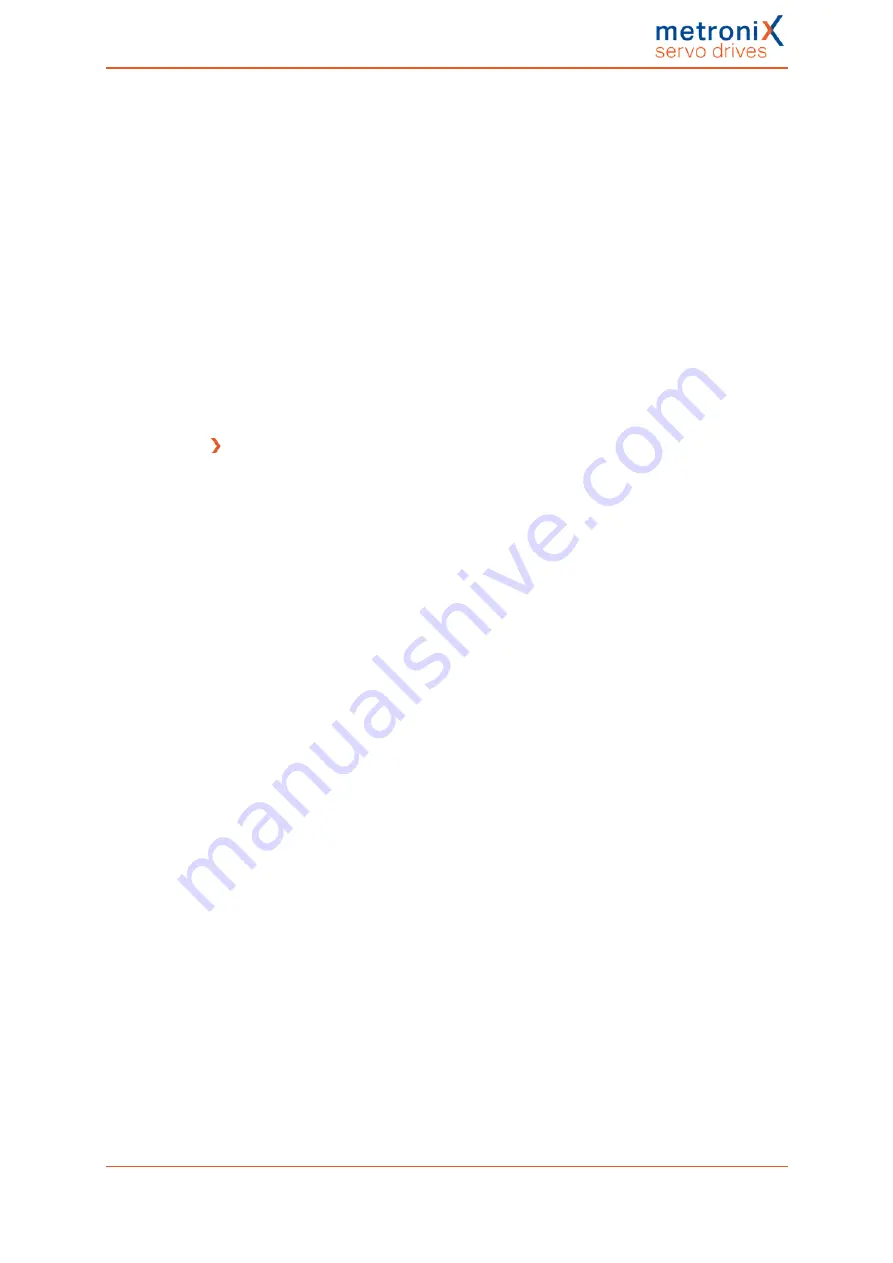
7 Additional settings
To adapt the BiSS position taken from the digital raw value of the encoder to the internal
absolute position and rotor position, the following variants can be used:
Relative-linear
: The BiSS data are available only as a data frame without any connection
with regard to the rotor position. The line count must be defined so that it matches the
commutation position. The position is always different whenever the system is switched
on and there is no connection with regard to the rotor position. For example, after a reset,
the position is always zero (regardless of the position of the rotor) and it can become
positive or negative. The encoder is installed on a linear motor. The commutation position
must be determined, and homing is required.
Rotative single-turn and multi-turn
: There is always a rotary motor and the data frame can
be divided into single-turn and multi-turn segments .
Absolute-linear
: A data frame that must be mapped to a rotary system with a freely
selectable line count (no power of two). The encoder is installed on a linear motor. It is not
necessary to determine the commutation position, and homing is not required.
Start-up notes
1. Perform the bit adaptation for single-turn und multi-turn revolutions in accordance
with the encoder data sheet. There should not be any encoder error and the
firmware can perform the CRC.
2. Check the actual position that is indicated in the status window. One mechanical
revolution of the motor must correspond to one indicated revolution. If an
adaptation is necessary, the line count can be modified.
3. In the case of linear motors, the offset of one pole pair must be mapped precisely to
the rotor position (number of pole pairs 1).
4. To check the range of movement of absolute encoders without a homing run, tests
concerning the repeatability of the actual position must be performed at various
different positions within the range of movement.
5. Then, the indication of the actual position can be configured with "mm" as the
display unit, for example, in the "Display units" window.
Product manual BL 4000-C
Page 147 of 298
Содержание smartServo BL 4000-C Series
Страница 1: ...Important Read thoroughly before use Retain for future reference Product manual smartServo BL 4000 C ...
Страница 261: ...15 Appendix 15 2 CE conformity in accordance with the Machinery Directive Product manual BL 4000 C Page 261 of 298 ...
Страница 262: ...15 Appendix Product manual BL 4000 C Page 262 of 298 ...
Страница 263: ...15 Appendix 15 3 cULus certification Product manual BL 4000 C Page 263 of 298 ...