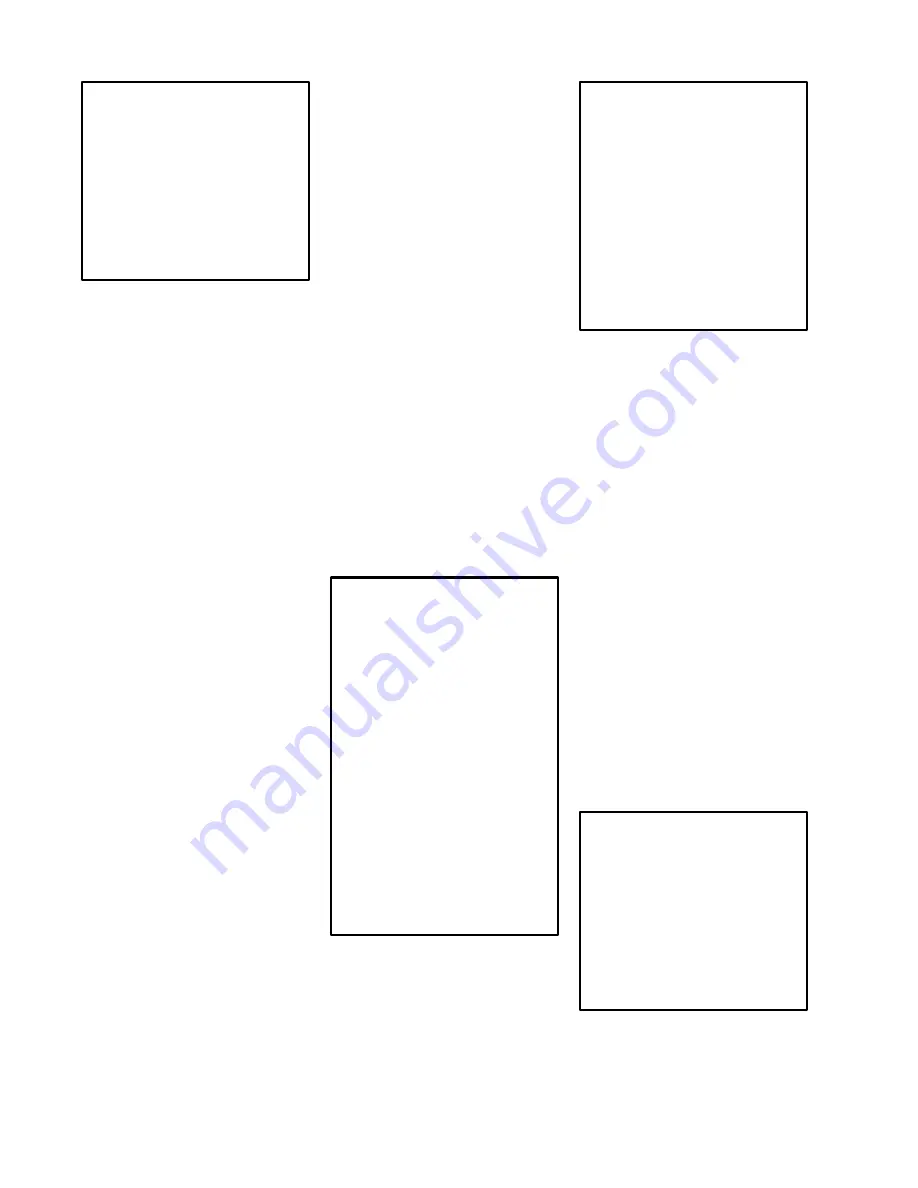
4:14
DANGER
THE REMAINING STEPS
ARE MADE WITH POWER
ON. EXERCISE EXTREME
CARE BECAUSE HAZARD-
OUS VOLTAGE EXISTS.
FAILURE TO OBSERVE THIS
PRECAUTION COULD RE-
SULT IN SEVERE BODILY
INJURY OR LOSS OF LIFE.
5.
Connect the positive lead of a
scope or voltmeter (20 VDC
scale) to the SR test pin and
connect the common lead to
the OV pin.
6.
Turn power ON and set the
Torque reference at maximum
voltage. The controller’s
current limit function is not
functional in torque mode.
Torque reference must be
limited externally. DO NOT
START THE CONTROLLER.
7.
Adjust the SR pot for the
maximum current (torque)
required at the SR test pin. (8
volts = 200% controller-rated
current.)
8.
Connect the positive lead of a
digital voltmeter to the OS test
pin and the common lead to
the OV pin.
9.
Turn the OS pot slowly CW
until the trip point is slightly
greater than the maximum
application motor speed. Use
Figure 4-5C to determine the
equivalent voltage reading of
the overspeed trip point.
10. With Torque reference at
minimum, give the controller a
Start command.
11. Slowly increase the Torque
reference until the motor starts
to rotate.
12. If the motor shaft rotation is
incorrect:
•
Give the controller a Stop
command. Wait until the
motor has completely
stopped.
•
Turn power OFF.
•
After verifying D-C bus
voltage is zero and the
POWER LED is not
illuminated, change the
position of switch 2SW-6 on
the hinged panel.
•
Turn power ON.
•
Give the controller a Start
command.
13. Give the controller a Stop
command.
14. Turn power OFF.
15. After verifying the D-C bus
voltage is zero and the
POWER LED is not
illuminated, remove the
voltmeters and any other
instrumentation connected
during startup.
16. Close and secure the
controller enclosure door, if
applicable.
Perform Startup in Position
Regulator Mode
WARNING
THIS DRIVE IS CAPABLE OF
OPERATING AT AND MAIN-
TAINING ZERO SPEED. THE
USER IS RESPONSIBLE FOR
ASSURING SAFE CONDI-
TIONS FOR OPERATING
PERSONNEL BY PROVID-
ING SUITABLE GUARDS
AND AUDIBLE OR VISUAL
ALARMS OR OTHER DE-
VICES TO INDICATE THAT
THE DRIVE IS OPERATING
OR MAY BE OPERATING AT
OR NEAR ZERO SPEED.
FAILURE TO OBSERVE
THESE PRECAUTIONS
COULD RESULT IN BODILY
INJURY.
WARNING
IMPROPER CONNECTION
OR CALIBRATION OF CON-
TROLLER MAY CAUSE THE
DRIVE TO OVERSPEED. AT
THE INITIAL STARTUP, BE
PREPARED TO STOP THE
DRIVE IMMEDIATELY IF UN-
CONTROLLED ACCELERA-
TION SHOULD OCCUR.
FAILURE TO OBSERVE THIS
PRECAUTION COULD RE-
SULT IN BODILY INJURY.
1.
Make sure all power is OFF.
The POWER LED should not
be illuminated.
2.
Perform “Startup in Speed
Regulator Mode” Steps 4
through 26 and tune for high
response application.
3.
Remove Speed reference
circuit and wire any necessary
inputs or outputs to the
controller for proper machine
operation in the Position
Regulator mode.
4.
With power OFF, set 1SW-1
ON and 1SW-2 OFF.
5.
Wire the reference, a serial
pulse, to 2CN connector pins
49 and 50 according to Table
3-2.
6.
If remote forward and reverse
is desired, wire 2CN connector
pins 47 and 48 according to
Table 3-2.
DANGER
THE REMAINING STEPS
ARE MADE WITH POWER
ON. EXERCISE EXTREME
CARE BECAUSE HAZARD-
OUS VOLTAGE EXISTS.
FAILURE TO OBSERVE THIS
PRECAUTION COULD RE-
SULT IN SEVERE BODILY
INJURY OR LOSS OF LIFE.
7.
Turn power ON.
8.
Connect the positive lead of a
digital voltmeter to the OS test
pin and the common lead to
the OV pin.
Artisan Technology Group - Quality Instrumentation ... Guaranteed | (888) 88-SOURCE | www.artisantg.com