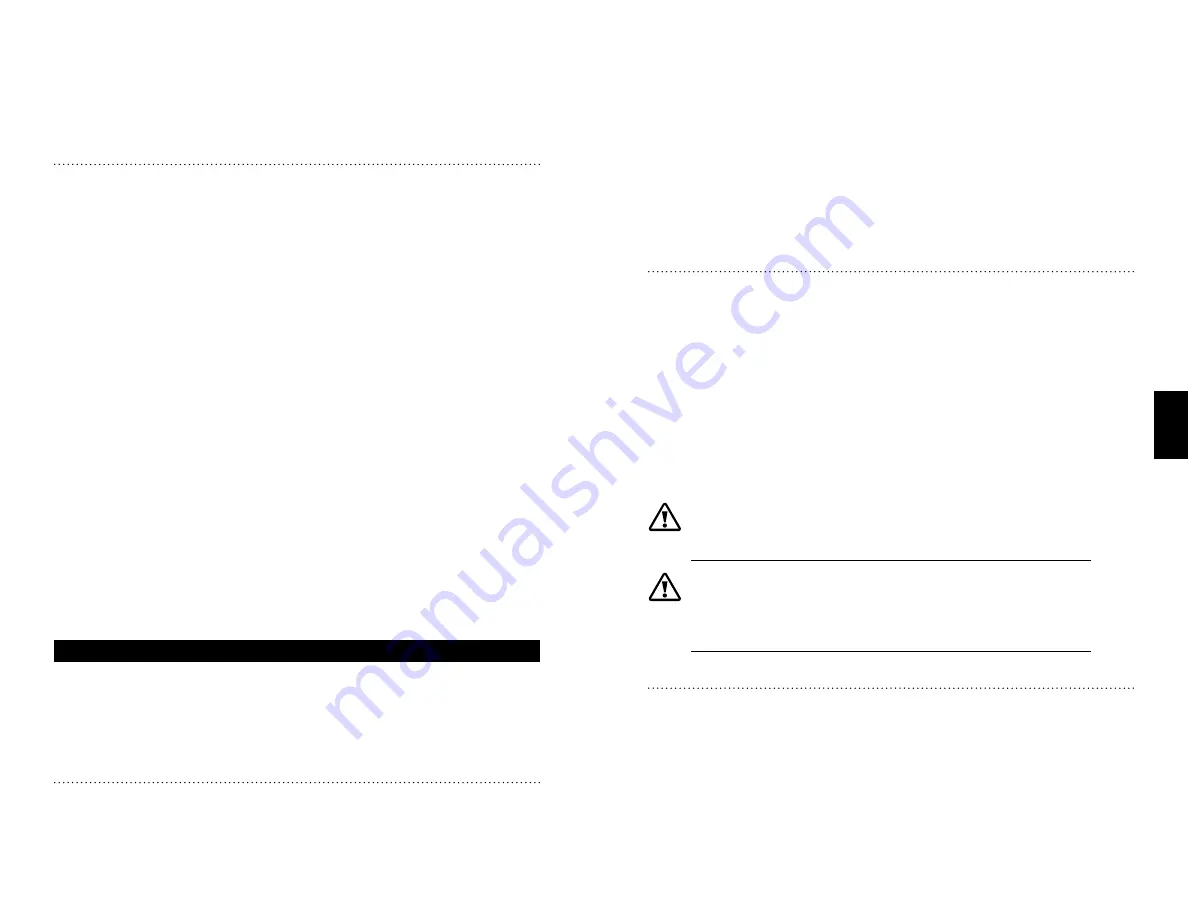
45
M O R N I N G S T A R C O R P O R A T I O N
6.0
44
L O A D C O N T R O L
After an LVD, the load reconnect voltages are 0.25 volts per battery cell
higher than the LVD (for example, in a 12V system the LVD
R
would be 1.5
volts above LVD). Battery voltages can rise quickly after an LVD, typically from
1.0 to 1.3 volts or more (12V system). The LVD
R
value must be high enough to
avoid cycling in and out of LVD.
5.3 LVD Warning
When the battery is discharging and the green LED changes to the next state
(G-Y LEDs on), there are four remaining transitions to LVD (refer to the LED
indications in Section 3.3). Each of these LED displays will serve as a
warning of an approaching LVD. The final warning is a blinking red LED state.
The amount of time from the initial G-Y display until the load disconnect will
depend on many factors. These include:
• The rate of discharge.
• The health of the battery
• The LVD setting
For a “typical” system with a healthy battery and an LVD setting of about 11.7
volts, there could be approximately 10 hours per LED transition. The LVD
would occur about 40 hours from the first G-Y display (under constant load
with no charging).
Another significant factor affecting the warning time is the LVD voltage
setpoint. Lower LVD voltage settings may result in the battery discharging
70% or 80% of its capacity. In this case, the battery’s very low charge state
will result in the voltage dropping much faster. At the lowest LVD settings,
there could be as little as 2 or 3 hours of warning between LED transitions
for a healthy battery.
The amount of time it takes to transition through the LEDs to LVD can vary
greatly for different systems. It may be worthwhile to measure the time it takes
for your system to transition from one LED state to the next. Do this under
“typical” discharging loads.
This will provide a good reference for how long it will take for your system
to reach LVD. It can also provide a benchmark for judging the health of your
battery over time.
6.0 Diversion Charge Control
The TriStar’s third mode of operation is diversion load battery charge control.
As the battery becomes fully charged, the TriStar will divert excess current
from the battery to a dedicated diversion load. This diversion load must be
large enough to absorb all the excess energy, but not too large to cause a
controller overload condition.
6.1 Diversion Charge Control
In the diversion mode, the TriStar will use PWM charging regulation to divert
excess current to an external load. As the battery becomes fully charged, the
FET switches are closed for longer periods of time to direct more current to
the diversion load.
As the battery charges, the diversion duty cycle will increase. When fully
charged, all the source energy will flow into the diversion load if there are
no other loads. The generating source is typically a wind or hydro generator.
Some solar systems also use diversion to heat water rather than open the
solar array and lose the energy.
The most important factor for successful diversion charge control is the
correct sizing of the diversion load. If too large, the controller’s protections
may open the FET switches and stop diverting current from the battery. This
condition can damage the battery.
If you are not confident and certain about the installation, a professional
installation by your dealer is recommended.
6.2 Diversion Current Ratings
The maximum diversion load current capability for the two TriStar versions is
45 amps (TS-45) and 60 amps (TS-60/M). The diversion loads must be sized
so that the peak load current cannot exceed these maximum ratings.
See section 6.4 below for selecting and sizing the diversion loads.
The total current for all combined charging sources (wind, hydro, solar) should
be equal or less than two-thirds of the controller’s current rating: 30A (TS-45)
and 40A (TS-60/M). This limit will provide a required margin for high winds
and high water flow rates as well as a margin for error in the rating and
selection of the diversion load. This protects against an overload and a safety
disconnect in the TriStar controller, which would leave the battery charging
unregulated.
CAUTION: If the TriStar’s rating is exceeded and the controller dis-
connects the diversion load, Morningstar will not be responsible for
any damage resulting to the system battery or other system compo-
nents. Refer to Morningstar’s Limited Warranty in Section 10.0.
PRUDENCE : Si la capacité du TriStar est dépassée et que le contrôleur
déconnecte la charge de diversion, Morningstar ne sera pas responsable
de tout dommage résultant de la batterie du système ou d’autres
composants du système. Reportez-vous à la Garantie limitée de
Morningstar dans la Section 10.0.
6.3 Standard Diversion Battery Charging Programs
The TriStar provides 7 standard diversion charging algorithms (programs) that
are selected with the DIP switches. An 8th algorithm can be used for custom
set-points using the PC software.
The table below summarizes the major parameters of the standard diversion
battery charging algorithms. Note that all the voltages are for 12V systems
(24V = 2X, 48V = 4X).