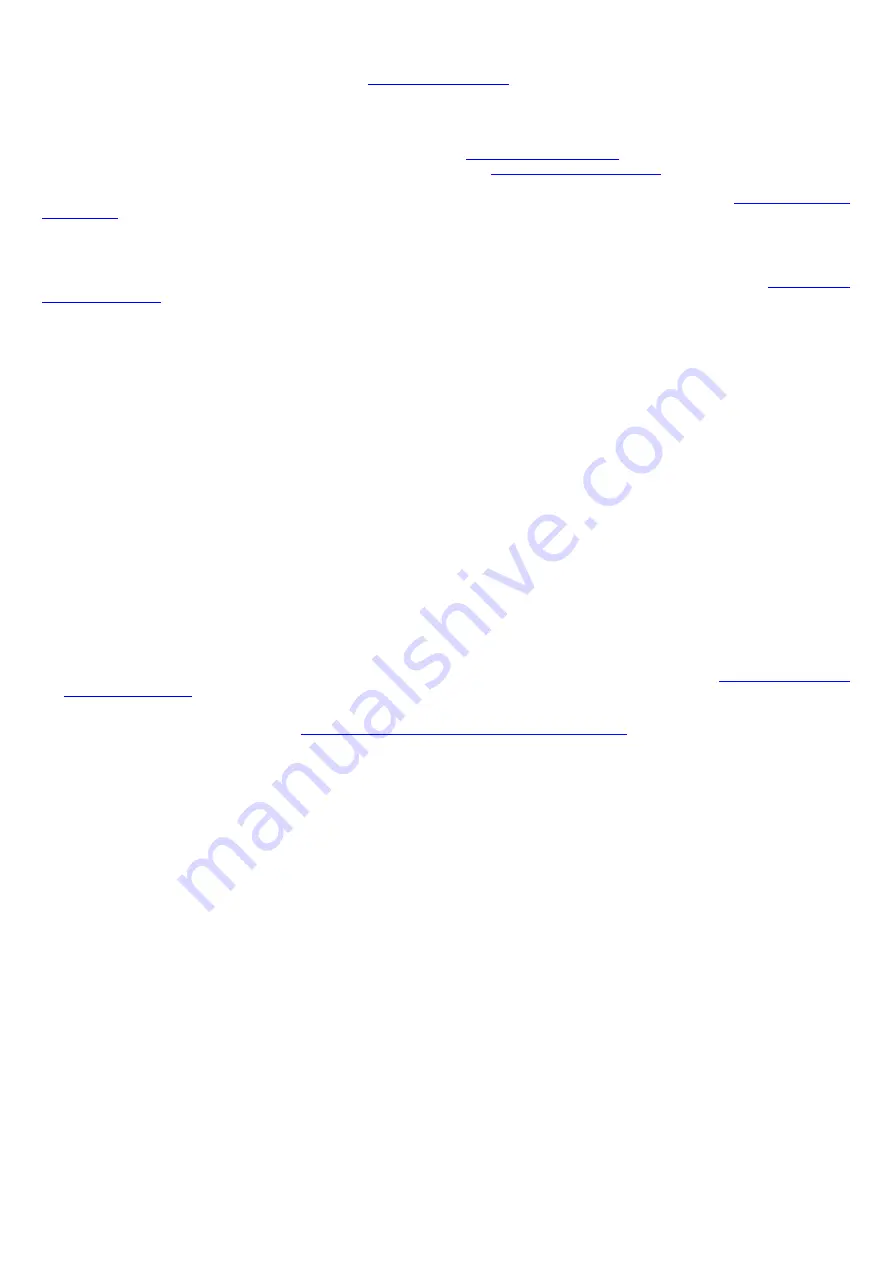
4 / 72
HBC-series V7 LV+MV
First steps
First, before you start run controller, we recommend read
solder (mounted) suitable connectors
select basic of driving type
(car, boat, aircraft / PWM, constant rpm, constant torque).
This you make by program „
Controller 2
“
connect controller to motor and other parts
connect controller to driving (master) system,
see more
Basic controller connection
when you want use
sensor motor
,
read first instruction here
:
Sensor motors and controllers
For first tests you can use controller with pre-defined average value of all parameters (type cells =
Automat 78%
Of course, optimal behaviors of the controller and your system you achieve only by correct (optimize) settings and tuning corre-
sponding parameters.
Parameter setting by program „
Controller 2
“ is very simple and intuitive and enable easy and transparent setting all controller features for op-
timal behavior. If you wish to enjoy all the possibilities of the controller, please refer to the whole manual.
When you set parameters, include throttle limits (= programed) or range of driving signal or driving voltage, you can start
Basic Recommendations
Shorten the cables between the battery and the controller as much as possible
(however not under 5 cm, there is a possibility of un-
soldering wires from the controller)
! The higher the power and the "faster" the used motor, the more important is this requirement !
If you need to prolong the power conductors to batteries (distance between the controller and the batteries > 50 cm), it is neces-
sary to solder additional capacitor blocks
(so more than capacitors used in the controller itself)!!! Additional capacitors must be the
same as used in controllers, i.e.
„
very low ESR
“,
105°C.
It is advantageous to use a block of capacitors
10X1G0.63
or
8X0G3.120
, etc. Al-
so necessary used cables with correspond cross section !
Use only quality and well dimensioned connectors for connect battery to the controller !
Very suitable and very reliable connectors
are MP JET 5.0
– 5.5 – 6.0 mm, which are dimensioned for currents up to 200 – 300A. MP JET connectors feature small transition re-
sistance, small dimensions and very firm connection (they do not come apart themselves as some other types do).
We recommend to put the socket on the “
–
“ wire
(
black wire
)
of the controller and the plug on the “
+
” wire
(
red wire
)
.
If you use for both
cables to the same connector (i.e. plug for example), the probability of polarity reversal (and thus destroy the controller) is very high.
Another good possibility is to use ring terminals and screwing to the controller.
!!! Warning, reversal of battery poles will reliably destroy the controller !
(The damage however, may not show immediately, but in some
later runs)
!
If you use the connectors to the motor terminals,
(marked
„
A
“, „
B
“, „
C
“)
apply to them the same criteria. If you choose the connectors,
on the controller side cables solder socket
!
Insulate the connectors after soldering, e.g. using heat shrinking sleeve.
Never connect more cells (higher voltage) than is specified in technical data, you can damage controller.
We always recommend first connect the traction battery via the auxiliary connector with a serial resistor, see more
“
If you use for electronics feeding an external source (battery 14 up to 35V, etc.) must always be connected (turn-on) the battery first and is
disconnected (turn-off) last - see chapter
Connecting controller to the traction supply and turning on
Short circuit of motor wires together (when batteries are connected) or short cut of these wires to the feeding voltage (
“
+
”
or
“
–
“
cables) results in damage or destroy of the controller !
Short circuit on the motor cables or feeding cables to any other wires
(control signal, communication link, …)
caused damaging of
the controller !
If the controller is powered by an AC adapter (mains power supply, not battery) should not even brake ! or off freewheel !!!
Freewheel must be s
et “without synchro”. If you need to brake when powered by an AC adaptermust be used the braking resis-
tors with appropriate management
(control signal for braking resistors controlling provide controller yourself)
!!! If you braking and the
controller is feeding from inverter, etc. without controlled braking resistors are very likely to destroy the controller !!!
Do not underestimate the quality of traction batteries, has a significant influence on the system behavior.
Do not SWITCH OFF controller or PLUG OFF BATTERY when motor RUN or when it is still turning
– that may lead to damage or
destroy of the controller !!! This also applies to spontaneous disconnecting of the connector during operation, e.g. by vibra-
tions!!!
This is why connectors should be chosen very carefully
– see recommendation above
.
The only exception is a safety discon-
nection (Emergency disconnecting).
Be careful for using damaged motor or motor overloading, controller damaging is possible.
One controller can control only one motor.
It is necessary to cool the controller in operation with flowing air (or water for water coolers). Do not obstruct the access of cooling airflow
to the controller, e.g. by packing the controller in foam.
It is recommended to measure current drawn from battery with charged battery and full load (protection of the battery and controller).
Only clamp Ampermeters using is permitted
(always for DC current, on the battery cables).
Never use Ampermeter inserted to the circuit
(i.e. between battery and controller)
– you can damage controller !
It is convenient to use measurements carried out by the controller during the drive and their display using PC.
Please remember,
that even one additional cog on pinion of the motor significantly increase the drawn currents. With acceleration set faster, currents in the
start-up peak rise very fast, and that up to many times of the current in the steady state. It is necessary to do the measurement with the
hardest batteries, which you wish to use in the set. This will prevent possible problems with overloading the controller, motor and batteries.
Controllers designed for sensor motors can work also with sensorless motors
– depend only on the correct parameter settings (motor type).