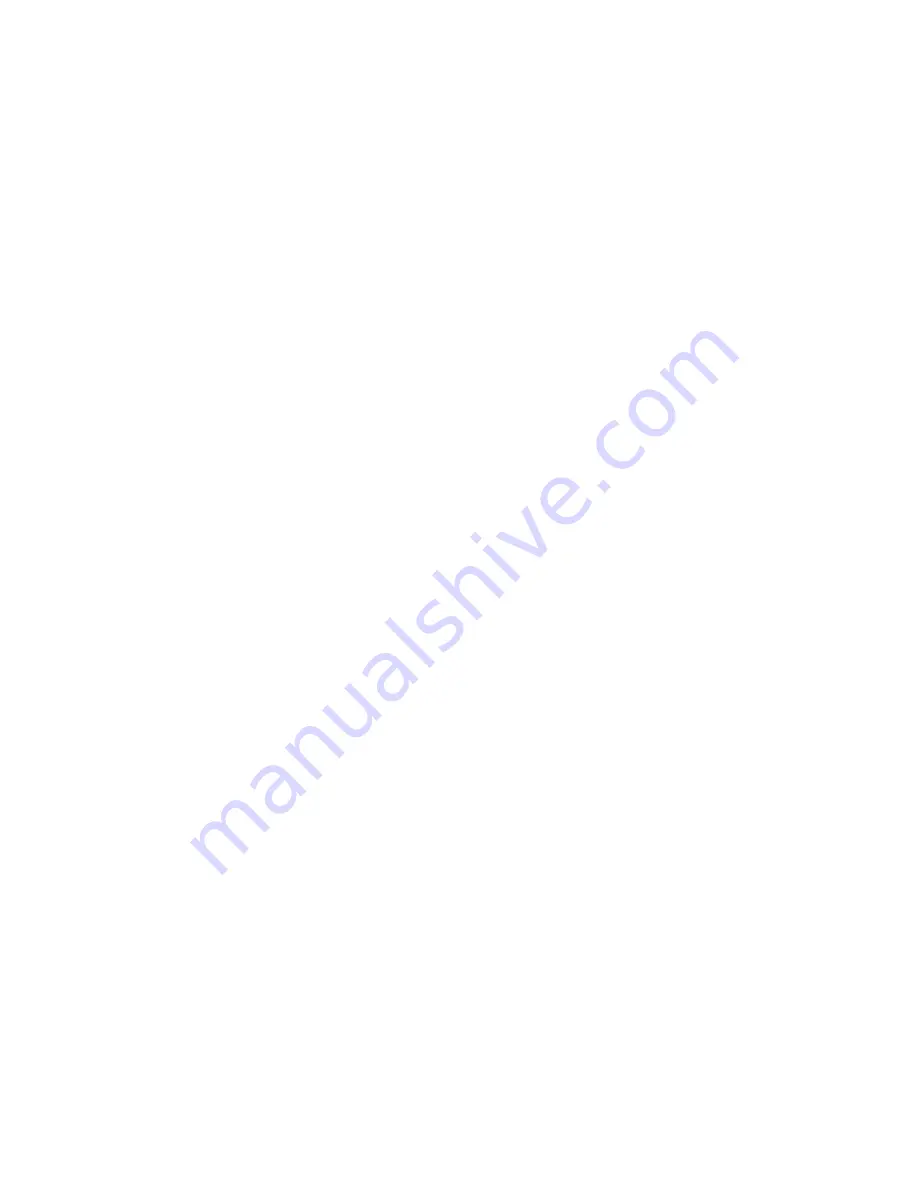
5:1
5: Understand How
the Controller Operates
Fundamentals of the
HR2000 Controller and
the Motor
The drive system consists of an
electronic controller and a
permanent magnet A-C motor.
The controller consists of two
major sections: a power section
and a regulator section. The motor
consists of a three-phase wound
stator, a permanent magnet rotor,
and a shaft-mounted optical
encoder. Refer to the functional
block diagram in Figure 5-3.
Input power is applied to terminals
181(R), 182(S), and 183(T) on the
controller faceplate. From these
terminals, power branches to a
control transformer that supplies
the low voltage power required for
the regulator and a cooling fan.
Input power also feeds the diode
bridge. Input diodes convert
three-phase A-C power to nominal
310-volt D-C power. A Hall
transductor monitors this D-C
power for high D-C bus output
currents. The regulator in the IET
circuit monitors the Hall
transductor, which, when large
output currents are sensed, will
remove power from the motor by
removing base voltage to the
output transistors.
After bus filter capacitor voltage
reaches a predetermined level, the
precharge relay bypasses or
shunts the precharge resistor
ensuring a soft start on power up.
The D-C bus then feeds a bridge
of six output transistors. The sine
wave PWM output of the
transistors powers the motor. The
Hall transductor, having outputs
monitored by the regulator for sine
wave current control and for
current limit of the controller
output, also monitors two of the
three output phases.
The run, reset, proportional/
proportional plus integral loop, and
shaft clamp inputs are all optically
isolated. These inputs are fed into
the microprocessor for monitoring
of their functions.
The notch filter frequency
bandwidth, inverse time overload,
overspeed trip, and the positive
gain pots are fed into the
microprocessor for setting and
monitoring. Analog reference
inputs are directed into the
regulator speed and torque loops.
The controller also has three
optically isolated outputs that
indicate ready to run, position
error, and minimum speed.
The controller has three user
reference inputs: a differential
input that feeds a linear voltage
time unit (LVTU) circuit and two
single-ended inputs. The LVTU
ramp circuit may be
disabled/enabled by using jumper
J2. The output of the LVTU circuit
feeds a summing amplifier, which
is also fed by a Test mode
reference. The tester pot is
enabled when a dip switch,
accessed through the hinged
panel faceplate, is switched ON.
The output of this operational
amplifier is fed into an electronic
switch. The switch is fed by three
optically isolated inputs to restrict
torque produced in either forward,
reverse, or both forward and
reverse motor rotation directions.
The output of this switch feeds the
speed loop amplifier. The speed
loop sums these signals along
with the speed feedback signal. A
notch filter is provided in the
feedback loop to eliminate
torsional resonances due to high
inertia loads and motor inertia
mismatches. The notch filter circuit
may be disabled/enabled by using
jumper 1J. Drives are shipped with
the notch filter enabled.
The speed loop contains two
capacitors that may be switched
into the circuit through two dip
switches on the controller
faceplate. All drives are shipped
with capacitors selected. The
output of the speed loop feeds the
regulator. The torque regulator
switch simply bypasses the speed
loop such that the output of the
summing junction for reference
signals feeds directly into the
current regulator. The notch filter
has no effect in the torque
regulator mode.
The microprocessor uses the
motor encoder to determine rotor
position. This information is used
to convert the quadrature
current/torque reference (ITR) to
two motor line current reference.
Two motor line current feedbacks
are then subtracted from the two
motor line current references to
produce two line current errors.
The motor line current errors are
then fed to two independent motor
line current regulators. The
outputs of the motor line current
regulators are then fed into the
base drivers that control the output
transistors. The third line current is
always the sum of the first two.
If Position mode regulation is
selected, the input reference must
be a pulse signal. This pulse
signal feeds directly into the
microprocessor. This control
method allows the microprocessor
to act as an up/down counter. The
reference pulses are up-counts,
and the encoder feedback pulses
subtract from the up-counts so
that the encoder moves only as
many pulses that have been given
as reference.
If a continuous pulse input is
received by the controller, a
constant speed will be maintained
on the motor.
Artisan Technology Group - Quality Instrumentation ... Guaranteed | (888) 88-SOURCE | www.artisantg.com