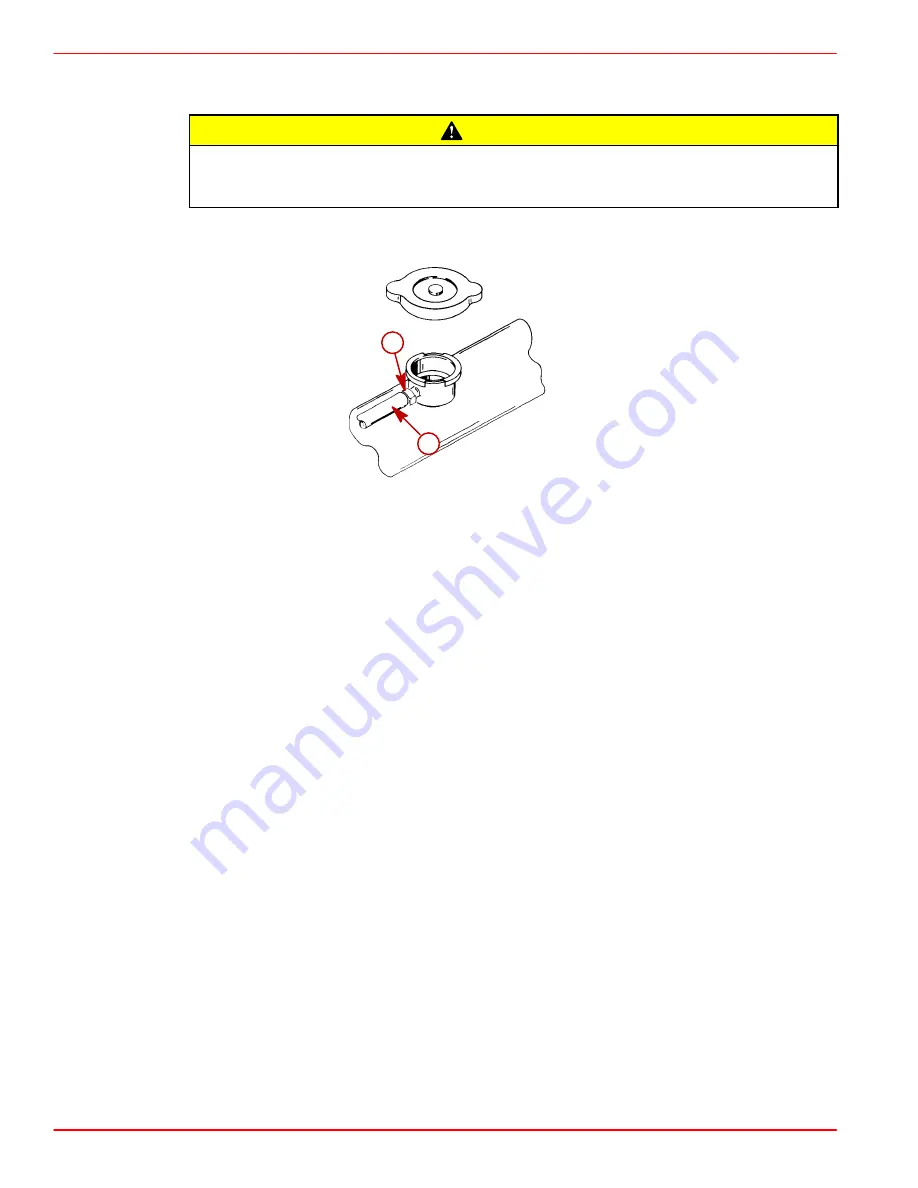
GASOLINE STERNDRIVE INSTALLATION MANUAL
Page 66 of 137
90-860172011
Coolant Recovery System
CAUTION
Avoid engine overheating and subsequent damage to engine. The coolant recovery
system will not operate properly without proper sealing. Plastic tubing MUST seal
completely at connections.
1. Connect plastic tubing to bayonet fitting on heat exchanger. Secure with tubing clamp
provided.
70548
a
b
a -
Plastic Tubing
b -
Tubing Clamp
1. Remove cap from coolant recovery reservoir and fill to FULL mark with coolant solution.
2. Reinstall cap.