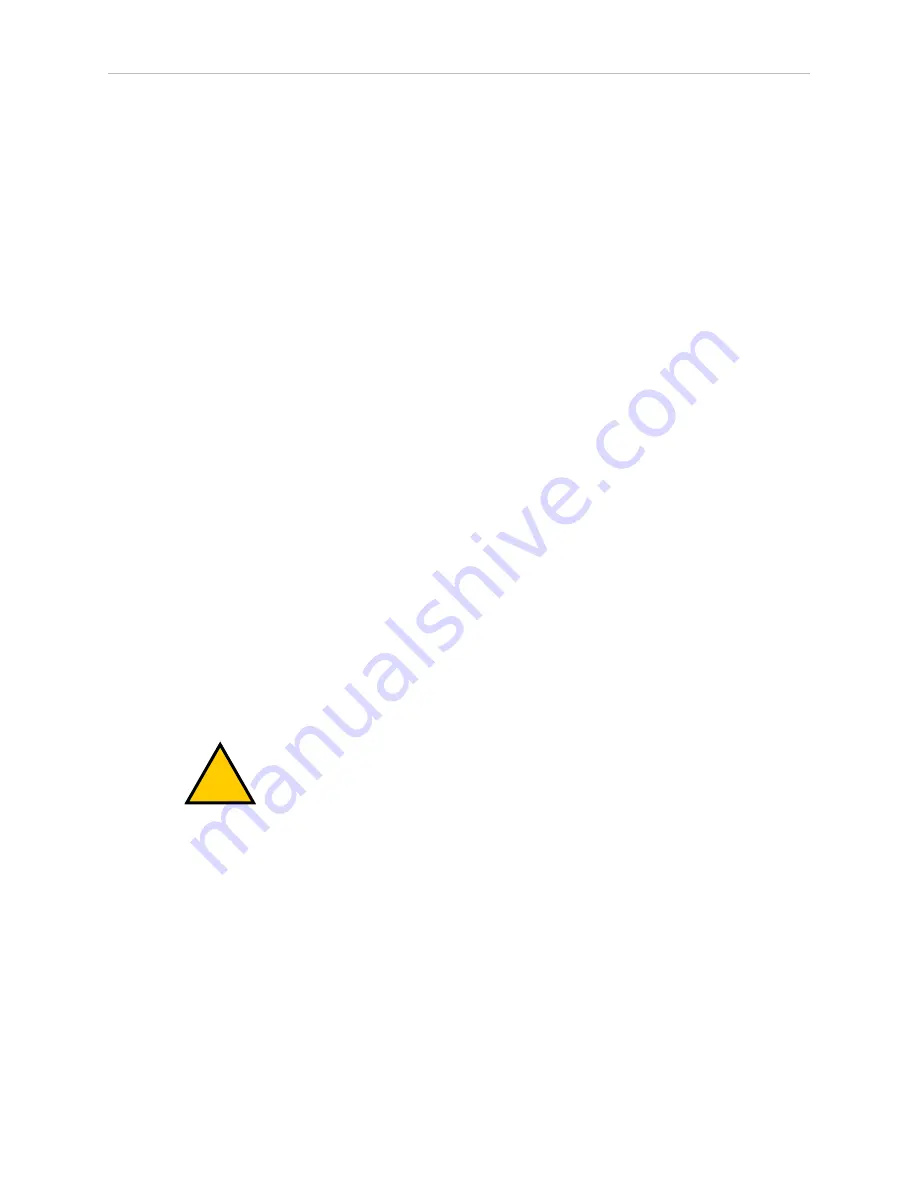
Chapter 2: Safety
l
Enable power through ACE software installed on your PC
l
l
Press the ROBOT POWER button on the Pendant
Once the motors are enabled, the robot will wait two seconds and then resume commanded
motion, if there is adequate space to maneuver.
2.4 Robot Behavior
Hardstops
If the Cobra 350 runs into one of its hardstops, the robot’s motion will stop completely, an
envelope error will be generated, and power will be cut to the robot motors.
The robot cannot continue to move after hitting a hardstop until the error has been cleared.
The Cobra 350’s hardstops are capable of stopping the robot at any speed, load, and max-
imum or minimum extension.
Limiting Devices
There are no dynamic or electro-mechanical limiting devices provided by Omron Adept Tech-
nologies, Inc. The robot does not have safety-rated soft axis or space limiting.
However, the user can install their own safety rated (category 0 or 1) dynamic limiting devices
if needed, that comply with ISO 10218-1, Clause 5.12.2.
Singularities
No singularities exist that cause a hazardous situation with a Cobra 350 robot.
2.5 Intended and Non-intended Use
Intended Use of the Robot
!
WARNING:
PERSONAL INJURY RISK
Cobra 350 robots are not collaborative robots. They require a dedicated work
area that will prevent personnel from coming into contact with them during
operation.
The normal and intended use of Cobra 350 robot does not create hazards.
The Cobra 350 robots have been designed and constructed in accordance with the relevant
requirements of IEC 60204-1.
The Cobra 350 robot is intended for use in parts assembly and material handling for payloads
up to 5.0 kg. See Technical Specifications on page 119 for complete specifications. Refer to the
Robot Safety Guide
for details on the intended use of our robots.
Guidelines for safe use:
l
Clean, dry mounting surfaces — surfaces that are routinely kept free of debris and
liquids.
05624-000 Rev. K
Cobra 350 User's Guide
17