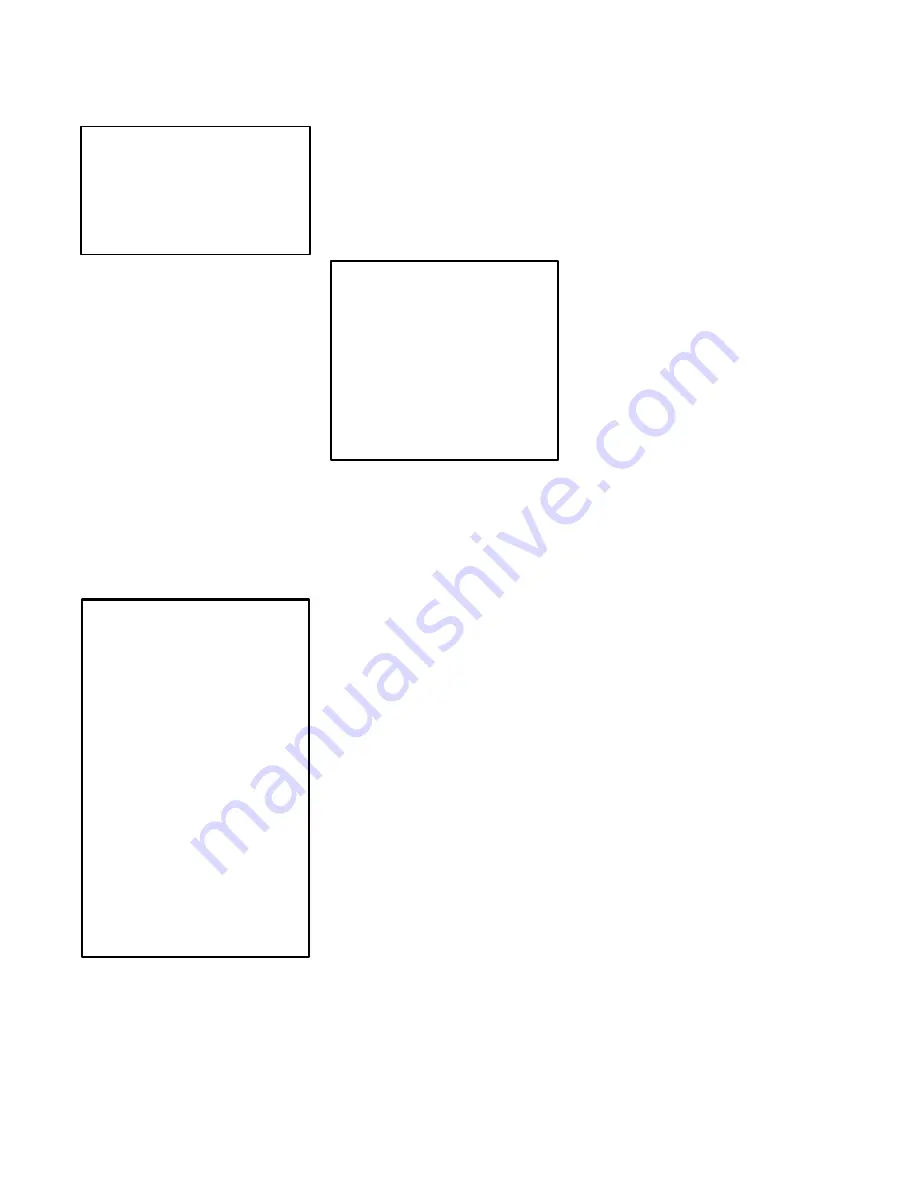
4:10
Perform Startup Procedure 2
with Motor Coupled
CAUTION
Do not perform Procedure 2
before Procedure 1. Failure to
observe this precaution could
result in damage to, or destruc-
tion of, the equipment.
1.
Determine the regulator mode
necessary for your application:
speed regulator, torque
regulator, or position regulator.
2.
Proceed to the section
corresponding to the selected
regulation mode:
•
“Perform Startup in Speed
Regulator Mode,”
•
“Perform Startup in Torque
Regulator Mode,” or
•
“Perform Startup in Position
Regulator Mode.”
Perform Startup in Speed
Regulator Mode
WARNING
THIS DRIVE IS CAPABLE OF
OPERATING AT AND MAIN-
TAINING ZERO SPEED. THE
USER IS RESPONSIBLE FOR
ASSURING SAFE CONDI-
TIONS FOR OPERATING
PERSONNEL BY PROVID-
ING SUITABLE GUARDS
AND AUDIBLE OR VISUAL
ALARMS OR OTHER DE-
VICES TO INDICATE THAT
THE DRIVE IS OPERATING
OR MAY BE OPERATING AT
OR NEAR ZERO SPEED.
FAILURE TO OBSERVE
THESE PRECAUTIONS
COULD RESULT IN BODILY
INJURY.
This procedure requires a digital
voltmeter and an oscilloscope.
1.
Make sure all power is OFF.
The POWER LED should not
be illuminated.
2.
Couple the motor to the
machine or load.
3.
Remove Speed reference
circuit from Procedure 1 and
wire any necessary inputs or
outputs to the controller for
proper machine operation in
the Speed Regulator mode.
4.
With power OFF, verify the
regulator switches are set as
shown in Figure 4-6.
DANGER
THE REMAINING STEPS
ARE MADE WITH POWER
ON. EXERCISE EXTREME
CARE BECAUSE HAZARD-
OUS VOLTAGE EXISTS.
FAILURE TO OBSERVE THIS
PRECAUTION COULD RE-
SULT IN SEVERE BODILY
INJURY OR LOSS OF LIFE.
5.
With the Speed reference at
minimum, turn power ON.
Note:
The POWER ON and the
RDY LEDs should illuminate.
6.
Place a digital voltmeter (20
VDC scale) on 2CN pin
connectors 8(+) and 23
(COM).
Note:
This analog D-C signal is
proportional to speed.
7.
Adjust the SZ pot until the
voltmeter reads zero. The SZ
LED should illuminate.
8.
Give the controller a Start
command. The RUN LED
should illuminate.
9.
Increase the Speed reference
to maximum. The motor will
accelerate to the maximum
speed setting.
10. Connect a digital voltmeter to
2CN connector pins 8(+) and
24 (COM) to monitor speed
output. Verify that the digital
voltmeter reads 4.8 VDC
maximum speed.
11. If the meter does not read 4.8
VDC or a different maximum
speed is required, adjust the
SR pot until the proper speed
is reached. The SR test point
will read 8.0 VDC at 2000
RPM.
If a
faster maximum speed
is
required:
•
Turn the SR pot CW until the
proper maximum speed is
reached. If the controller
IETs and the SFB LED
illuminates, the over-speed
trip point has been
exceeded.
•
Turn the OS pot 1/8 turn
CW.
•
Push the Reset pushbutton
(4SW).
•
The POWER ON, the RDY,
and the SZ LEDs should
illuminate.
•
Repeat this Step until the
desired speed is reached.
If a
slower maximum speed
is required:
•
Turn the SR pot CCW until
the proper maximum speed
is reached.
•
Turn the OS pot CCW until
the controller IETs and the
SFB LED illuminates.
•
Turn the OS pot 1/8 turn
CW.
•
Remove the Speed
reference input.
•
Push the Reset pushbutton
(4SW).
12. Run the controller at
approximately 50% speed.
13. If an audible high frequency
motor noise or motor vibration
is present (that was not
present when the motor was
not coupled to the load), the
notch filter may be required.
14. Readjust SZ per Step 7.
15. If the ramp generator is used:
Note:
Ramp generator works with
differential inputs only.
Artisan Technology Group - Quality Instrumentation ... Guaranteed | (888) 88-SOURCE | www.artisantg.com