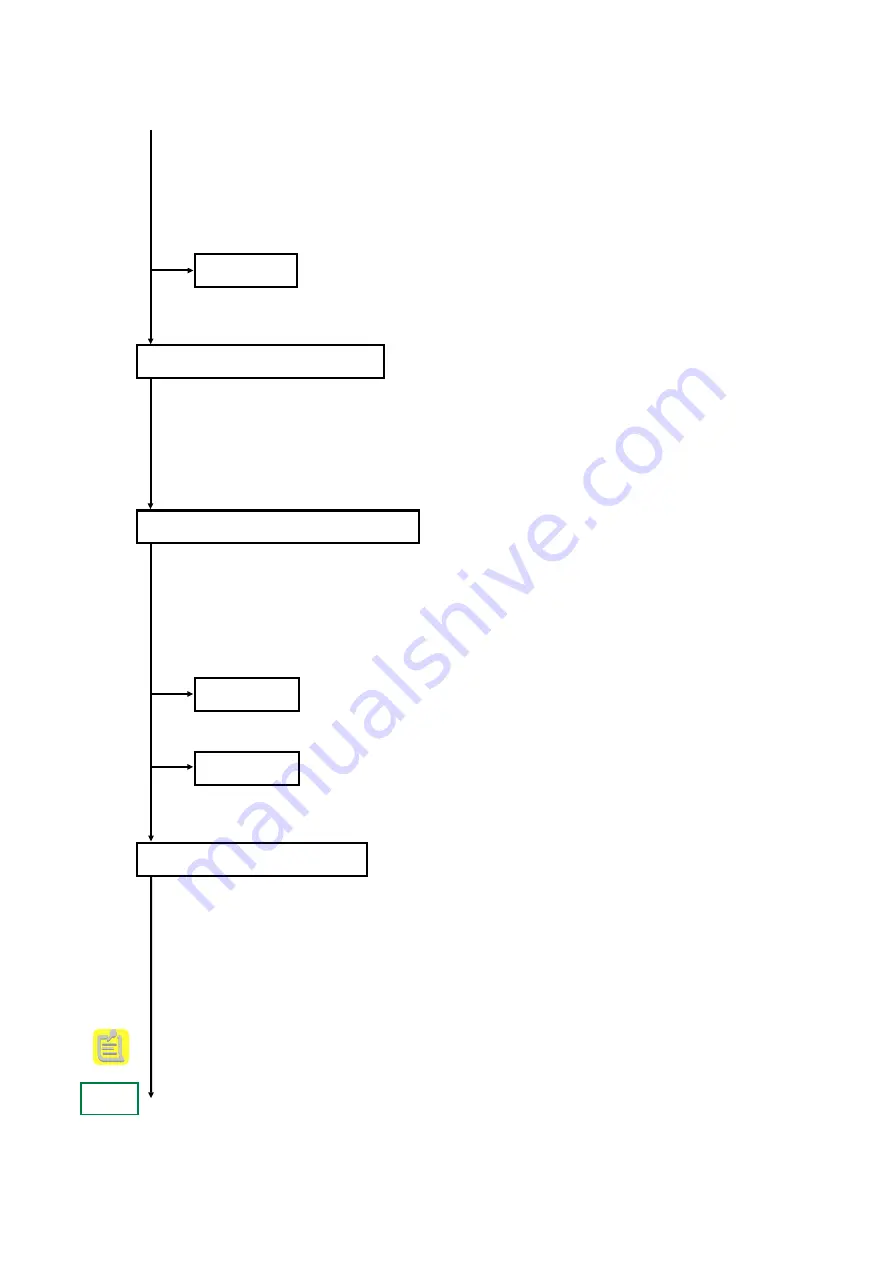
5. Clean the drum potential sensor and the drum thermistor using a
dry cloth or blower brush.
6. Clean the erase lamp, the QL filter, and the ID sensor using water.
7. Clean the pick-off pawls with alcohol.
Every 1.2M
1. Replace the ozone filter.
7. Cleaning Unit (every 150K)
1. Clean inside the unit.
2. Clean and inspect the entrance seal, the side seals, and the
cleaning filter.
3. Replace the cleaning blade, the flick blade, and the cleaning brush.
8. Development Unit (every 150K)
1. Clean the upper seal, the sleeve drive gear, and the timing belt
pulley.
2. Inspect the toner cartridge seals, the sleeve side seals, and toner
near end sensor feeler movement.
3. Replace the development filter, and the duct filter.
Every 300K
1. Replace the developer.
Every 600K
1. Replace the sleeve side seals and the sleeve drive gears.
9. Fusing Unit (every 150K)
1. Inspect the bushings and bearings of the hot and pressure rollers.
2. Inspect and clean the stripper pawls using a suitable solvent.
3. Clean the guide plates, the de-curling roller, and resin transport
rollers using a suitable solvent.
4. Clean the de-curling belt and the rubber transport rollers using
alcohol.
5. Clean the oil supply roller bushings using a suitable solvent.
6. Replace the oil supply roller.
31 July 1995
PREVENTIVE MAINTENANCE SCHEDULE
4-47
Содержание FT8680
Страница 3: ...SECTION 1 OVERALL MACHINE INFORMATION ...
Страница 8: ...MEMO 31 July 1995 SPECIFICATIONS 1 5 ...
Страница 23: ...6 5 IMAGE OVERLAY MODE 2ND SIDE A171V505 wmf PAPER PATH 31 July 1995 1 20 ...
Страница 24: ...SECTION 2 DETAILED SECTION DESCRIPTIONS ...
Страница 133: ...Timing Chart 1 Stack 2 Paper Feed A171D551 wmf A171D552 wmf 31 July 1995 DUPLEX 2 109 ...
Страница 159: ...SECTION 3 INSTALLATION ...
Страница 177: ...SECTION 4 SERVICE TABLES ...
Страница 229: ...SECTION 5 REPLACEMENT AND ADJUSTMENT ...
Страница 362: ...SECTION 6 TROUBLESHOOTING ...