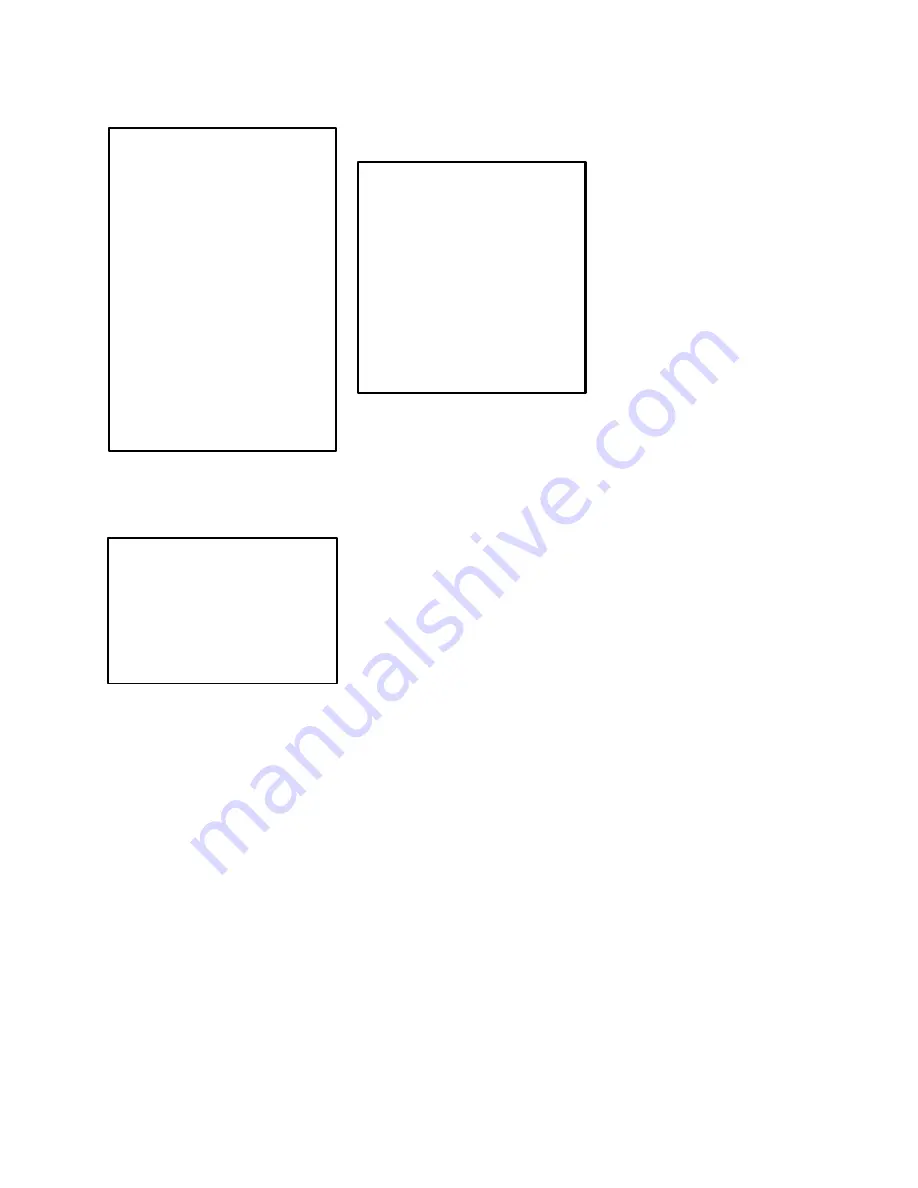
4:1
4: Start and Adjust the Controller
DANGER
ONLY QUALIFIED ELECTRI-
CAL PERSONNEL FAMILIAR
WITH THE CONSTRUCTION
AND OPERATION OF THIS
EQUIPMENT AND THE HAZ-
ARDS INVOLVED SHOULD
INSTALL, ADJUST, OPER-
ATE, AND/OR SERVICE THIS
EQUIPMENT. READ AND UN-
DERSTAND THIS MANUAL IN
ITS ENTIRETY BEFORE
PROCEEDING. FAILURE TO
OBSERVE THESE PRECAU-
TIONS COULD RESULT IN
SEVERE BODILY INJURY OR
LOSS OF LIFE.
Gather Necessary Test
Equipment
CAUTION
Do not use a megger to perform
continuity checks in the drive
equipment. Failure to observe
this precaution could result in
damage to, or destruction of,
the equipment.
The following equipment or its
equivalent is recommended:
•
A two-channel oscilloscope with
10 to 1 probes.
•
A digital volt-ohmmeter with a
10 megohm input impedance on
all ranges, such as a Fluke
8022B.
•
Either an Optional Exercise
Module (M/N 3RE4) or a
function generator with 0.5 V
peak, 1 to 3 Hz square wave
output or manually operated
switch with ungrounded 0.5 V
supply.
Check the Installation
WARNING
THE USER IS RESPONSIBLE
FOR ENSURING THAT DRIV-
EN MACHINERY, ALL DRIVE-
TRAIN MECHANISMS, AND
PROCESS LINE MATERIAL
ARE CAPABLE OF SAFE OP-
ERATION AT AN APPLIED
MOTOR SPEED OF 3000
RPM. FAILURE TO OBSERVE
THIS PRECAUTION COULD
RESULT IN BODILY INJURY.
1.
Make sure the input
disconnect is in the OFF
position (power OFF).
2.
Verify that motor nameplate
data corresponds to the
controller output ratings.
3.
Make sure that any motor
thermal switch or overload
device, if required, is sized for
the rated motor current and is
wired according to Figure
3-12.
4.
Rotate the motor shaft by
hand to check that the motor
is free from any binding or
mechanical load problem and
that no loose items, such as
shaft keys, couplings, etc., are
present.
5.
Visually check the controller
for mechanical damage and
remaining installation debris,
wire strands, etc.
6.
Make sure that all coils, such
as relays and magnetic
valves, that are connected to
the controller or located in the
controller vicinity are
suppressed: A-C coils with RC
filters and D-C coils with
diodes in a non-conducting
direction.
Check the Wiring
1.
Verify that the controller is
wired according to connection
diagram Figure 3-12.
2.
Check that all connections are
tight.
3.
Check that no solder bridges
are present on the connectors.
4.
Check that signal leads are
separated from
electromagnetic fields.
5.
Verify that A-C line voltage is
three phase, 230 VAC (208
VAC if the internal input power
voltage RED wire was
changed as shown in Figure
3-10.
6.
Verify that A-C line frequency
is 50/60 Hz.
7.
Verify that the A-C line feeding
the controller has less than
5,000 amps fault short circuit
rating.
Artisan Technology Group - Quality Instrumentation ... Guaranteed | (888) 88-SOURCE | www.artisantg.com