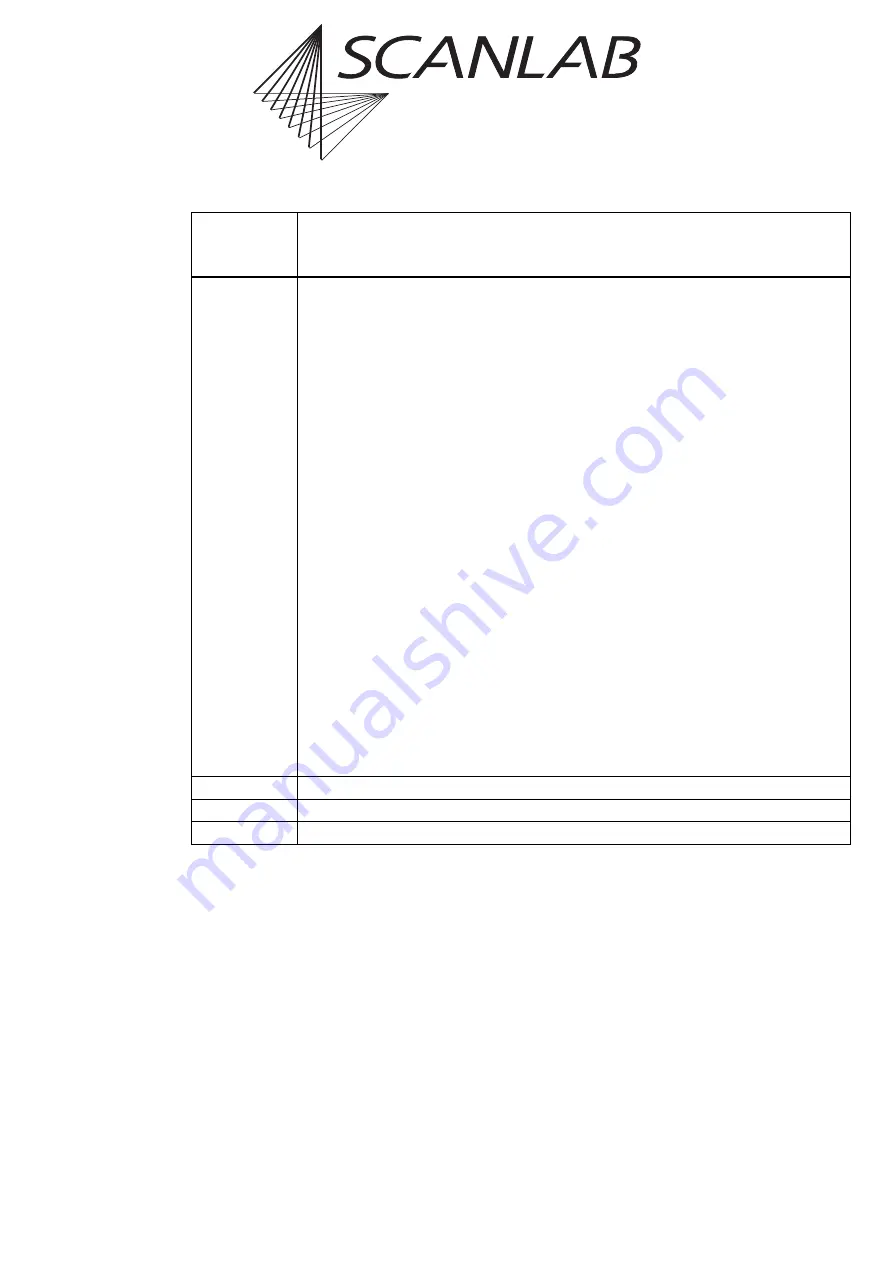
RTC
®
5 PC Interface Board
Rev. 1.9 e
10 Commands And Functions
384
innovators for industry
Comments
• No monitoring takes place if the specified scan head does not have a correction table
assigned (see
).
• The used position limits (that is, if exceeded the emergency action is executed) are the
parameters of a customer-specific Processing-on-the-fly application monitoring (see
). Exceeding these limits only cause error messages in
case of Processing-on-the-fly applications. The error messages can be queried with
if_fly_<axis>_overflow
/
if_not_fly_<axis>_overflow
commands. They do not trigger
any activities.
• Processing-on-the-fly applications use the data type
Data
= 0 (sample values) for
customer-specific range limits. Inconsistent error messages and switch-offs may occur
if used simultaneously with
range_checking
data types
Data
> 0.
• The
range_checking
monitoring is active without Processing-on-the-fly application.
•
Data
RTC5_PARAM_ERROR
error code. In this case the
command is sent to the RTC
®
5 board as
.
•
Data
=2 and
Data
=3 have the identical effect for the Z axis.
• For
Data
= 4 and
Data
= 5 the user must define the set position as the to be returned
data type. A simultaneous use of a speed-dependent laser control with
Mode
= 2 (see
) is not possible.
•
Data
= 4 and
Data
= 5 only differ in regards to the axis onto an optional vario
SCAN
is
connected. For 2D systems without vario
SCAN
both selections have the identical effect.
•
Data
= 4 und
Data
= 5 may produce nonsensical switch-offs if an intelli
SCAN
®
is
connected but is either not switched-on or a real position has not been set as feedback.
• If the laser has been switched-off with
Mode
= 0 and the fault condition is gone then
the laser is
not
switched on until the next marking command. The laser is
not
switched-
on right in the middle of a currently executing marking command.
RTC
®
4
RTC
®
5 new command
Version info
Available beginning with version DLL 537, OUT 537
References
Undelayed
Short List
Command
range_checking