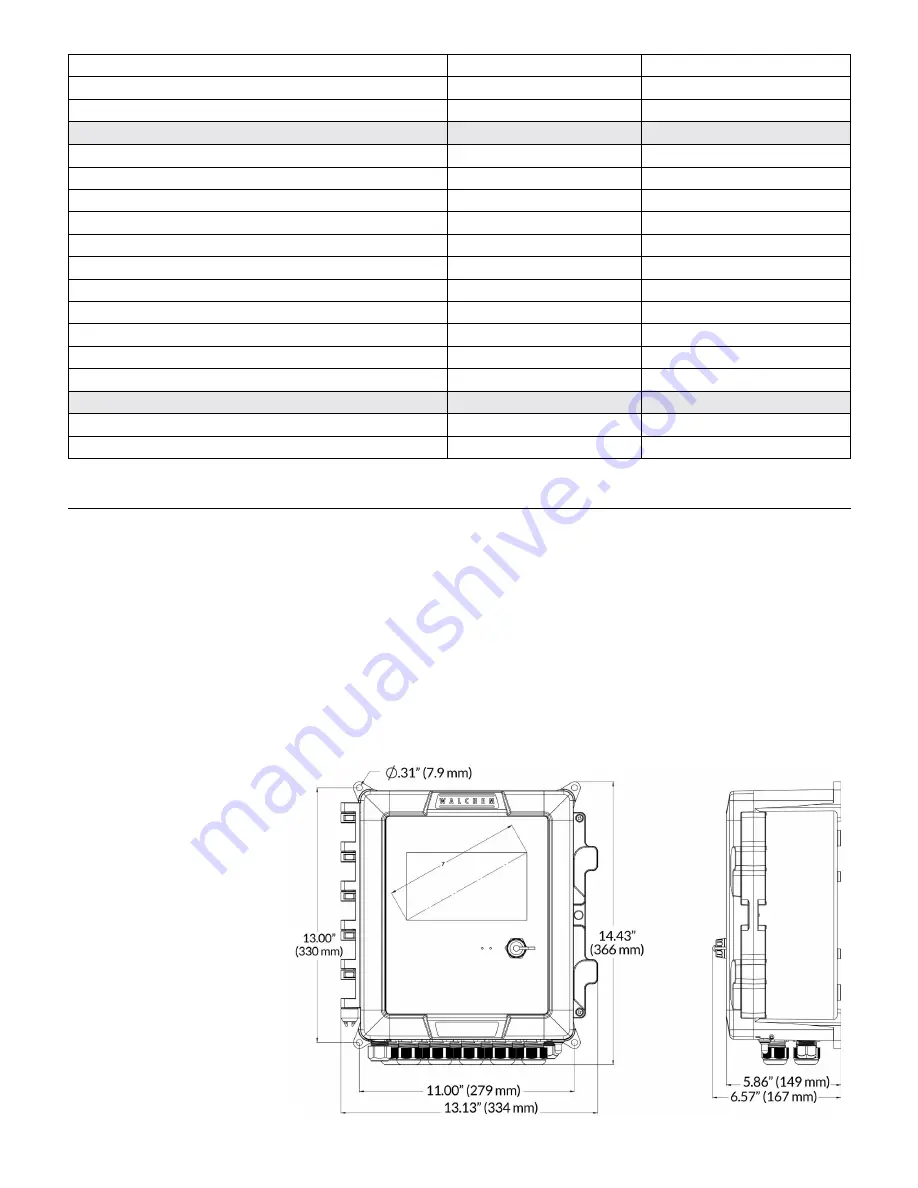
11
Specific Gravity (Flow Prop mode)
0 g/ml
9.999 g/ml
Target (Flow Prop mode)
0 ppm
1,000,000 pm
Low Cycles Limit (Flow Proportional mode)
0 cycles of concentration
100 cycles of concentration
Configuration settings
Low Limit
High Limit
Local Password
0000
9999
Log in Timeout
10 minutes
1440 minutes
Fluent update period
1 minute
1440 minutes
Fluent reply timeout
10 seconds
60 seconds
Alarm Delay
0:00 minutes
59:59 minutes
SMTP Port
0
65535
TCP Timeout
1 second
240 seconds
Auto Dim Time
0 seconds
23:59:59 HH:MM:SS
Device ID (BACnet)
1
4194302
Data Port (Modbus, BACnet)
1
65535
Ad-Hoc Time Limit
1 min.
1440 min.
Graph settings
Low Limit
High Limit
Low axis limit
Low end of sensor range
High end of sensor range
High axis limit
Low end of sensor range
High end of sensor range
3.0 UNPACKING & INSTALLATION
3.1 Unpacking the unit
Inspect the contents of the carton. Please notify the carrier immediately if there are any signs of damage to the controller or
its parts. Contact your distributor if any of the parts are missing. The carton should contain an
EP2100
series controller
and an instruction manual. Any options or accessories will be incorporated as ordered.
3.2 Mounting the electronic enclosure
The controller is supplied with mounting holes on the enclosure. It should be wall mounted with the display at eye
level, on a vibration-free surface, utilizing all four mounting holes for maximum stability. Do not install the enclosure
in a location where it will be exposed to direct sunlight. Use M6 (1/4” diameter) fasteners that are appropriate for
the substrate material of the wall. The enclosure is NEMA 4X (IP66) rated. The maximum operating ambient tem-
perature is 122°F (50°C); this should be considered if installation is in a high temperature location. The enclosure
requires the following clearances:
Top:
2” (50 mm)
Left:
10” (254 mm)
Right:
4” (102 mm)
Bottom:
7” (178 mm)
EP2100