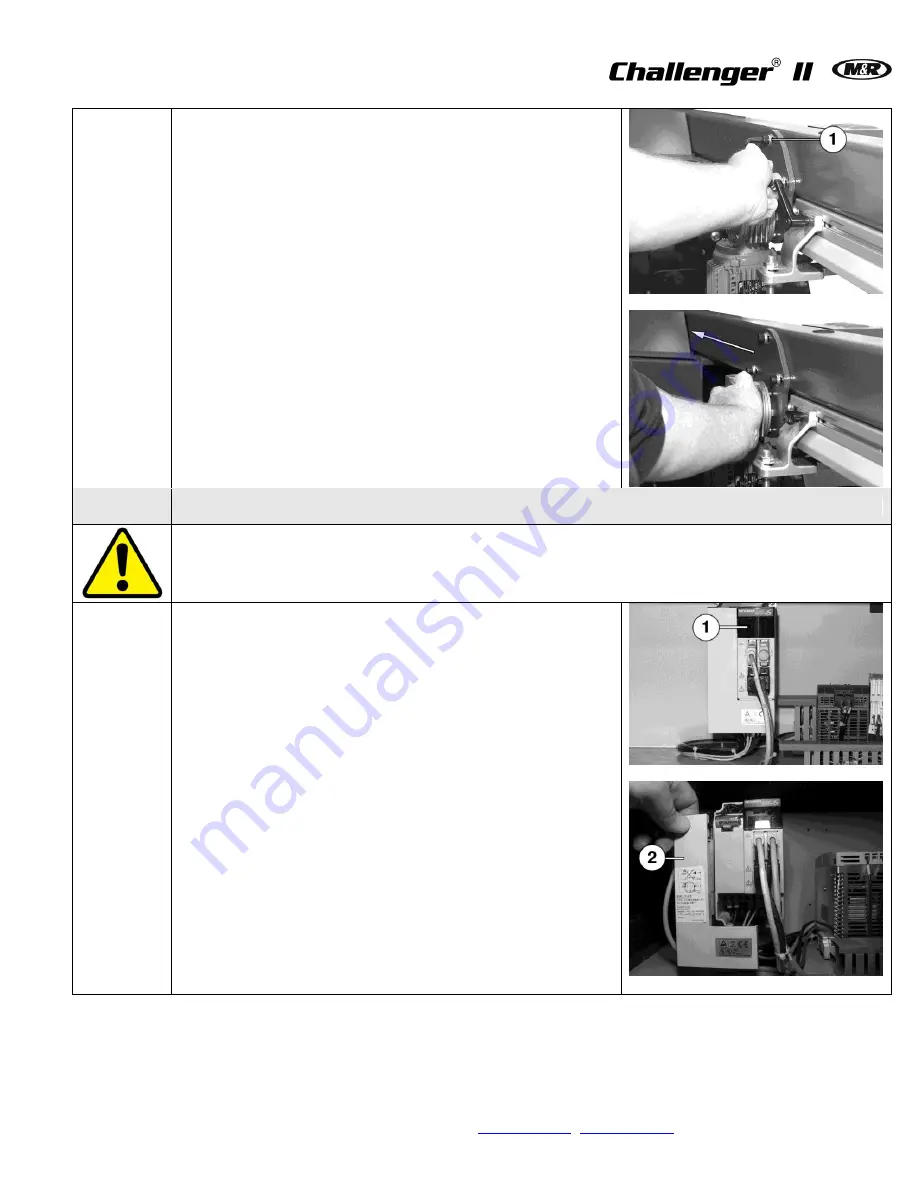
V.033114
M&R Companies 1N 372 Main St. Glen Ellyn, IL 60137 USA
69
Tel: +630-858-6101 Fax: +630-858-6134
as shown.
IMPORTANT:
Do not use pry bars or other tools as levers to
move the Print Carriage Drive Assembly.
4. While holding the Print Carriage Drive Assembly in position,
tighten the three socket cap screws (1).
Frequency
Maintenance
WARNING:
To prevent possible injury to personnel and/or damage to the equipment, lock out and tag the
electrical service and compressed air supply to the equipment.
Every
Three
Years
Replace Servo Amplifier Batteries
1 - Servo Battery (M&R Part No. 1017147)
IMPORTANT:
This procedure requires electrical power to be
connected to the press.
IMPORTANT:
The new batteries must be installed within five
minutes of removal of the old battery. This will ensure the
preservation of program data in the Servo Amplifier memory.
1. Open the access door on the lower electrical enclosure
mounted to the indexer chassis.
2. Locate both Servo Amplifier units (1 & 2) mounted to the rear
wall. Remove the access cover on the Servo Amplifier (2)
and flip up the LED cover assembly on Servo Amplifier (1) to
expose the battery connector.