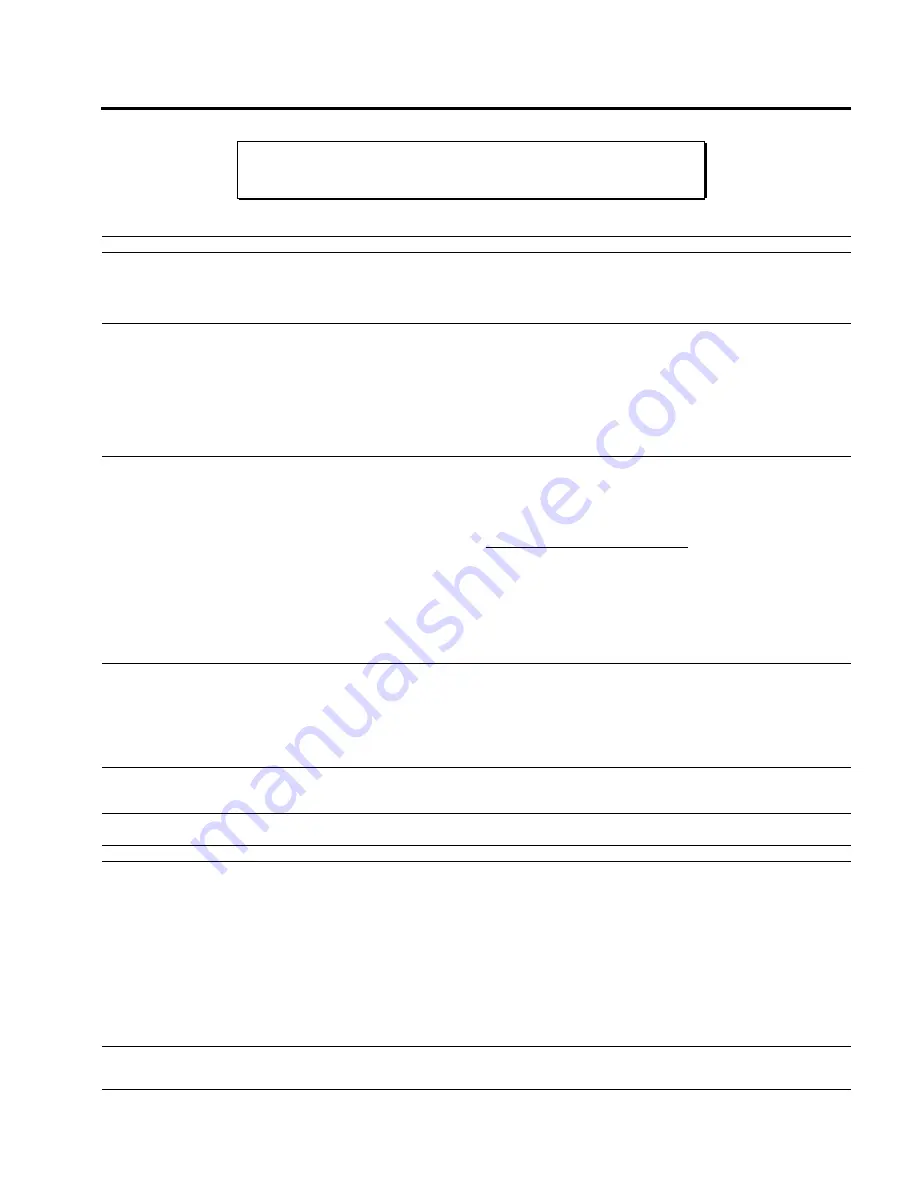
Chapter 2. Troubleshooting
2 5
Common Problems & Solutions
N O T E
Some software-related causes are provided because it is sometimes
difficult to identify a problem as either hardware or software related.
Problem
Cause
Solution
Communication
(serial) not operative,
or receive garbled
characters.
1. Improper interface connections or
communication protocol.
2. Serial communication is disabled.
3. In a daisy chain, the unit may not be
set to proper address.
1. See
Troubleshooting Serial Communication section below.
2. Enable serial communication with the
E1
command.
3. Verify DIP switch settings (see page 4), or proper use of
ADDR
command.
Direction is reversed.
1. Direction connections to the drive are
reversed.
2. Phase of encoder reversed (reported
TPE
direction is reversed).
1.a. Software remedy: You can use the
CMDDIR1
command to reverse the
polarity of both the commanded direction and the polarity of the encoder
counts).
1.b. Hardware remedy: Switch DIR- with the DIR+ connection to the drive (if
your drive does not accept differential outputs this will not work). You will also
have to change the feedback device wiring or mounting so that it counts in
same direction as the commanded direction.
2.a. Software remedy: For the affected axis, issue the encoder feedback
polarity reversal command (
ENCPOL1
).
2.b. Hardware remedy: Swap the A+ and A- connections to the 6200.
Distance, velocity, and
accel are incorrect as
programmed.
1. Incorrect resolution setting.
2. Pulse width too narrow.
1.a. Use the
DRES
command to configure the 6200 to match the resolution of
the drive (usually set with DIP switches). The 6200’s default drive resolution
for both axes is set to 25,000 steps/rev (
DRES25ØØØ,25ØØØ
).
1.b. If using encoder feedback, match the
ERES
command setting (default
ERES
setting is 4,000 counts/rev for both axes:
ERES4ØØØ,4ØØØ
) to the
post-quadrature resolution of the encoder.
ERES
values for Compumotor encoders:
E Series Encoders:
ERES4000
OS motor with -HJ encoder (OSxxx-xxx-HJ):
ERES2048
OS motor with -RE encoder (OSxxx-xxx-RE):
ERES4000
OS motor with -RC encoder (OSxxx-xxx-RC):
ERES4000
RS motor with -EC encoder (RSxxx-xxx-EC):
ERES4000
OEM Series Encoders: 83 size:
ERES4000
57 size:
ERES2048
2. Set the pulse width to the drive specifications using the
PULSE
command
(default pulse width setting is 0.3
µ
s).
Encoder counts
missing.
1. Improper wiring.
2. Encoder slipping.
3. Encoder too hot.
4. Electrical noise.
5. Encoder frequency too high.
1. Check wiring.
2. Check and tighten encoder coupling.
3. Reduce encoder temperature with heatsink, thermal insulator, etc.
4.a. Shield wiring.
4.b. Use encoder with differential outputs.
5. Peak encoder frequency must be below 1.6MHz post-quadrature. Peak
frequency must account for velocity ripple.
Erratic operation.
1. Electrical noise and/or improper
shielding.
2. Improper wiring.
1.a. Reduce electrical noise or move 6200 away from noise source.
1.b. Refer to
Reducing Electrical Noise on page 24.
2. Check wiring for opens, shorts, & mis-wired connections.
Joystick Mode: motor
does not move.
1. Joystick Release input not grounded.
2. Improper wiring.
1. Ground the Joystick Release input.
2. Check wiring for opens, shorts, and mis-wired connections.
LEDs
See
Diagnostic LED above (page 24)
Motion does not occur.
1. Check “STATUS” LED.
2. End-of-travel limits are active.
3. P-CUT (pulse cut) input not grounded.
4. Drive fault detected.
5. Improper wiring.
6. Load is jammed.
7. No torque from motor.
8. Step pulse width is too narrow for the
drive to recognize.
1. See
Diagnostic LED above.
2.a. Hardware limit switches: Move the load off of the limits or disable the
limits with the
LHØ,Ø
command.
2.b. Software limits: Set
LSPOS
to a value greater than
LSNEG
.
3. Ground the P-CUT connection.
4.a. Check status with
TASXF
command (see bit #4).
4.b. Verify correct drive fault level setting (
DRFLVL
command value).
5. Check command (CMD), shutdown (SHTNC or SHTNO),
drive fault (DFT), and end-of-travel limit connections.
6. Remove power and clear jam.
7. See problem:
Torque, loss of.
8. Set the pulse width to the drive specifications using the
PULSE
command
(default pulse width setting is 0.3
µ
s).
Motor creeps at slow
velocity in encoder
mode.
1. Encoder direction opposite of motor
direction.
2. Encoder connected to wrong axis.
1. Switch encoder connections A+ & A- with B+ & B-.
2. Check encoder wiring.
Artisan Technology Group - Quality Instrumentation ... Guaranteed | (888) 88-SOURCE | www.artisantg.com
Содержание Compumotor 6200
Страница 5: ...Artisan Technology Group Quality Instrumentation Guaranteed 888 88 SOURCE www artisantg com ...
Страница 7: ...Artisan Technology Group Quality Instrumentation Guaranteed 888 88 SOURCE www artisantg com ...
Страница 35: ...Artisan Technology Group Quality Instrumentation Guaranteed 888 88 SOURCE www artisantg com ...
Страница 37: ...Artisan Technology Group Quality Instrumentation Guaranteed 888 88 SOURCE www artisantg com ...
Страница 41: ...Artisan Technology Group Quality Instrumentation Guaranteed 888 88 SOURCE www artisantg com ...