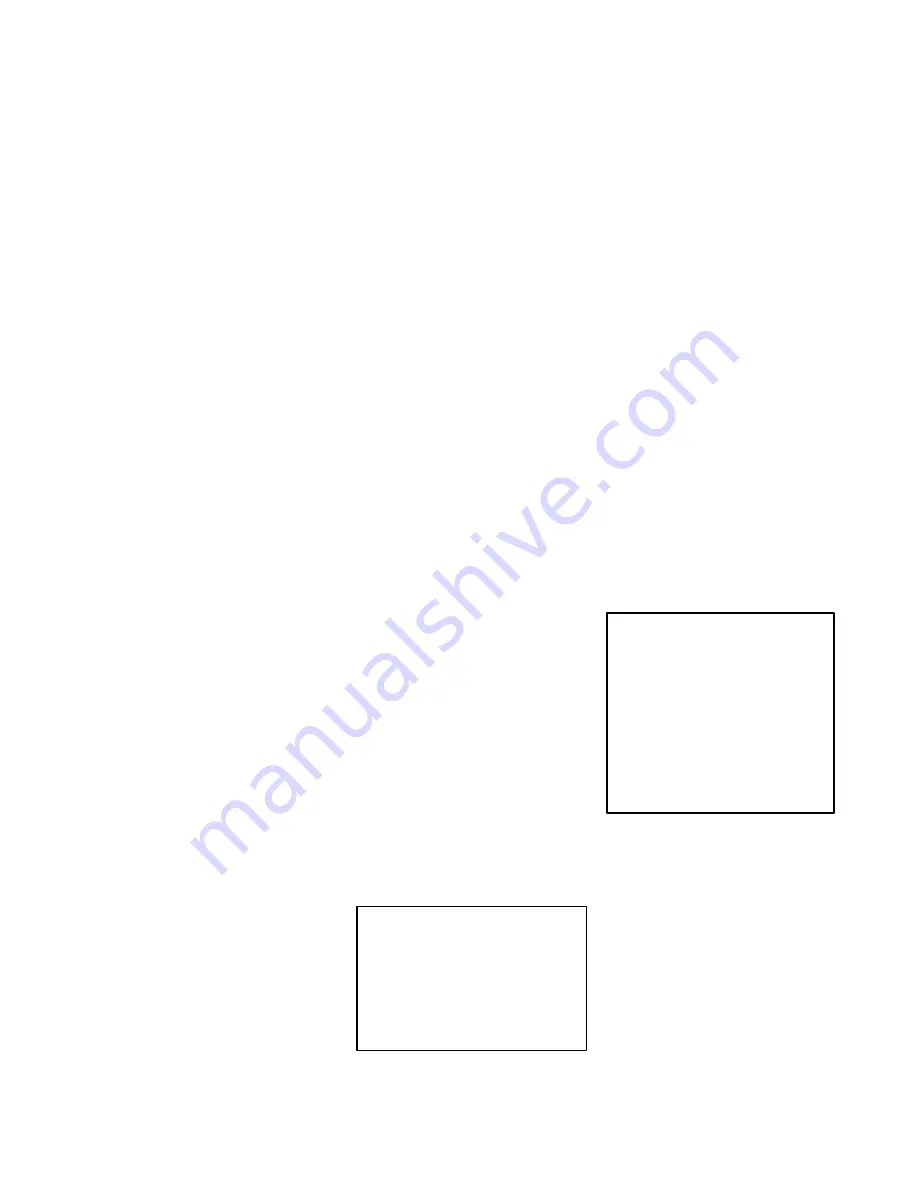
7:3
Understand Controller Status
Indicators
Fault Contact
This contact indicates that a fault
has occurred as described in
Table 7-1. A dry fault contact is
connected at terminals FR1 and
FR2 on the terminal board on the
faceplate of the controller. This
contact is open when no input
power is present or when a fault
condition is present; it is closed
under normal running conditions.
This contact has the following
ratings:
•
D-C: A maximum voltage of 30
VDC or a maximum current of
1 amp resistive.
•
A-C: 250 VA maximum with a
maximum voltage of 250 VAC
or a maximum current of 0.5
amp resistive.
Solid State Outputs
Four optically isolated solid state
outputs are located on connector
2CN. Each output is rated at 24
VDC with 20 mA maximum
sourcing capability. Use twisted
pair wire to monitor these outputs.
•
Ready (RDY): Indicates the
controller has proper power
applied to the input terminals
and no fault conditions exist.
This output is available
between connector 2CN pin
42(+VI) and any unused pin
from 26–32 (0VI).
•
Position Counter Overflow
(POS): Indicates that the pulse
buffer, used to accept
reference when in the position
mode, has overflowed. This
output is available between
connector 2CN pin 43(+VI) and
any unused connector 2CN pin
from 26–32 (0VI).
•
Zero Steady State Error (SZ):
This output is available
between connector 2CN pin
44(+VI) and any unused pin
from 26–32 (0VI). The
indication of this output
depends on the mode selected:
SPEED/TORQUE: Indicates
that the drive is operating at a
speed less than the value
determined by the PG pot.
POSITION: Indicates that the
input frequency reference is
different than the encoder
feedback frequency.
•
Rotation Direction (DIR):
Indicates the motor rotation
direction. When ON, rotation is
counterclockwise when viewed
from the shaft end. This output
is available between connector
2CN pin 45 (+V) and any
unused connector 2CN pin
from 26–32 (0VI).
Understand Controller
Test Points
1.
The controller has 6 test
points and a common on the
regulator that are accessible
through the hinged panel
faceplate.
2.
A scope or digital voltmeter
connected to a test point will
monitor the signal that can be
adjusted by the respective
controller pot.
3.
Fine tune the signal by slowly
turning the pot until the
waveform is as desired.
4.
Refer to “Review the
Regulator Pots” in Chapter 4
for a summary of these pots
along with the waveform
typical for the factory setting of
the pot.
Gather Necessary Test
Equipment
CAUTION
Do not use a megger to perform
continuity checks in the drive
equipment. Failure to observe
this precaution could result in
damage to, or destruction of,
the equipment.
The following equipment or its
equivalent is recommended:
•
A two-channel oscilloscope
with 10 to 1 probes.
•
A digital volt-ohmmeter with a
10 megohm input impedance
on all ranges, such as a Fluke
8022B.
•
Either an optional Exercise
Module (M/N 3RE4) or a
function generator with 0.5 V
peak, 1 to 3 Hz square wave
output or manually operated
switch with ingrounded 0.5 V
supply.
Perform General
Troubleshooting
Procedures
1.
Before removing power to the
controller, check to see if any
RED LED illuminated.
Indicating that an IET has
occurred. (Removing power to
the controller will lose the
status of the LED.) If any LED
is illuminated, refer to Table
7-1 for possible causes of the
IET.
DANGER
THE REMAINING STEPS
ARE MADE WITH POWER
ON. EXERCISE EXTREME
CARE BECAUSE HAZARD-
OUS VOLTAGE EXISTS.
FAILURE TO OBSERVE THIS
PRECAUTION COULD RE-
SULT IN SEVERE BODILY
INJURY OR LOSS OF LIFE.
•
Clear the fault.
•
Reset the controller by
pressing the Reset button
located above the 2SW
switches on the face of the
controller hinged panel.
•
Give the controller a Start
command.
•
If the controller does not
restart, proceed with this
procedure.
Artisan Technology Group - Quality Instrumentation ... Guaranteed | (888) 88-SOURCE | www.artisantg.com