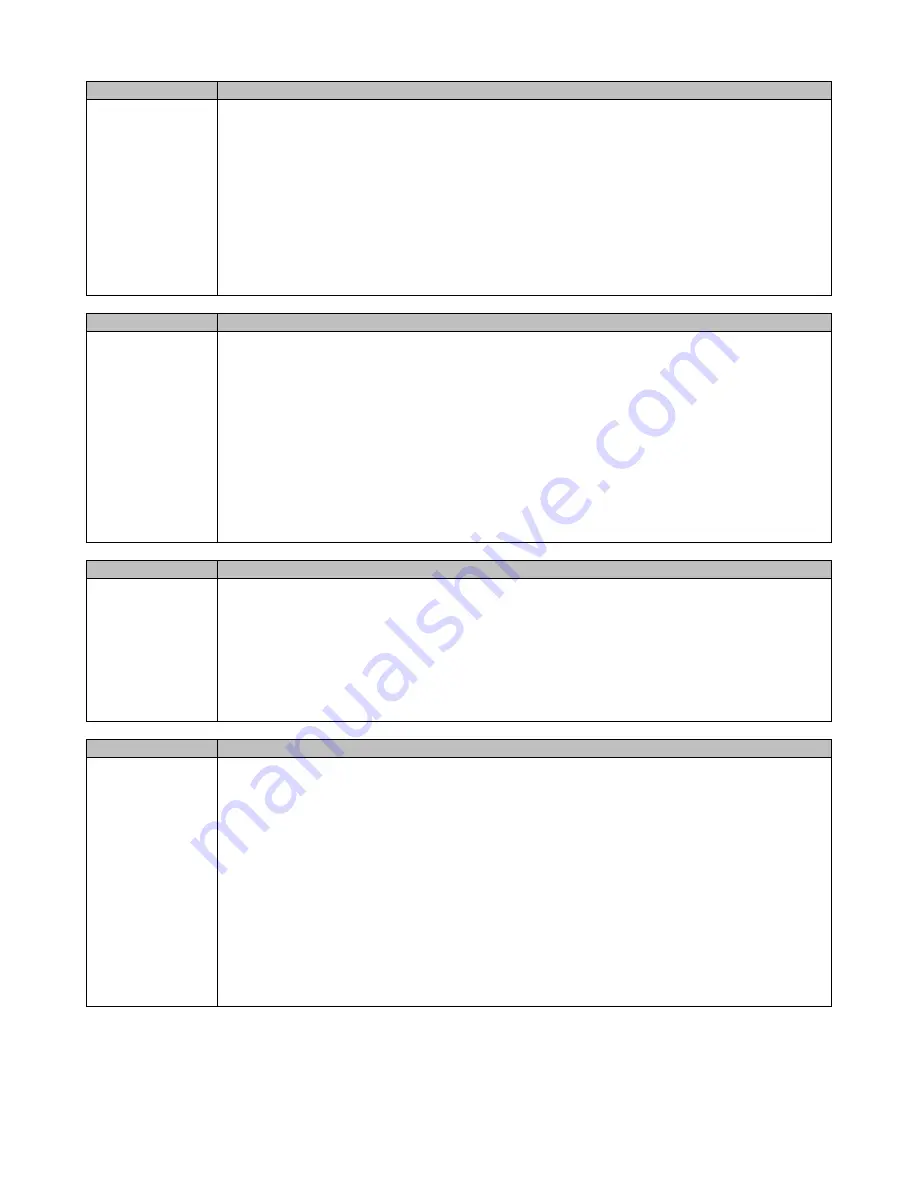
BAM 1020-9800 Manual Rev W.docx
Page 62
Problem: The
airflow rate is too low and won’t adjust up to 16.70 L/min.
Cause/Solution:
•
The gray plastic pump mufflers on the Medo pumps may clog up after several
months. Replace it or drill a hole in the end of it for a temporary fix. The brass
mufflers on Gast pumps can often be cleaned.
•
Some users replace the pump muffler with a 30 inch length of air tubing. This will
not clog and reduces the pump noise as well as the mufflers do.
•
The vacuum pump may need to be rebuilt after about 2 years. Medo pumps
slowly loose flow capacity as the pump wears out. Eventually, the flow capacity
drops below 16.70 lpm when it needs to be rebuilt.
•
Checking the 18.4 L/min point during the regular 3-point flow audits verifies the
pump capacity.
•
Check the inlet and PM heads for obstructions.
Problem: The airflow is stuck at a particular rate, and will not change.
Cause/Solution:
•
The flow controller unit on some older units can become stuck. If your flow
controller does not have a small circuit board mounted directly on the motor, it
needs to be upgraded. Contact the Service dept.
•
Perform the 3-point flow audit in the TEST > FLOW screen. The BAM should try
to regulate to these flow values. If the flow does not change, the flow controller
may not be working.
•
Unplug the pump power while performing a 3-point flow check. With the pump off,
you should be able to clearly hear the flow controller pulse at 1-second intervals
as it rotates and attempts to regulate the flow. If not, the flow controller is not
working or the circuit board output is not working.
•
If the flow regulates lower, but not higher than 16.70 lpm, the pump is probably
worn out, or there is a leak.
Problem: The
nozzle gets stuck in the UP position, or won’t press down onto the tape fully.
Cause/Solution:
•
With the nozzle in the down position, lift the nozzle up and down with your thumb
and determine if it feels sticky or gritty.
•
The nozzle O-ring eventually breaks down and needs to be replaced. See Section
7.6 for instructions.
•
The brass nozzle bushings may have grit in them. See Section 7.6. Remove the
nozzle and clean the parts. A shim kit is required for nozzle reassembly.
•
A stuck nozzle is sometimes caused by a misaligned inlet tube. Make sure it is
straight up and perpendicular to the top of the BAM 1020.
Problem: The BAM 1020 has flow leaks, even after cleaning the nozzle and vane.
Cause/Solution:
•
The nozzle may be sticking as described above. Verify that the nozzle up/down
motion is smooth and complete. If the nozzle feels sticky or gritty, it will not seal
properly.
•
Check the O-rings on the sharp-cut cyclone (if used). These frequently leak.
•
Check the zero of the flow sensor in the BAM: Perform another leak check, but
disconnect the tubing between the pump and the BAM, so there can be no air
flow through the BAM 1020. Verify that the flow reading on the BAM reads less
than 0.2 L/min. If not, the flow sensor
Q
0
zero offset setting may need to be
adjusted in the SETUP > CALIBRATE menu. The Q
0
setting is usually very close
to zero.
•
Check for bad O-rings on the BAM inlet tube receiver.
•
Remove the BAM case cover and inspect all air fittings inside the BAM. These are
compression fittings, and must be fully inserted to prevent leaks.
•
Inspect the internal and external flow system for split or cracked air tubing.