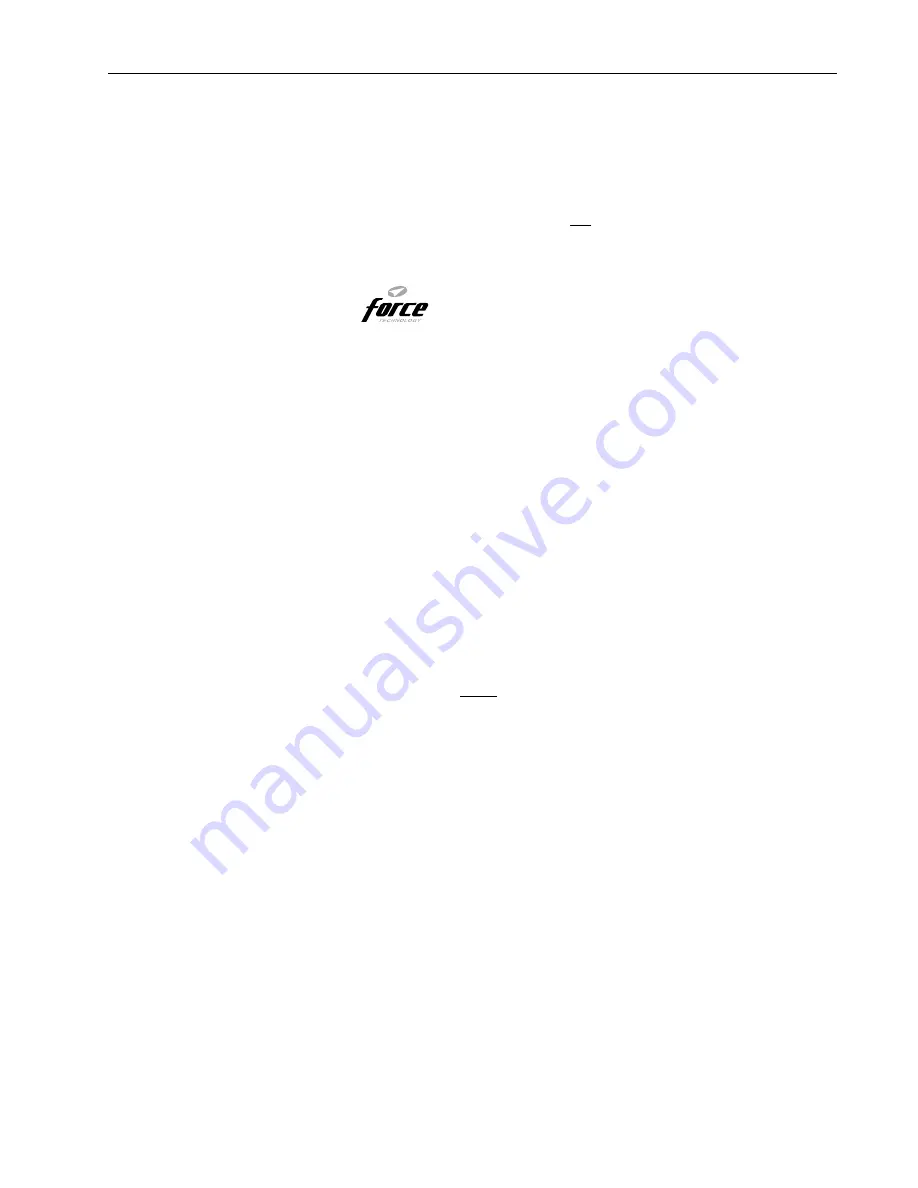
Application Notes
B-3
Vector Control can operate in one of two configurations:
1.
Encoderless
Not to be confused with Sensorless Vector above, Encoderless Vector
based on Allen-Bradley’s patented Field Oriented Control technology
means that a feedback device is not required. Torque control can be
achieved across a significant speed range without feedback.
2.
Closed Loop (with Encoder)
Vector Control with encoder feedback utilizes Allen-Bradley’s Force
Technology™. This industry leading technology allows the drive to
control torque over the entire speed range, including zero speed. For
those applications that require smooth torque regulation at very low
speeds or full torque at zero speed, Closed Loop Vector Control is the
answer.
Speed Regulators
Any of the PowerFlex drives, regardless of their motor control technology
(Volts/Hz, Sensorless Vector or Vector) can be set up to regulate speed.
Speed regulation and torque regulation must be separated to understand
drive operation.
The PowerFlex 70/700 with Standard Control and the PowerFlex 700H can
be programmed to regulate speed using the slip compensation feature. Slip
compensation reacts to load changes by adjusting the drive output frequency
to maintain motor speed. Torque production operates independently. This
feature produces speed regulation of about 0.5% of base speed over a
specified speed range (40:1 for V/Hz and 80:1 for Sensorless Vector). These
drives do not have the capability to extend the speed range or tighten the
speed regulation below 0.5% because they do not have connections for a
feedback device.
Motor Overload
For single motor applications the drive can be programmed to protect the
motor from overload conditions. An electronic thermal overload I
2
T
function emulates a thermal overload relay. This operation is based on three
parameters; [Motor NP FLA], [Motor OL Factor] and [Motor OL Hertz]
(parameters 042, 048 and 047, respectively).
[Motor NP FLA] is multiplied by [Motor OL Factor] to allow the user to
define the continuous level of current allowed by the motor thermal
overload. [Motor OL Hertz] is used to allow the user to adjust the frequency
below which the motor overload is derated.
The motor can operate up to 102% of FLA continuously. If the drive had
just been activated, it will run at 150% of FLA for 180 seconds. If the motor
had been operating at 100% for over 30 minutes, the drive will run at 150%
Содержание powerflex 700h
Страница 1: ...PROGRAMMING MANUAL High Power Firmware Versions x xxx 3 001 PowerFlex 700H AC Drives ...
Страница 10: ...P 4 Overview Notes ...
Страница 56: ...2 42 Programming and Parameters Notes ...
Страница 70: ...3 14 Troubleshooting Notes ...
Страница 103: ......