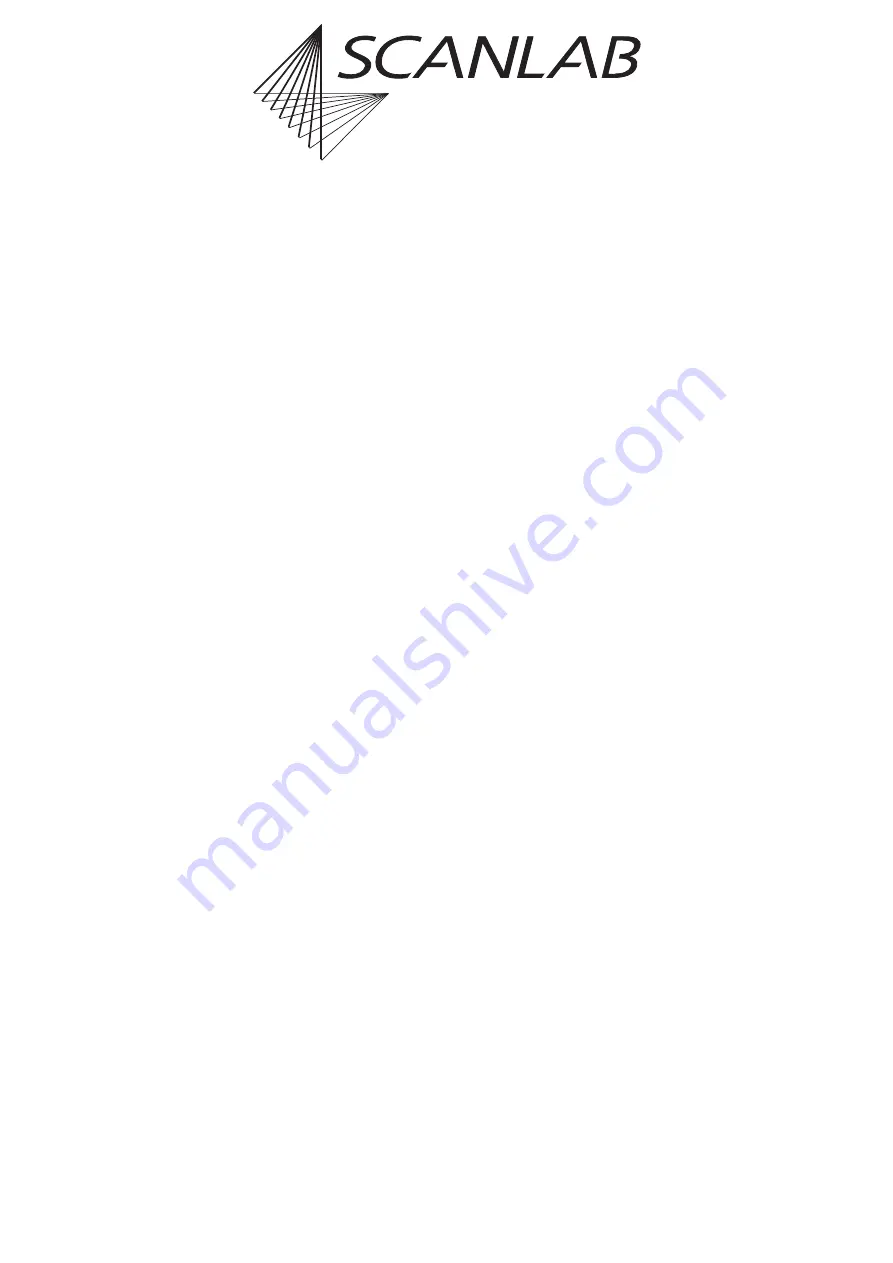
RTC
®
5 PC Interface Board
Rev. 1.9 e
7 Basic Functions for Scan Head and Laser Control
140
innovators for industry
7.4.9 Automatic Laser Control
Automatic laser control commands can be used to
achieve automatic readjustment of “laser active”
laser control signals – and thus of the laser power –
even during execution of vector and arc commands.
On the one hand, this allows compensation of laser
impact variations (and thus variations in the
processing results) arising from (e.g.) changes in
power density, spot size or processing speed, even for
constant predefined laser power. In marking
processes, for example, this compensation results in
more uniform marking strength and more uniform
line widths during hatching. On the other hand, the
laser impact along a vector can also be deliberately
readjusted. e.g. to achieve the desired weldseam
shape in laser welding applications.
The automatic laser control commands supplement
commands described in the preceding sections of this
chapter, such as
constant
laser power for subsequent mark and arc commands.
For automatic laser control, a position-dependent,
speed-dependent or vector-defined correction of
laser control signals can be activated (these three
correction possibilities can also be freely combined
with each other). Here, the selected laser control
signals are readjusted in accordance with scanning
movements of the scan system. As an alternative to
(galvanometer scanner-) speed-dependent laser
control, encoder-speed-dependent correction
(combinable with position-dependent and vector-
defined laser control) can be enabled.
• With
position-dependent
laser control (see
), position-dependent (radial) variations
in laser impact can be compensated during
execution of vector and arc commands. Such
variations may occur, for example, from optical
system aberrations (e.g. objective edge
diminution, i.e. power losses at the objective
edge). Depending on the optical system, varia-
tions may also occur for a non-perpendicular
incidence of the laser beam at the processed
material (i.e. angles of incidence larger than zero)
for increasing distances to the image field center
– which alters the reflection and the laser spot.
Position-dependent laser control allows
definition of an automatic radial correction
(dependent on the distance to the image field
center).
•
Speed-dependent
laser control (see
)
allows compensation of speed-dependent varia-
tions in laser impact during execution of vector
and arc commands. Such variations can occur if
the speed changes during a mark command or
across multiple mark commands – for example:
– resulting from acceleration or deceleration
scanner motions at the beginning or end of a
vector or from directional changes within a
polyline
– resulting from automatic readjustment to the
10
µ
s clock of the stepwidth and effective
marking speed (short-vector jitter)
– with timed mark commands resulting from the
automatic readjustment of the marking speed
in accordance with the predefined marking
duration (timed mark commands allow avoid-
ance of effects, such as fluttered edges at the
vector’s end, that might occur with normal
mark commands)
•
Vector-defined
allows linear readjustment of a laser signal
parameter along a mark or jump vector. This
allows, for example, to compensate laser impact
variations along a vector on uneven material
surfaces (resulting from an angle of incidence
that varies along the vector)
•
Encoder-speed-dependent
laser control (see
), allows the laser impact to be
controlled based on the current encoder speed
(counter pulses in the most recent 10
µ
s interval)
of an encoder counter, e.g. corresponding to the
current conveyance speed of a transport system
(and therefore to the speed of the workpiece).
Selectively, automatic laser control adjusts one of the
following signal parameters:
• the 12-bit output value at the ANALOG OUT1 or
ANALOG OUT2 analog output ports of the 15-pin
D-SUB LASER connector (also see
)
• the output value at the 16-bit digital TTL output
of the EXTENSION 1 connector (also see
• the output value at the 8-bit digital output port
of the EXTENSION 2 connector (also see
• the pulse length (
PulseLength
) or output period
(
HalfPeriod
) of the laser signals LASER1 and
LASER2
• Only for vector-defined laser control: focus shift
for subsequent parameterized vector output
(requires enabling the 3D option as well as
loading and assigning a 3D correction file)