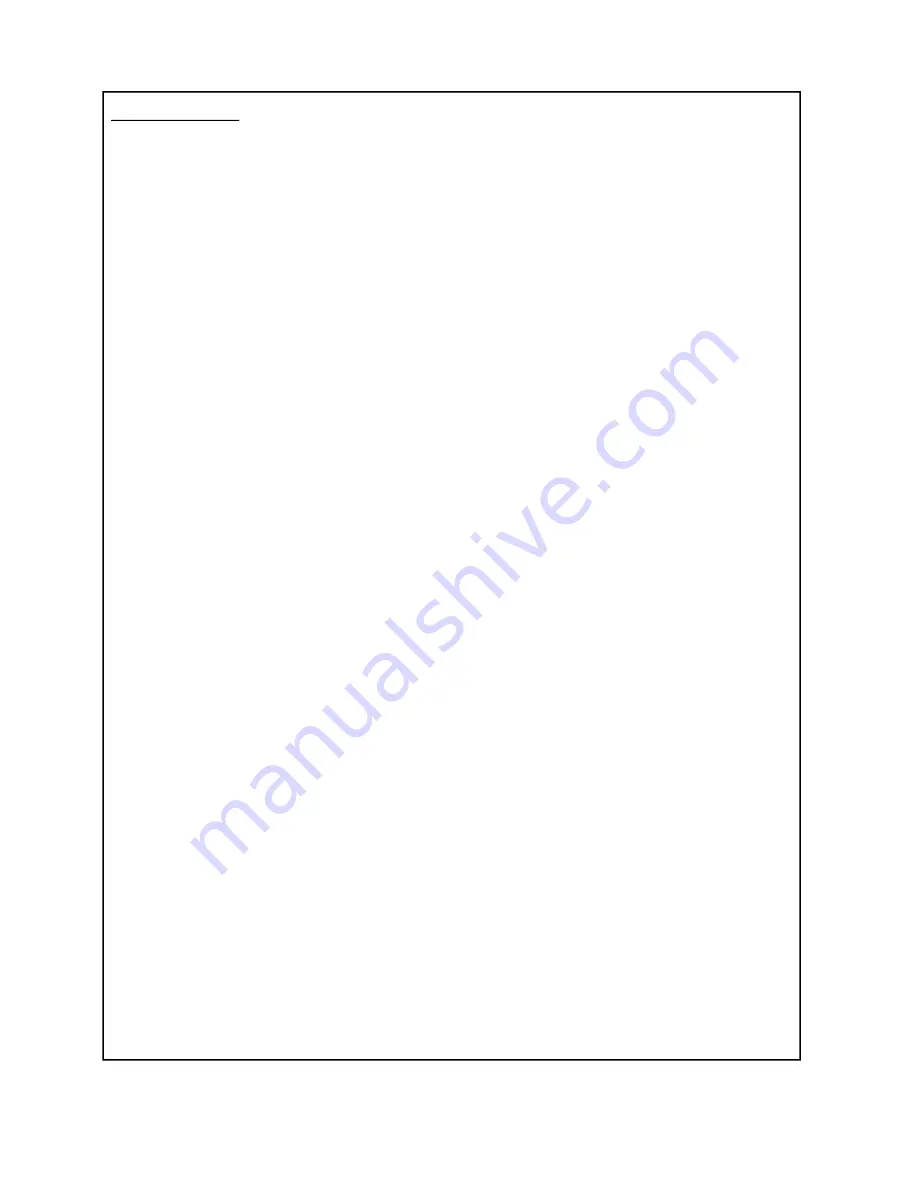
Page 27
SECTION G
ELECTRICS: REMOVAL/REFITTING PCB’s
REPLACEMENT OF STEPPER DRIVE BOARDS
There is one Dual Stepper Driver Board, and three Single Stepper Driver Boards; which supply
the drive motors with the correct power.
These are located as above, and can be accessed in the same manner.
Cut any cable ties and unplug the green plugs and
Unscrew the fixings attaching the PCB to the panel.
Switch the mains power off and disconnect from the mains supply.
spade connectors.
Refitting is the reverse of above but care should be taken to ensure that the rotary switch and
the dip switches are correctly set for the correct PCB, see Wiring Diagram.
Attach spade terminals in the correct positions and refit.
This controls the fold knives motor and the main roller drive motor and is located as above.
(see section on covers for removal).
Switch the mains power off and disconnect from the mains supply.
Unplug all the green plugs from the PCB.
Using a posi-drive screw driver, unscrew the five fixing screws and carefully remove the PCB.
Replacement is the reverse procedure ensure that the switches are correctly set.
These supply power to the machine and are located inside the layside cover. (see section on
covers for removal).
Switch the mains power off.
Unscrew all connections from the terminal block on the power supply.
Using a No1 Posi-drive screwdriver remove the screw inside the electrical compartment and
remove the unit by sliding forwards and out.
REPLACEMENT OF DUAL STEPPER BOARD
LARGE POWER SUPPLY.
SYSTEM
Digifold Pro
Содержание Digifold Pro CB
Страница 7: ...Page 7 SYSTEM BLANK PAGE Digifold Pro ...
Страница 13: ...Page 13 SYSTEM Digifold Pro ...
Страница 17: ...Page 17 SYSTEM BLANK PAGE Digifold Pro ...
Страница 21: ...Page 21 SYSTEM Layedge Side Operator Side Digifold Pro ...
Страница 37: ...SYSTEM Page 37 BLANK PAGE Digifold Pro ...
Страница 39: ...Page 39 SYSTEM Digifold Pro ...
Страница 53: ...Page 53 BLANK PAGE Digifold Pro SYSTEM ...
Страница 55: ...Page 55 Digifold Pro SYSTEM ...
Страница 61: ...Page 61 Digifold Pro SYSTEM ...
Страница 73: ...Page 73 Digifold Pro SYSTEM ...
Страница 79: ...Page 79 Digifold Pro SYSTEM ...
Страница 88: ...Page 88 CREASING FOLDING Section N BL YEL ...
Страница 92: ...Page 92 CREASING FOLDING Mod No Rev Mod Description Date Mod By REVISION HISTORY ...