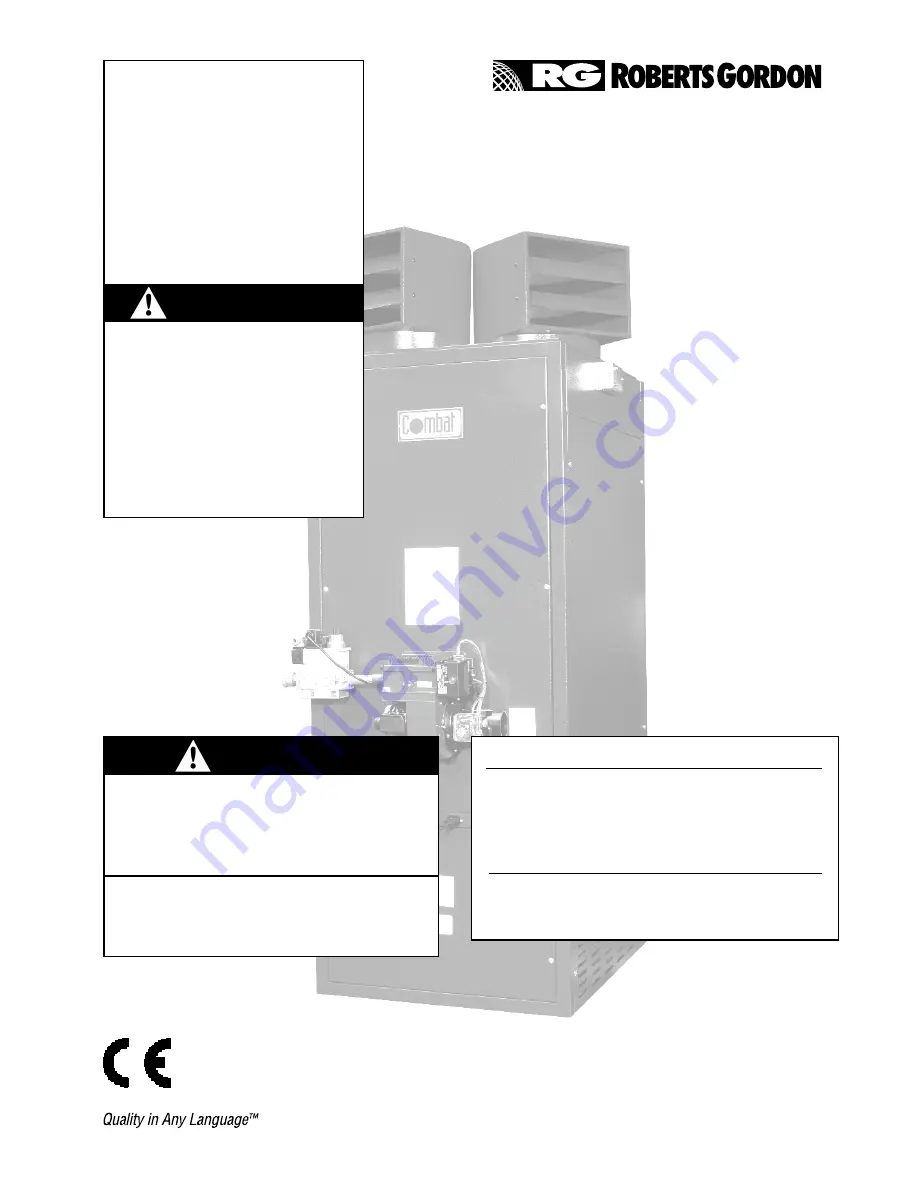
FOR YOUR SAFETY
If you smell gas:
1. Open windows.
2. DO NOT try to light any appliance.
3. DO NOT use electrical switches.
4. DO NOT use any telephone in
your building.
5. Leave the building.
6. Immediately call your local gas
supplier after leaving the building.
Follow the gas suppliers
instructions.
Do not store or use petrol or other
flammable vapours and liquids in the
vicinity of this or any other appli-
ance.
Failure to follow these instructions
can result in death, injury or property
damage.
WARNING
Improper installation, adjustment, alteration,
service or maintenance can result in death, injury
or property damage. Read the Installation,
operation and service manuals thoroughly before
installing or servicing this equipment
Installation must be done by a contractor qualified
in the installation and service of gas/oil fired
heating equipment (whichever is applicable).
Installer
Please take time to read and understand these
instructions prior to any installation. Installer must
give a copyof this manual to the user/owner.
Owner/User
Keep this manual in a safe place close to the heater
to provide your serviceman with information should it
become necessary.
Roberts-Gordon Europe Ltd.
Oxford Street
Bilston, West Midlands WV14 7EG UK
Telephone: +44 (0)1902 494425
Fax: +44 (0)1902 403200
email: [email protected]
www.combat.co.uk
www.rg-inc.com
Combat
®
Warm Air Cabinet
& High-Flow Heaters
OIL FIRED: POP, POPH and
POP /H versions
Models 015 to 0100
GAS FIRED: PGP, PGPH and
PGP /H/M versions
Models 015 to PGP 0100
Installation, Commissioning,
Service & User Instructions
WARNING
Fire Hazard
X523F 02/03
© Copyright 2002 Roberts-Gordon
Содержание Combat HF 30 v4
Страница 2: ......
Страница 47: ...Page 45 CABINET HEATER Section 6 Wiring Diagrams Fig 6 1 As Wired Diagram for Models 015 to 030 Floor Standing ...
Страница 48: ...Page 46 CABINET HEATER Fig 6 2 As Wired Diagram for Models 015 to 030 Horizontal Mounting ...
Страница 49: ...Page 47 CABINET HEATER Fig 6 3 As Wired Diagram for Models 040 and 050 Floor Standing ...
Страница 50: ...Page 48 CABINET HEATER Fig 6 4 As Wired Diagram for Models 040 050 Horizontal Mounting ...
Страница 51: ...Page 49 CABINET HEATER Fig 6 5 As Wired Diagram for Models 060 to 0100 Floor Standing ...
Страница 52: ...Page 50 CABINET HEATER Fig 6 6 As Wired Diagram for Models 060 to 0100 Horizontal Mounting ...
Страница 55: ...Page 55 CABINET HEATER Fig 6 12 Wiring Diagram for High Flow Models HF40 v3 HF50 v2 HF50 v3 and HF50 v4 ...