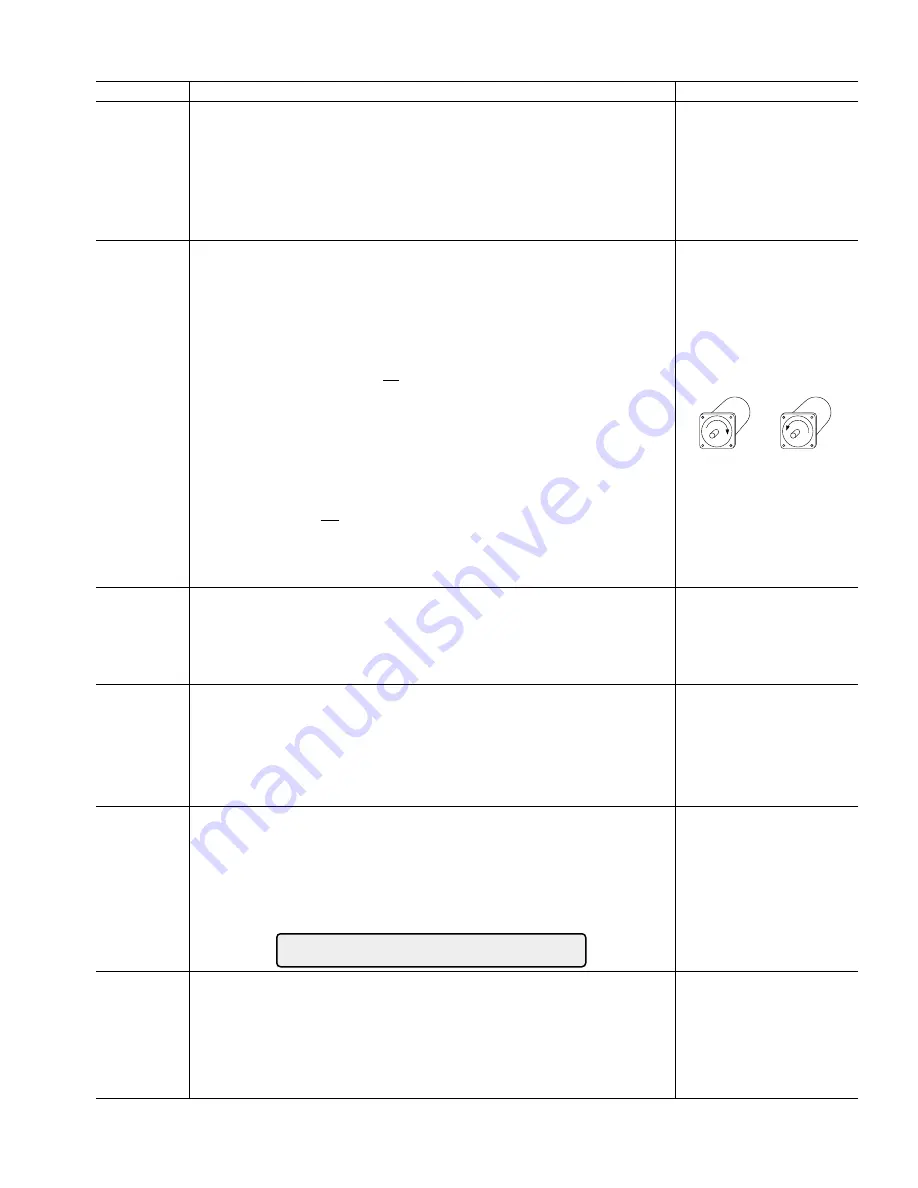
Chapter 1. Installation
2 1
Connections
Test Procedure
Response Format
(left to right)
End-of-travel
and
Home Limits
NOTE: If you are not using end-of-travel limits, issue the Disable Limits (
LHØ,Ø
) command
and ignore the first two bits in each response field.
1. Enable the hardware end-of-travel limits with the
LH3,3
command.
2. Close the end-of-travel switches and open the home switches.
3. Enter the
TLIM
command. The response should be
*TLIM11Ø_11Ø
.
4. Open the end-of-travel switches and close the home switches.
5. Enter the
TLIM
command. The response should be
*TLIMØØ1_ØØ1
.
6. Close the end-of-travel switches and open the home switches (return to original config.).
7. Enter the
TLIM
command. The response should be
*TLIM11Ø_11Ø
.
TLIM
response:
bit 1 = Axis 1 CW limit
bit 2 = Axis 1 CCW limit
bit 3 = Axis 1 HOM limit
bit 4 = Axis 2 CW limit
bit 5 = Axis 2 CCW limit
bit 6 = Axis 2 HOM limit
“CW” means positive travel.
“CCW” means negative travel.
“HOM” means home.
Motor and
Encoder
(motion)
1. Enter the
ENCØØ
command to enable the motor step mode for both axes.
Enter the
PSETØ,Ø
command to set the motor position to zero on both axes.
Enter the
TPM
command to report the motor positions.
The response should be
*TPM+Ø,+Ø
(motors are both at position zero).
Enter the
D25ØØØ,25ØØØ
command, followed by the
GO
command. The motors will
move one rev (25000 steps) in the clockwise direction (viewed from the flange end).
Enter the
TPM
command to report the motor positions.
The response should be
*TPM+25ØØØ,+25ØØØ
(motors are both at position 25000).
2. NOTE: Ignore this step if you are not using encoder feedback. This test assumes you are
using a 1000-line encoder yielding a 4000 count/rev resolution.
Enter the
ENC11
command to enable the encoder step mode on both axes.
Enter the
PSETØ,Ø
command to set the encoder position to zero on both axes.
Enter the
TPE
command to report the encoder positions. The response should be
*TPE+Ø,+Ø
(encoders are both at position zero).
If the encoders are coupled to the motor shafts: Enter the
D4ØØØ,4ØØØ
command,
followed by the
GO
command. The encoders (and motors) will move one revolution (4000
counts) in the clockwise direction (viewed from the flange end).
If the encoders are not coupled to the motor shafts: Manually rotate the encoder
shafts one revolution in the clockwise direction (viewed from the flange end).
Enter the
TPE
command to report the encoder positions.
The response should be
*TPE+4ØØØ,+4ØØØ
(encoders are at position 4000).
Enter the
ENCØØ
command to return the 6200 to the default motor step mode.
TPM
response (motor counts):
±
motor1,
±
motor2
TPE
response (encoder counts):
±
encoder1,
±
encoder1
Direction of rotation:
Counter-clockwise
(negative counts)
Clockwise
(positive counts)
Programmable
Inputs
(incl. triggers)
1. Open the input switches or turn off the device driving the inputs.
2. Enter the
TIN
command.
The response should be
*TINØØØØ_ØØØØ_ØØØØ_ØØØØ_ØØØØ_ØØØØ_ØØ
.
3. Close the input switches or turn on the device driving the inputs.
4. Enter the
TIN
command.
The response should be
*TIN1111_1111_1111_1111_1111_1111_11
.
TIN
response:
bits 1-24 = prog. inputs 1-24
bits 25-26 = TRG-A and TRG-B
Programmable
Outputs
(incl. OUT-A
and OUT-B)
1. Enter the
OUTALL1,26,1
command to turn on (sink current on) all programmable
outputs. Verify that the device(s) connected to the outputs activated properly.
2. Enter the
TOUT
command.
The response should be
*TOUT1111_1111_1111_1111_1111_1111_11
.
3. Enter the
OUTALL1,26,Ø
command to turn off all programmable outputs. Verify that the
device(s) connected to the outputs de-activated properly.
4. Enter the
TOUT
command.
The response should be
*TOUTØØØØ_ØØØØ_ØØØØ_ØØØØ_ØØØØ_ØØØØ_ØØ
.
TOUT
response:
bits 1-24 = prog. outputs 1-24
bits 25-26 = OUT-A and OUT-B
RP240
1. Cycle power to the 6200.
2. If the RP240 is connected properly, the RP240’s status LED should be green and one of the
lines on the computer or terminal display should read
*RP24Ø CONNECTED
.
If the RP240’s status LED is off, check to make sure the +5V connection is secure.
If the RP240’s status LED is green, but the message on the terminal reads
*NO REMOTE
PANEL
, the RP240 Rx and Tx lines are probably switched. Remove power and correct.
3. Assuming you have not written a program to manipulate the RP240 display, the RP240
screen should display the following:
COMPUMOTOR 6200 INDEXER
RUN JOG STATUS DISPLAY ETC
Pulse Cutoff
and Joystick
Inputs
1. Open the pulse cutoff input (P-CUT) switch, and open the joystick input switches or turn off
the device driving the joystick inputs.
2. Enter the
TINO
command.
The response should be
*TINOØØØØ_ØØØØ
.
3. Close the P-CUT switch, and close the joystick input switches or turn on the device
driving the inputs.
4. Enter the
TINO
command.
The response should be
*TINO1111_11ØØ
.
TINO
response:
bit 1 = joystick auxiliary
bit 2 = joystick trigger
bit 3 = joystick axes select
bit 4 = joystick velocity select
bit 5 = joystick release
bit 6 = Pulse cutoff (P-CUT) input
bits 7 & 8 are not used
Artisan Technology Group - Quality Instrumentation ... Guaranteed | (888) 88-SOURCE | www.artisantg.com
Содержание Compumotor 6200
Страница 5: ...Artisan Technology Group Quality Instrumentation Guaranteed 888 88 SOURCE www artisantg com ...
Страница 7: ...Artisan Technology Group Quality Instrumentation Guaranteed 888 88 SOURCE www artisantg com ...
Страница 35: ...Artisan Technology Group Quality Instrumentation Guaranteed 888 88 SOURCE www artisantg com ...
Страница 37: ...Artisan Technology Group Quality Instrumentation Guaranteed 888 88 SOURCE www artisantg com ...
Страница 41: ...Artisan Technology Group Quality Instrumentation Guaranteed 888 88 SOURCE www artisantg com ...