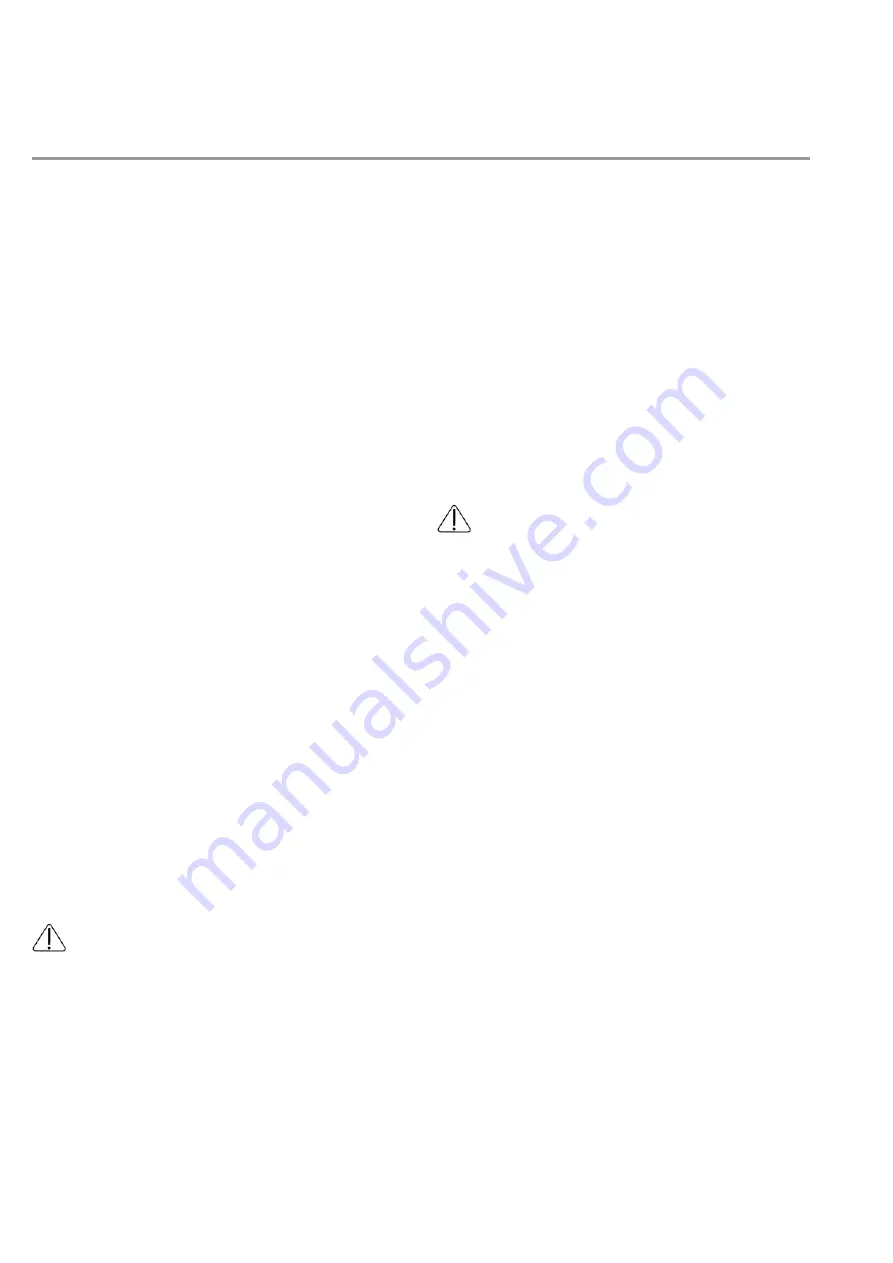
5. Maintenance
ProCon HT 150 / HT 225
•
Check the hydraulic pressure switch
Put the appliance in the heating mode and slowly release the
system pressure. Below 0.5 bar the pressure switch should turn
off the burner. In the multifunction display of the control unit
the error display will be permanently on. The codes „1“ and
„19“ will appear on the multifunction display alternately. During
system refill (pressure > 0.8 bar) the burner will restart and the
error signal will disappear.
•
Check expansion tank (MAG)
Check the inlet pressure of the pressure expansion tank.
If the inlet pressure of the pressure expansion tank is lower than the
system static pressure, continue to fill in as much nitrogen as possible
until the inlet pressure is higher than the system static pressure.
Then fill the appliance until the filling pressure is higher than the
inlet pressure of the expansion tank (see Check system pressure).
•
Check system pressure
Check the system pressure. In the case of "open loop” heating
systems the minimum system pressure should be 0.8 bar and a SPIRO
VENT air separator should be inserted. In the case of “closed loop”
heating systems with pressure expansion tank, the minimum system
pressure should be 1 bar and the maximum system pressure
should be 2.5.
•
Check water connections
Check inside and outside the appliance to see whether there are
any leakages on the flanges and joints. Even small leakages must be
repaired.
•
Check burner and burner plate
Remove the burner plate with fan, suction duct and the burner
from the boiler body.
Check the seals and insulations of the burner plate for damages;
if possible, replace them. Check the wire mesh on the surface of
the burner. If the mesh is damaged, replace the burner as well
as the burner seals.
Do not clean the burner mechanically. It may damage the
surface of the burner.
•
Check the ignition and ionization electrodes
Check the electrodes for dirt and wear. If a white layer has formed on
the electrode, remove it with sandpaper. The clearance between the
electrode and the burner surface should be approx. 4 mm. If you
replace the electrode, you must also change the graphite seal. Use
ceramic paste CRC (94.17464-5004) to mount the fastening
screws of the ignition electrode.
•
Clean the combustion chamber / heating surfaces
Check the heating gas end of the heat exchanger for dirt. Where
necessary, clean the heat exchanger with a vacuum cleaner or with a
nylon brush (does not use PVCs or wire brushes!)
For stubborn dirt, you can simply apply water. You can also use solvent-
free cleaning agents.
You can remove soot deposits with alkaline agents that contain
additional surfactants (e.g. Fauch 600).
For films and yellowish-brown surface discolorations, you can use
slightly acidic, chloride-free, phosphorous-based cleaning agents
(e.g. Antox 75 E).
Manufacturer of Antox 75 and Fauch
600: Oakite (Europe) GmbH
Trakehner Straße 3
60487 Frankfurt
The cleaning agents must not contain hydrocarbon-
based solvents or potassium.
Rinse the surfaces thoroughly with water after cleaning.
•
Check and clean the condensed water siphon
Carry out a visual inspection on the hoses of the inner siphon.
•
Check neutralization device
Check the functioning of the neutralization device as described in
the corresponding instruction manual. The pH value of the
condensate should be lower than 6.5.
•
Check CO
2
settings
After completing all maintenance work and proper assembly of the
appliance, check the set CO
2 values
with closed cap once again and
set the operation mode on the control to automatic.
•
Compact gas units
The compact gas units are maintenance-free. Check only the
housing for possible damages.
48
Содержание ProCon HT 150
Страница 1: ...1...
Страница 29: ......
Страница 62: ...7 Technical documentation ProCon HT 150 HT 225 7 9 Measurements and connection dimensions Fig 32 62...
Страница 74: ...Notes ProCon HT 150 HT 225 74...
Страница 75: ...HT 150 HT 225 GWB 75 Notes 75...
Страница 76: ...76...