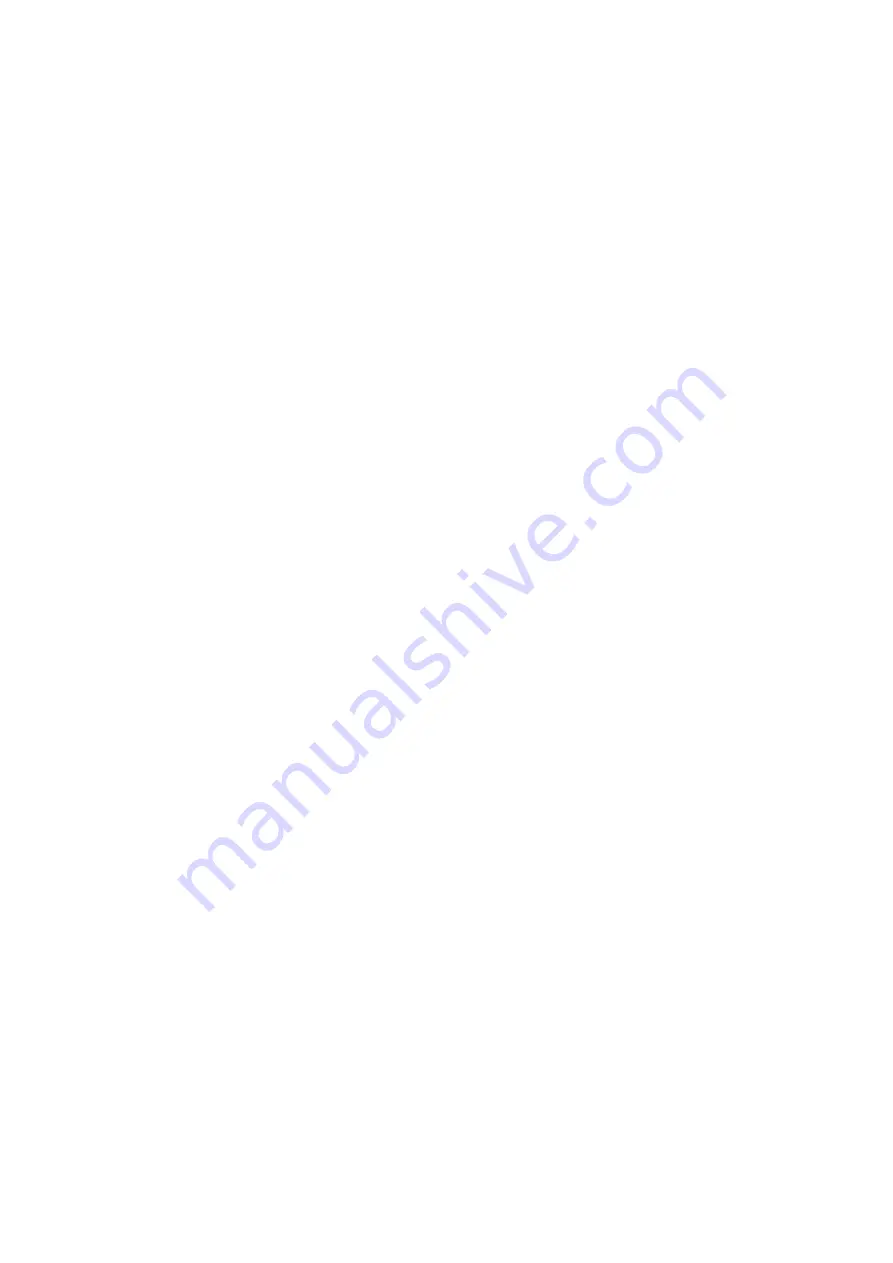
- 2 -
Contents
Before Use ....................................................................................................................... 3
Safety Precautions ........................................................................................................... 4
Product Overview ............................................................................................................. 7
Features ........................................................................................................................... 7
Names of Parts ................................................................................................................ 8
Installation ...................................................................................................................... 10
Conveyance ............................................................................................................ 10
Installation Procedure ............................................................................................. 11
Wiring Methods ....................................................................................................... 12
Attaching the Shuttle Tube ...................................................................................... 13
Attaching the Filter Case ......................................................................................... 14
Capability of This Product .............................................................................................. 15
Product Limitations ......................................................................................................... 15
Touch Panel ................................................................................................................... 16
Main Screen ................................................................................................................... 17
Sampling Method ........................................................................................................... 18
Setting the Flow Rate .............................................................................................. 18
Setting the Operation Start Timer ........................................................................... 19
Setting the Operation End Timer ............................................................................. 21
Starting Operations ................................................................................................. 23
During Operation ..................................................................................................... 24
Error Displays ......................................................................................................... 25
Power Outages .............................................................................................................. 26
Mode Display ................................................................................................................. 27
Menu .............................................................................................................................. 29
Toggling the Flow Rate Correction Method ............................................................. 29
Sampling Data ........................................................................................................ 30
Detailed Error Display ............................................................................................. 32
Setting the Time ...................................................................................................... 33
Setting the Screen .................................................................................................. 34
Setting the Serial Number ....................................................................................... 34
Setting the Error ...................................................................................................... 35
Calibration Mode ..................................................................................................... 36
Leak Check ............................................................................................................. 37
Calibration Methods ....................................................................................................... 38
Flow Rate Calibration Method ................................................................................. 38
Atmospheric Temperature Calibration Method ........................................................ 38
Atmospheric Pressure Calibration .......................................................................... 39
Flow Rate Correction Method ........................................................................................ 40
Communications ............................................................................................................ 40
Maintenance ................................................................................................................... 41
Troubleshooting .............................................................................................................. 42
Main Specifications ........................................................................................................ 43
Spare Parts .................................................................................................................... 44
Consumables ................................................................................................................. 44
Options ........................................................................................................................... 44
Warranty and Repair ...................................................................................................... 45
Disposal of the Product .................................................................................................. 46
Inquiries .......................................................................................................................... 46
Trouble Notification Sheet .............................................................................................. 47