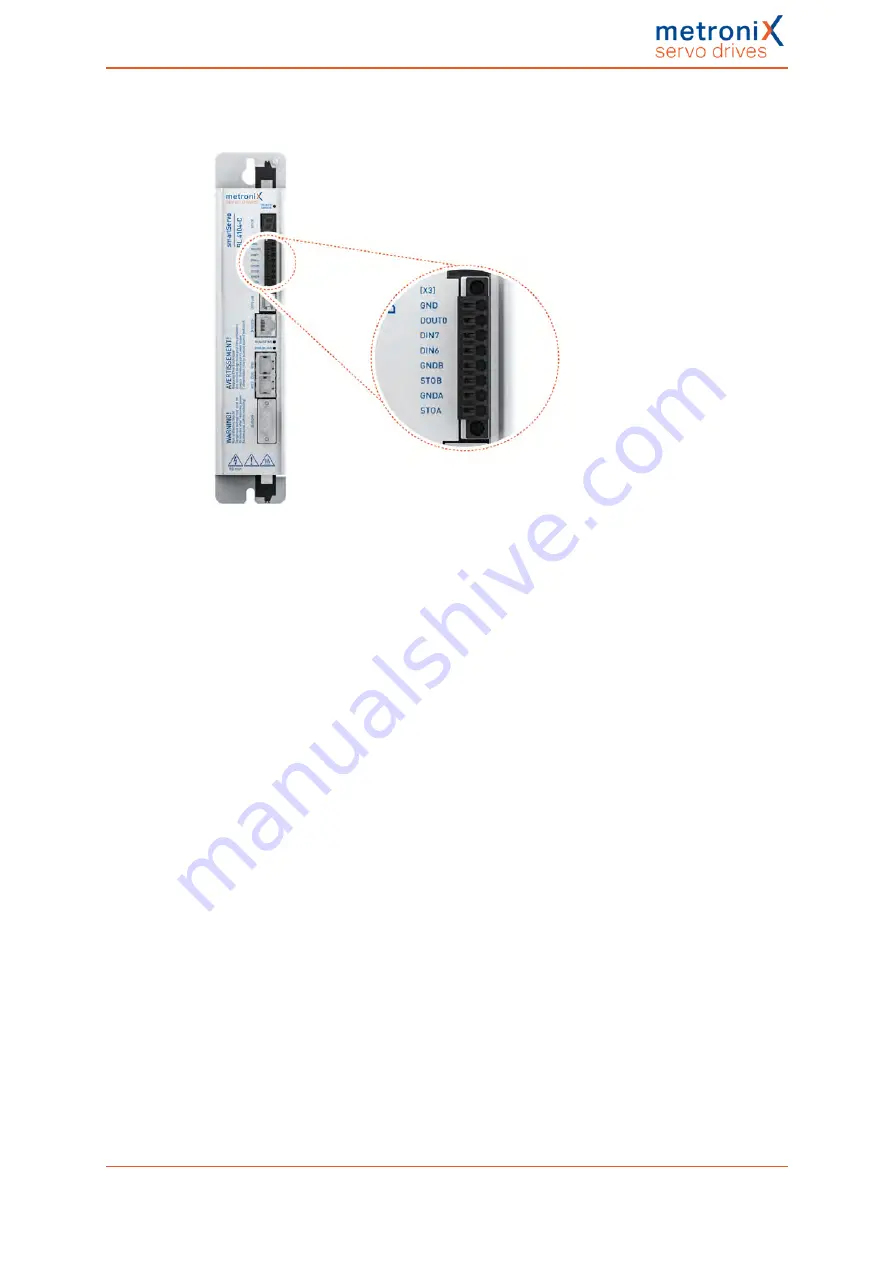
8 STO (safe torque off)
8.5.2
Overview of the [X3] interface
Figure 118: Position of connector X3
At its front, the servo drive has an 8-pin connector [X3] for
l
the STO control inputs,
l
the digital output DOUT0, and
l
the digital inputs DIN 6 and DIN 7
The STO safety function is requested exclusively via the two digital control inputs STOA
and STOB. The safety-oriented integration of additional interfaces is not
necessary/intended.
The servo drive does not monitor the input circuit for cross-circuit faults.
The [X3] interface enables the direct connection of active and passive sensors as
DOUT0/GND provide a short-circuit-proof 24 V supply voltage (see section 13.12
Product manual BL 4000-C
Page 197 of 298
Содержание smartServo BL 4000-C Series
Страница 1: ...Important Read thoroughly before use Retain for future reference Product manual smartServo BL 4000 C ...
Страница 261: ...15 Appendix 15 2 CE conformity in accordance with the Machinery Directive Product manual BL 4000 C Page 261 of 298 ...
Страница 262: ...15 Appendix Product manual BL 4000 C Page 262 of 298 ...
Страница 263: ...15 Appendix 15 3 cULus certification Product manual BL 4000 C Page 263 of 298 ...