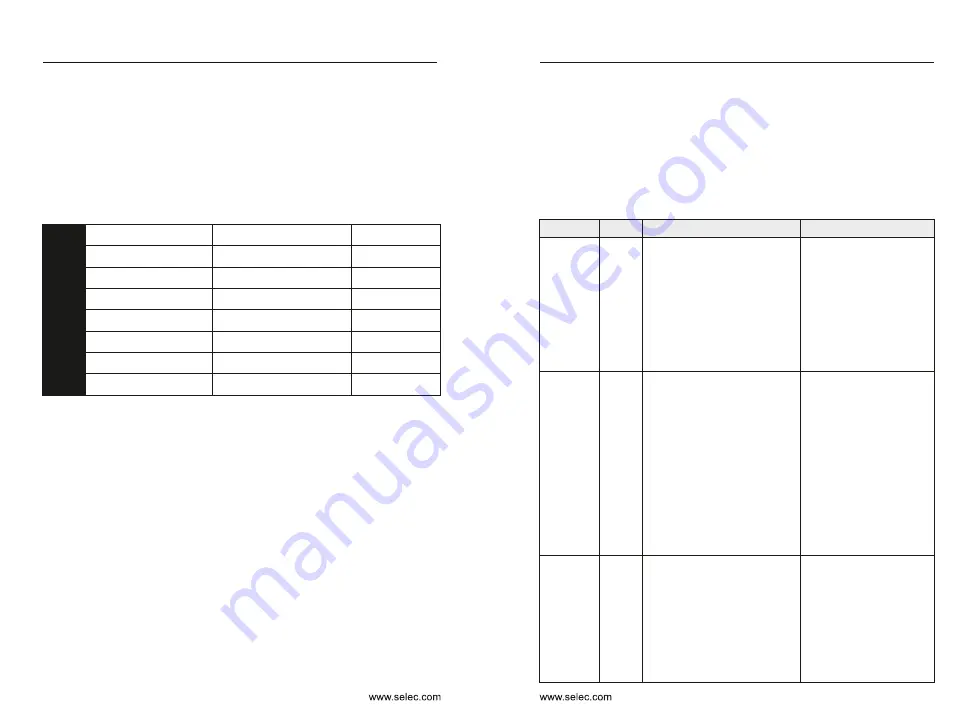
User Manual
158
User Manual
Chapter 7
159
Actual measurement of AI1 voltage value, stored in function parameters
AC-02
Given AI1 voltage signal (about 8V)
For AI1 and AI2, it is recommended to use 2V and 8V as the calibration
point pair AI3. It is recommended to sample -8V and 8V as the correction
point.
When AI2 and AI3 are corrected, the actual sampling voltage viewing
positions are U0-22 and U0-23 respectively.
View U0-21 display value, save function parameters AC-03
AC-12
AO1 target voltage 1
0.500V
〜
4.000V
factory reset
AO1 measured voltage 1
0.500V
〜
4.000V
factory reset
AO1 target voltage 2
6.000V
〜
9.999V
factory reset
AO1 measured voltage 2
6.000V
〜
9.999V
factory reset
AO2 target voltage 1
0.500V
〜
4.000V
factory reset
AO2 measured voltage 1
0.500V
〜
4.000V
factory reset
AO2 target voltage 2
6.000V
〜
9.999V
factory reset
AO2 measured voltage 2
6.000V
〜
9.999V
factory reset
AC-13
AC-14
AC-15
AC-16
AC-17
AC-18
AC-19
AI2 measured current 1
0.000mA
〜
20.000mA
factory reset
AI2 sampling current 1
0.000mA
〜
20.000mA
factory reset
AI2 measured current 2
0.000mA
〜
20.000mA
factory reset
AI2 sampling current 2
0.000mA
〜
20.000mA
factory reset
AO1 ideal current 1
0.000mA
〜
20.000mA
AO1 measured current 1
0.000mA
〜
20.000mA
AO1 ideal current 2
0.000mA
〜
20.000mA
AO1 measured current 2
0.000mA
〜
20.000mA
AC-20
AC-21
AC-22
AC-23
factory reset
factory reset
factory reset
factory reset
AC-24
AC-25
AC-26
AC-27
This set of function codes is used to correct the analog output AO.
The function parameters of this group have been corrected at the factory.
When the default is restored, it will be restored to the factory-corrected value.
Generally no correction is required at the application site.
The target voltage is the theoretical output voltage value of the inverter.
The measured voltage refers to the actual output voltage measured by an
instrument such as a multi-meter.
7-1 Fault alarm and Solutions
FAULTS AND SOLUTIONS
When the inverter fails during operation, the inverter will immediately
protect the motor from output, and the inverter fault relay contact will act and
display the fault code on the inverter display panel. Before seeking service,
users can perform self-checking according to the tips in this section to
analyze the cause of the fault. If the fault cannot be solved, please seek
technical support from our company or product agent.
Fault name Display
Troubleshoot the cause
Solutions
Inverter
unit
protection
Err01
Over-
current
during
acce-
leration
Err02
Over-
current
during
dece-
leration
Err03
1: The output circuit is grounded
or short circuited.
2: The connecting cable of the
motor is too long.
3: The IGBT overheats.
4: The internal connections
become loose.
5: The main control board is
faulty.
6: The driver board is faulty.
7: The AC drive IGBT is faulty.
1: Eliminate external faults.
2: Install a reactor or an
output filter.
3: Check the air filter and
the cooling fan.
4: Connect all cables
properly
5: Contact the agent or
company to support
1: The output circuit is grounded
or short circuited.
2: Motor auto-tuning is not
performed.
3: The acceleration time is too
short.
4: Manual torque boost or V/F
curve is not appropriate.
5: The voltage is too low.
6: The startup operation is
performed on the rotating motor.
7: A sudden load is added during
acceleration.
8: The inverter model is of too
small power class.
1: Eliminate external faults.
2: Perform the motor auto-
tuning.
3: Increase the acce-
leration time.
4: Adjust the manual torque
boost or V/F curve.
5: Adjust the voltage to
normal range.
6: Select rotational speed
tracking restart or start the
motor after it stops.
7: Remove the added load.
8: Select an inverter of
higher power class.
1: The output circuit is grounded
or short circuited.
2: Motor auto-tuning is not
performed.
3: The deceleration time is too
short.
4: The voltage is too low.
5: A sudden load is added during
deceleration.
6: The braking unit and braking
resistor are not installed.
1: Eliminate external faults.
2: Perform the motor auto-
tuning.
3: Increase the deceleration
time.
4: Adjust the voltage to
normal range.
5: Remove the added load.
6: Install the braking unit
and braking resistor.
Chapter 6