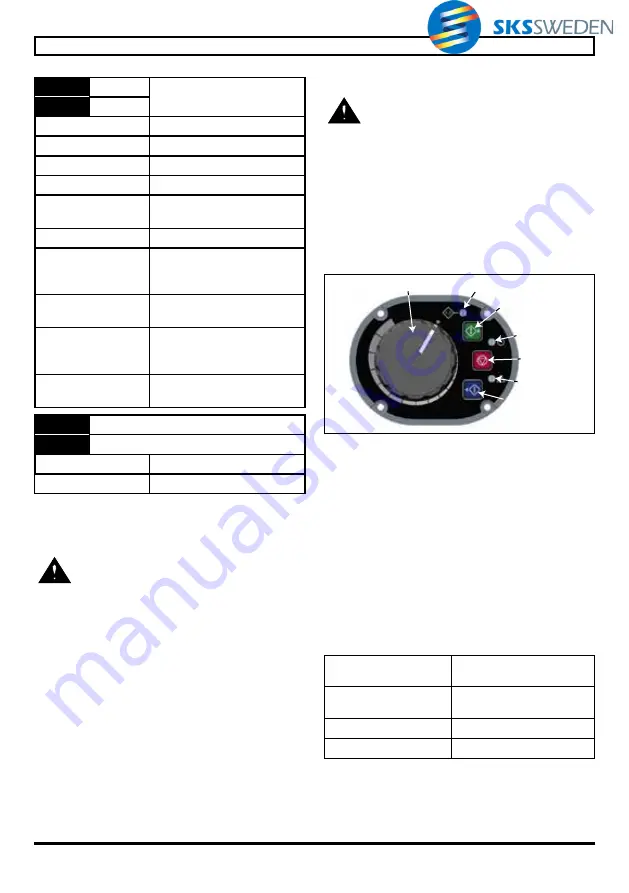
26
Installation and quick start commissioning guide - Commander ID300/302
5511 en - 2017.06 / a
QUICK START COMMISSIONING
31
STO1
Safe Torque Off function
(drive enable)
34
STO2
Terminal 31 function
STO1 channel
Terminal 34 function
STO2 channel
Type
Positive logic only digital input
Voltage range
0 to +24 V
Absolute maximum
applied voltage
30 V
Logic Threshold
10 V ±5 V
Low state maximum
voltage for disable to
SIL3 and PL e
5 V
Impedance
>4 mA @ 15 V, <15 mA @30 V
(IEC 61131-2, type 1)
Low state maximum
current for disable to
SIL3 and PL e
0.5 mA
Response time
Nominal: 12 ms
Maximum: 20 ms
32
0 V STO1
33
0 V STO2
Terminal 32 function
Common connection for STO1
Terminal 33 function
Common connection for STO2
3.6.4 - EIA 485 serial communication port
The serial communication port is single insulated and
meets the requirements for ELV.
When using the communications port with
a personal computer or centralized
controller e.g. PLC, an isolation device
must be included with a rated voltage at least equal
to the drive supply voltage. Ensure that the correct
fuses are installed at the drive input, and that the
drive is connected to the correct supply voltage.
If a serial communications converter other than
the CT Comms cable is used to connect to other
circuits classified as Safety Extra Low Voltage
(SELV) (e.g. to a personal computer), then a safety
isola ting barrier must be included to maintain the
SELV classification.
An isolated serial communications lead has been
designed to connect the drive to IT equipment (such as
laptop computers), and is available from the supplier of
the drive (part number: 4500.0096).
The “isolated serial communications” lead has
reinforced insulation as defined in IEC60950 for
altitudes up to 3,000 m.
4 - QUICK START COMMISSIONING
•
Ensure that no damage or safety hazard
could arise from the motor starting
unexpectedly.
By default, the correct motor rated current is set
in Pr 00.006. Please do not alter it, otherwise it will
affect the thermal protection of the motor.
•
If the drive is started using a keypad it will run to
the speed defined by a keypad reference. This may
not be acceptable depending on the application.
The user must check in Pr 01.017 and ensure that
the keypad reference has been set to 0.
•
If the intended maximum speed affects the safety
of the machinery, additional independent over-
speed protection must be used.
Potentiometer Yellow LED
Green LED
Red LED
Run Forward
Run Reverse
Stop
4.1 - Standard configuration with
potentiometer and Run/stop commands
flange option (ID-RUN-POT-LED-
FLANGE)
By using this standard configuration with potentio meter
and Run/stop command option, the user has to only
connect the enable or STO terminals (see section 3.6)
before proceeding to the quick start-up hereafter.
The default settings of the Commander ID300/302
standard configuration (Pr
00.005
= STANDARD AV/
AI) are as follows. Ensure default settings suit your
application. If not, add a Field keypad RTC option to set
para meters accordingly.
Minimum Reference
Clamp
10.00 Hz
Maximum Reference
Clamp
50.00 Hz
(or 80 Hz for gear-motor)
Acceleration Rate
5.0 s/100 Hz
Deceleration Rate
10.0 s/100 Hz