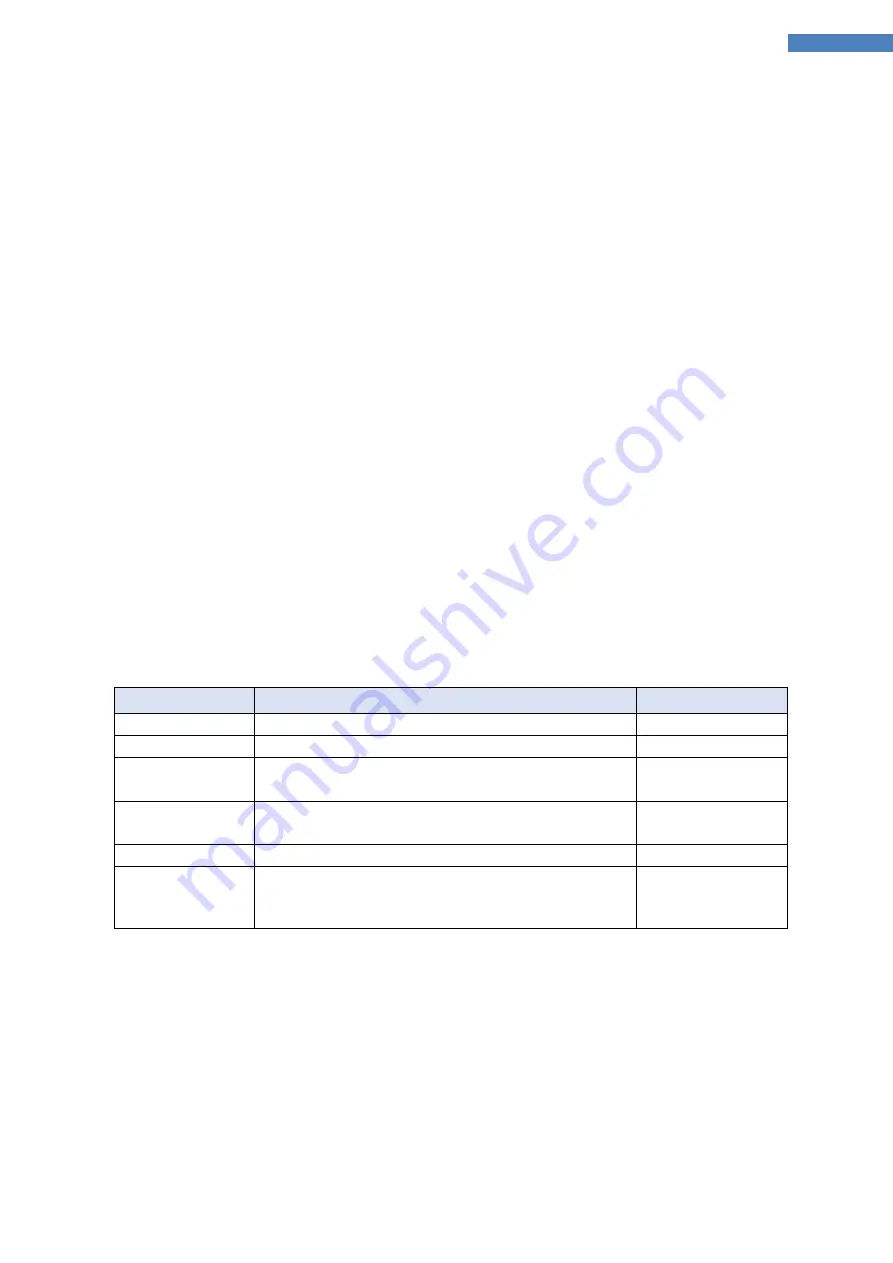
29
(2) Communication & I/O Command Mode
This controller can execute control operation by communication and I/O command
transmitted from the upper controller.
①
Plus-R Mode
:
Support Plus-R network, I/O command, Position table functions
②
MODBUS-RTU
:
Support MODBUS-RTU network, I/O command, Position table
functions
③
MODBUS-ASC
:
Support MODBUS-ASC network, I/O command, Position table
functions
Position Table Operation Sequence
The system can execute sequential operation by position table at the I/O command mode.
①
By using PT A0 ~ PT A6 input signal or DLL program, set PT number to be
operated.
②
In case of Servo OFF, set the controller to Servo ON by communication program or
Servo ON control input.
③
Start to operate by rising edge of PT Start input signal or communication program.
Stopping Operation of Position Table
When the motor is executing continuous operation of position table with CK10, stop
executing position table by following methods.
To use DLL program or control input signal corresponding to ‘Stop’ and ‘E-Stop’.
Position Control Operation
You can configure the operation by setting the following parameters with the user GUI
program or DLL program.
Parameter Name
Setting contents
Range
Axis Max Speed Maximum allowable speed
1~2,500,000[pps]
Axis Start Speed Start speed when acceleration starts
1~35,000[pps]
Axis Acc Time
Required time until the motor reaches the target
speed from stop status
1~9,999[ms]
Axis Dec Time
Required time until the motor reaches from the
constant speed to the stop status
1~9,999[ms]
Motion Dir
To select motion direction (CW or CCW)
0~1
Pulse per
Revolution
Number of pulses per revolution.
The range of ‘Axis Max Speed’ parameter is
depend on this value.
0~15