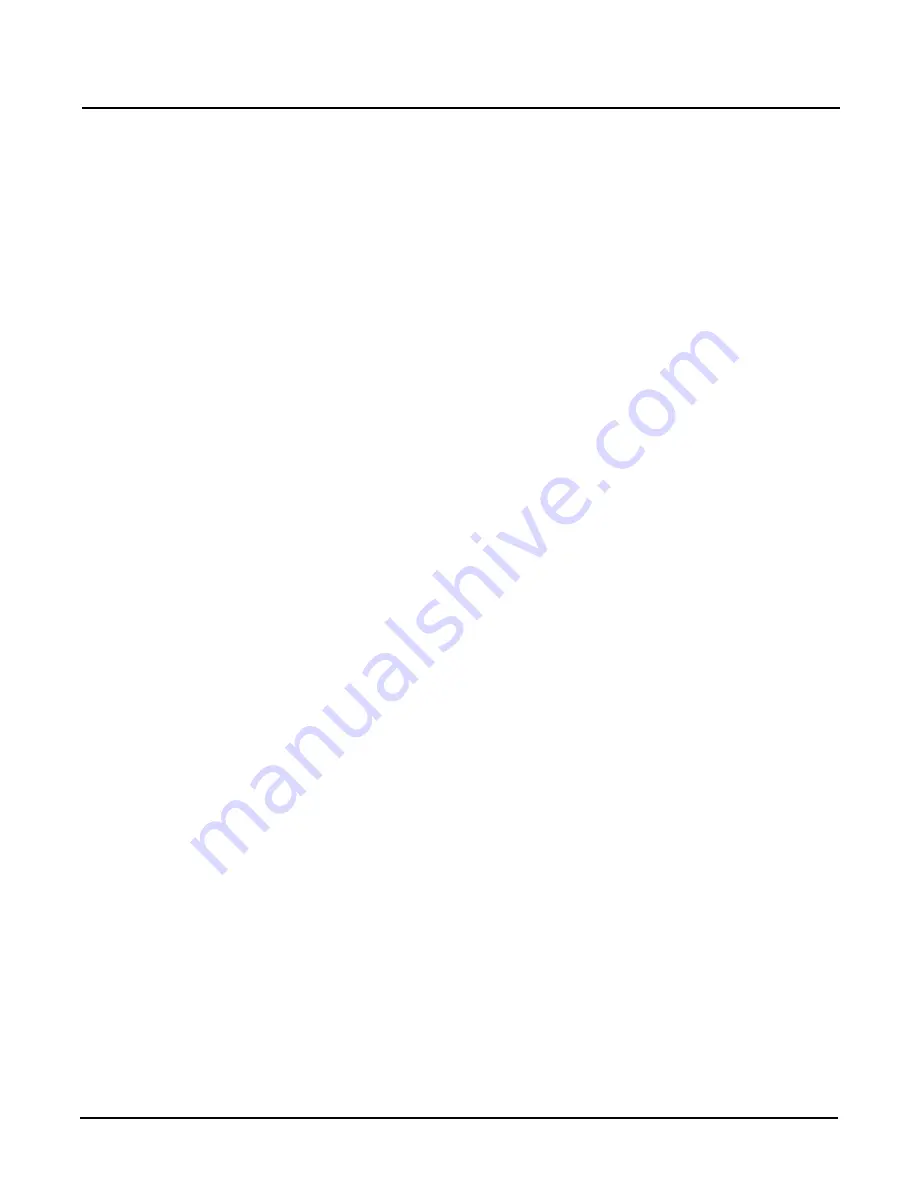
SY265C LC/SY265C LR Excavator OMM
5-18
Operation and Maintenance Manual — 0420
SANY
•
Clean and check the upper structure and undercarriage. (See page 5-109.)
•
Check the swing grease bath level. (See page 5-98.)
•
Check the swing drive fasteners. (See page 5-97.)
•
Lubricate the swing drive bearing. (See page 5-90.)
•
Check the final drive. (See page 5-87.)
•
Check the hydraulic pump. (See page 5-80.)
•
Check the hydraulic hoses and lines. (See page 5-76.)
•
Check the radiator, hydraulic oil cooler, and air conditioner condenser fins. (See page 5-46.)
•
Check the air conditioner fresh-air and recirculation filters. (See page 5-50.)
•
Replace the hydraulic system breather filter. (See page 5-69.)
•
Change the engine oil and filter. (See page 5-37.)
•
Replace the primary and secondary engine air filter. (See page 5-34.)
•
Replace the swing drive oil. (See page 5-93.)
•
Check the stationary regeneration. (See page 3-19.)
Every 6 Months or 1000 Hours
NOTE:
Make sure all daily, 50-hour, 250-hour, and 500-hour maintenance tasks have been completed before
proceeding with the 1000-hour maintenance tasks.
•
Check accumulator function. (See page 5-66.)
•
Check the fuel tank strainer. (See page 5-59.)
•
Replace the hydraulic pilot filter element. (See page 5-71.)
•
Replace the hydraulic return filter. (See page 5-73.)
•
Check the fuel lines. (See page 5-56.)
•
Check the aftertreatment exhaust piping. (See page 5-42.)
•
Replace the diesel exhaust fluid (DEF) tank filter. (See page 5-43.)
Annually or Every 2000 Hours
NOTE:
Make sure all daily, 50-hour, 250-hour, 500-hour, and 1000-hour maintenance tasks have been
completed before proceeding with the 2000-hour maintenance tasks.