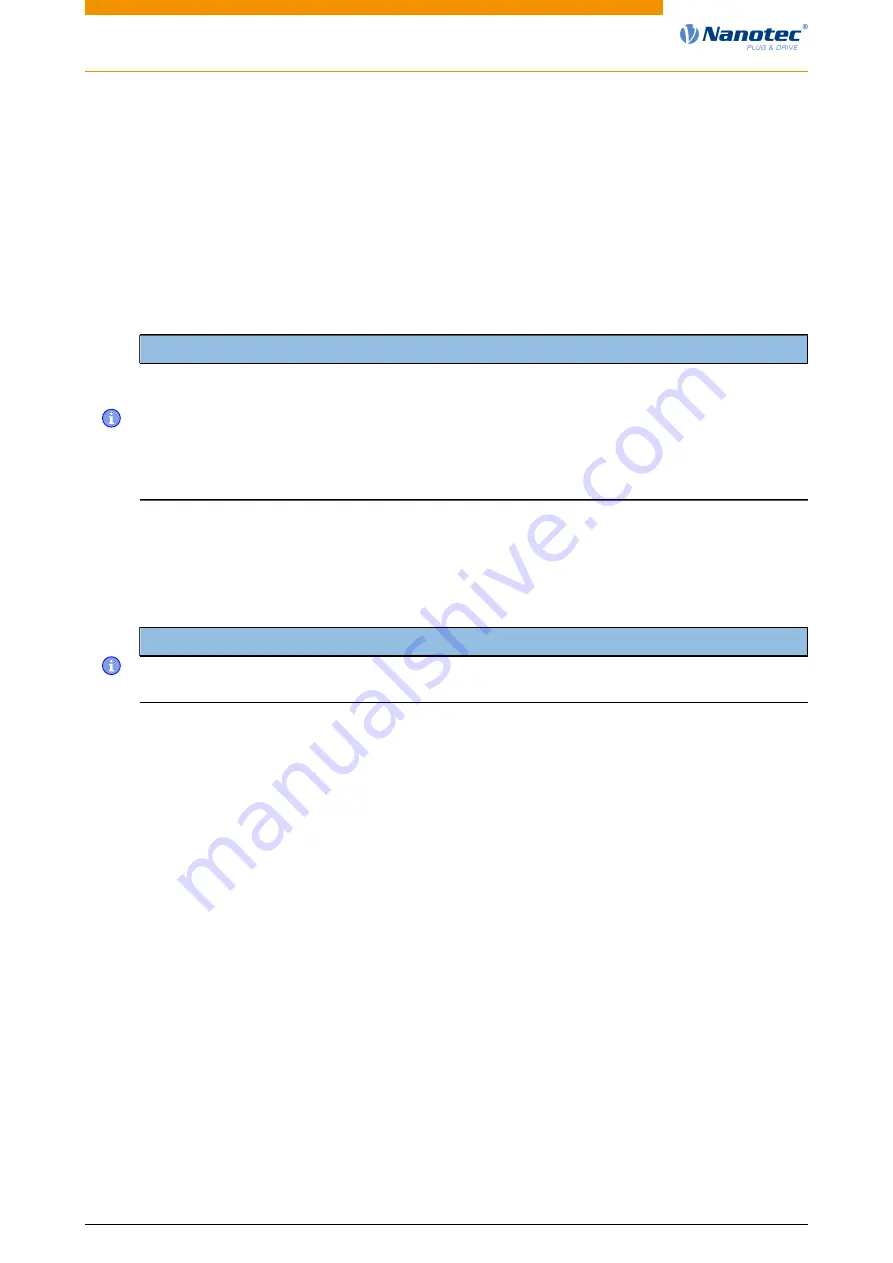
Technical Manual N5 (CANopen)
7 Special functions
1. The motor is brought to a standstill.
2. The time stored in 2038
h
:1
h
is allowed to elapse.
3. The brake is activated.
4. The time stored in 2038
h
:2
h
is allowed to elapse.
5. The motor current is switched off.
7.2.4 Brake PWM
The switched-on brake generates a PWM signal at the output of the controller that can be adjusted
with respect to duty cycle and frequency. If an output pin without PWM is needed, a duty cycle of 100
percent can be set.
Note
The Brake + pin of the brake output is internally connected to the voltage supply of the controller.
If the operating voltage of the brake is greater than the supply voltage of the controller, you cannot
use the brake output of the controller; you must supply the brake externally.
If the supply voltage of the controller is greater than the operating voltage of the brake (and up to 48 V
DC), it is recommended that the PWM controller from Nanotec with order designation EB-BRAKE-48V
be used and the duty cycle of the controller brake output be set to "100".
Frequency
The frequency of the brake PWM can be set in object 2038
:5
h
. The unit is Hertz; a value greater than
2000 is not possible.
Note
If the PWM signal of the brake causes interfering noise, it can be eliminated by connecting a 47
µF
… 100
µF capacitor in parallel at the brake output.
Duty cycle
The duty cycle – the ratio of pulse to period duration – is set in 2038
:6
h
. The value is a percentage
and can be selected between 2 and 100. With a value of 100, the output pin is permanently switched
on.
In the following figure, example duty cycles of 25 and 50 percent are shown, whereby the frequency is
held constant.
Version: 2.0.1 / FIR-v1650
95