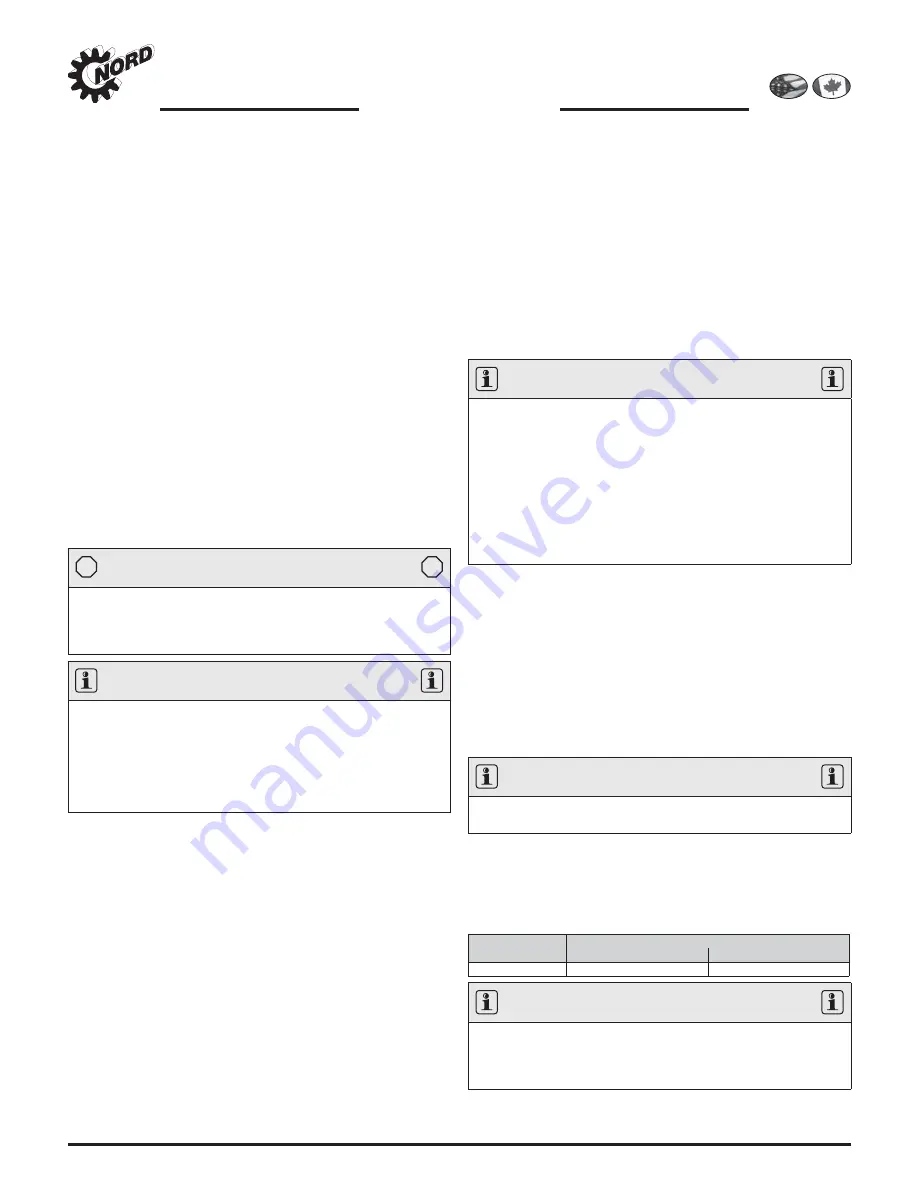
DRIVESYSTEMS
HELICAL-WORM REDUCER LUBRICATION
RETAIN FOR FUTURE USE
U10770 - 1 of 2
1. Importance of proper lubrication
Proper gearbox lubrication is essential in order to reduce
friction, heat, and component wear. Lubricants reduce heat
and wear by inserting a protective “fl uid boundary” between
mating parts and preventing direct metal to metal contact.
Lubricants also help prevent corrosion and oxidation,
minimize foam, improve heat transfer, optimize reducer ef-
fi ciency, absorb shock loads and reduce noise.
NORD helical-worm reducers are shipped from the factory
with a pre-determined oil fi Il level in accordance to the
specifi ed reducer size and mounting position.
2. Standard oil type
NORD helical worm gear reducers are fi lled with ISO VG 680
synthetic-hydrocarbon/polyalphaolefi n (SHC/PAO) worm gear
oil.
• SHC/PAO worm gear oils have good high and low
temperature stability, are compatible with most paint
and seal types, and are miscible with mineral oils.
• SHC/PAO worm gear oils also contain a small amount of
organic ester and other antiwear (AW) packages to
offer improved lubrication conditions, especially in the
worm mesh, where a sideways sliding motion prevails.
Please see user manual U11020 for more specifi c information
and for optional helical worm lubricants.
STOP
HARMFUL SITUATION
STOP
In worm gears avoid using extreme pressure (EP) gear oils
containing sulfur-phosphorous chemistries; these additives
can react adversely with bronze worm gears, and acceler-
ate wear.
IMPORTANT NOTE
Consult the sticker adjacent to the fi ll plug to determine
the type of lubricant installed at the factory. Some units
have special lubricants designed to operate in certain en-
vironments or intended to extend the service life or ser-
vice temperature range of the lubricant. If in doubt about
which lubricant is needed for a certain application, please
contact NORD Gear.
3. Lubrication replacement
The helical-worm gear oil should be replaced at least after
every 20,000 operating hours or after every four years. Often
gear reducers are exposed to extreme ambient conditions,
hostile environments, wet conditions, or dirty and dusty op-
erating areas. Especially in these situations, it is important to
establish a condition-based oil service interval.
4. Effi ciency
Helical worm gears reach effi ciencies up to 92% and are gen-
erally much more effi cient than worm-only gear units. How-
ever, it is important to consider the following, when using
worm gears.
• Worm gears reach their peak rated effi ciency, after they
undergo a natural run-in process (up to 25 hours operating
time at maximum rated load). Catalog published power
and torque fi gures are based upon the rated effi ciency
after the run-in is complete.
• Worm gears have naturally lower startup effi ciencies com-
pared to operating effi ciencies. As input speed increases
the enhanced hydrodynamic effects of the oil result in less
tooth friction and increased worm gear effi ciency.
IMPORTANT NOTE
Worm gear reducers applied in cold temperature service
,
may require increased motor power for the following
reasons:
• Lower operating temperatures, cause lubrication viscosity
to increase in both the gearbox and in the moving areas
of the driven machine.
•
Worm-gears have naturally lower start-up effi ciencies
compared to operating effi ciencies.
• In extreme cases, one might need to consider increasing
the motor power and lowering the oil viscosity
5. Oil Viscosity
Viscosity, or the oil’s resistance to shear under load, is often
considered the single most important property of any gear oil.
• Often one will consider making a viscosity correction to
the oil to improve the performance when operating the
gear unit at low temperature or high temperature.
• In cases of extreme load conditions, gear pairs and antifric-
tion bearings may be more susceptible to sliding or scuffi ng
wear. In these operating conditions, it may also be ben-
efi cial to consider an increased lubrication viscosity and/or
a lubrication with improved antiwear additive packages.
IMPORTANT NOTE
The user should consult with their primary lubrication sup-
plier before considering changes in oil type or viscosity.
6. Maximum oil sump temperature limit
To prevent reducer overheating, the reducer’s maximum oil
sump temperature limit must not be exceeded for prolonged
periods of operation (up to 3 hours continuous operation de-
pending upon reducer size).
Oil Type
Maximum Oil Temperature Limit
NORD
AGMA 9005-D94
Synthetic
105°C (220°F)
107°C (225°F)
IMPORTANT NOTE
Use caution when specifying gear reducers for high
temperature service.
If there is concern about exceeding
the allowable safe operating temperatures, please consult
NORD to discuss alternatives.
www.nord.com/docs
06.01.11
NORD Gear Corporation
Toll Free in the United States: 888.314.6673
NORD Gear Limited
Toll Free in Canada: 800.668.4378
Содержание Pulsalube 8 GS Ultra
Страница 8: ......
Страница 18: ......
Страница 20: ......
Страница 36: ......
Страница 38: ......
Страница 42: ......
Страница 48: ......
Страница 50: ......
Страница 53: ......
Страница 54: ......
Страница 55: ......
Страница 56: ......
Страница 61: ......
Страница 62: ......
Страница 64: ......
Страница 86: ......
Страница 87: ......
Страница 88: ......
Страница 89: ...XVJDEH LVVXH RNXPHQW GRFXPHQW 20 6 XV ODWW VKHHW 6SDUH SDUWV 6SDUH SDUWV OLVW 6HFWLRQDO GUDZLQJ DQG SDUWV OLVW...
Страница 90: ......
Страница 93: ......
Страница 94: ......
Страница 96: ......
Страница 98: ......
Страница 100: ......
Страница 110: ......
Страница 113: ......
Страница 114: ......
Страница 116: ......
Страница 118: ......
Страница 122: ......
Страница 126: ......