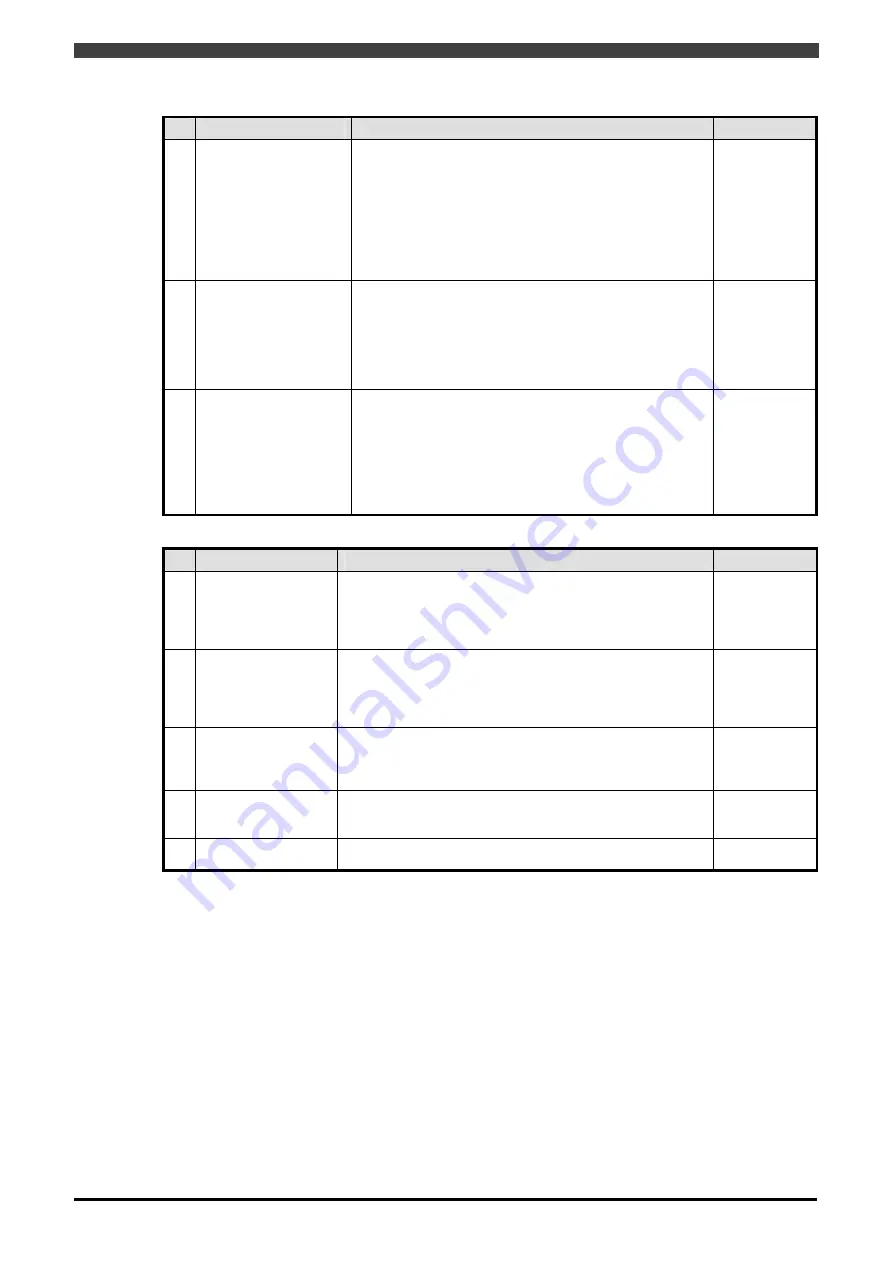
1.1 Outline
1-6
Encoder and motor interface
Item
Specifications
Remarks
1 Basic
functions
<Encoder>
It is possible send/receive data to/from the bidirectional
serial communication encoder.
It is possible to read communication between servo
amplifier and encoder together with request data and
encoder output data.
<Motor>
The motor position can be read out from the power line of
the motor.
2 Connection
method
<Encoder>
For the method of connecting encoder, 1-axis individual
connection or bus connection is available.
For both individual and bus connections, up to 8 axes can
be connected.
The connection method can be specified, using the
parameter of “Encoder type”.
3 Error
detection
<Encoder>
Encoder detection error
Timeout detection (hardware)
Encoder ID check (hardware)
Line disconnection detection (software)
<Motor>
Motor magnetic pole position is compared with the
encoder, and detects the mismatch of their angle.
Input/output signal, Motor power control sequence processing
Item
Specifications
Remarks
1 Safety
inputs
This is to read the safety signal.
For further details, see “2.3.2 Safety inputs.”
Diagnoses system short circuit between inputs, input circuit
failure, disparity between two inputs, and over current.
If an error is detected, safety output is turned OFF.
2 Safety
outputs
This is to output the safety signal.
For further details, see “2.3.3 Safety outputs.”
Diagnoses system short-circuit between outputs, output
circuit failure, and back check input circuit failure.
If an error is detected, safety output is turned OFF.
3 Monitor
inputs
This is to the read non-safety signal.
For further details, see “2.3.5 Non-safety inputs.”
Diagnoses input circuit failure and over current.
If an error is detected, safety output is turned OFF.
4 Monitor
outputs
This is to the output non-safety signal.
For further details, see “2.3.6 Non-safety outputs.”
If an error is detected, safety output is turned OFF.
5
Motor power control
sequence
This is to set the safety output to ON/OFF depending on
input conditions such as emergency stop and enable switch.
Содержание RMU20-20
Страница 2: ......
Страница 6: ...Contents 4 ...
Страница 8: ......
Страница 26: ...1 4 EC DECLARATION OF CONFORMITY FOR MACHINERY 1 18 NOTE ...
Страница 68: ...2 9 Enabling RMU 2 40 NOTE ...
Страница 70: ......
Страница 86: ...3 2Operation procedure 3 16 Top Display Form Limit Side Display Sphere Limit Side Display Form Limit ...
Страница 100: ...3 4 Setting when a slider unit is used 3 30 NOTE ...
Страница 102: ......
Страница 138: ...4 4Approval 4 36 8 Approval is completed The following screen will be displayed ...
Страница 144: ......
Страница 154: ...5 4Trouble shooting 5 10 NOTE ...
Страница 156: ......
Страница 166: ...6 4Trouble shooting 6 10 NOTE ...
Страница 168: ......
Страница 189: ......