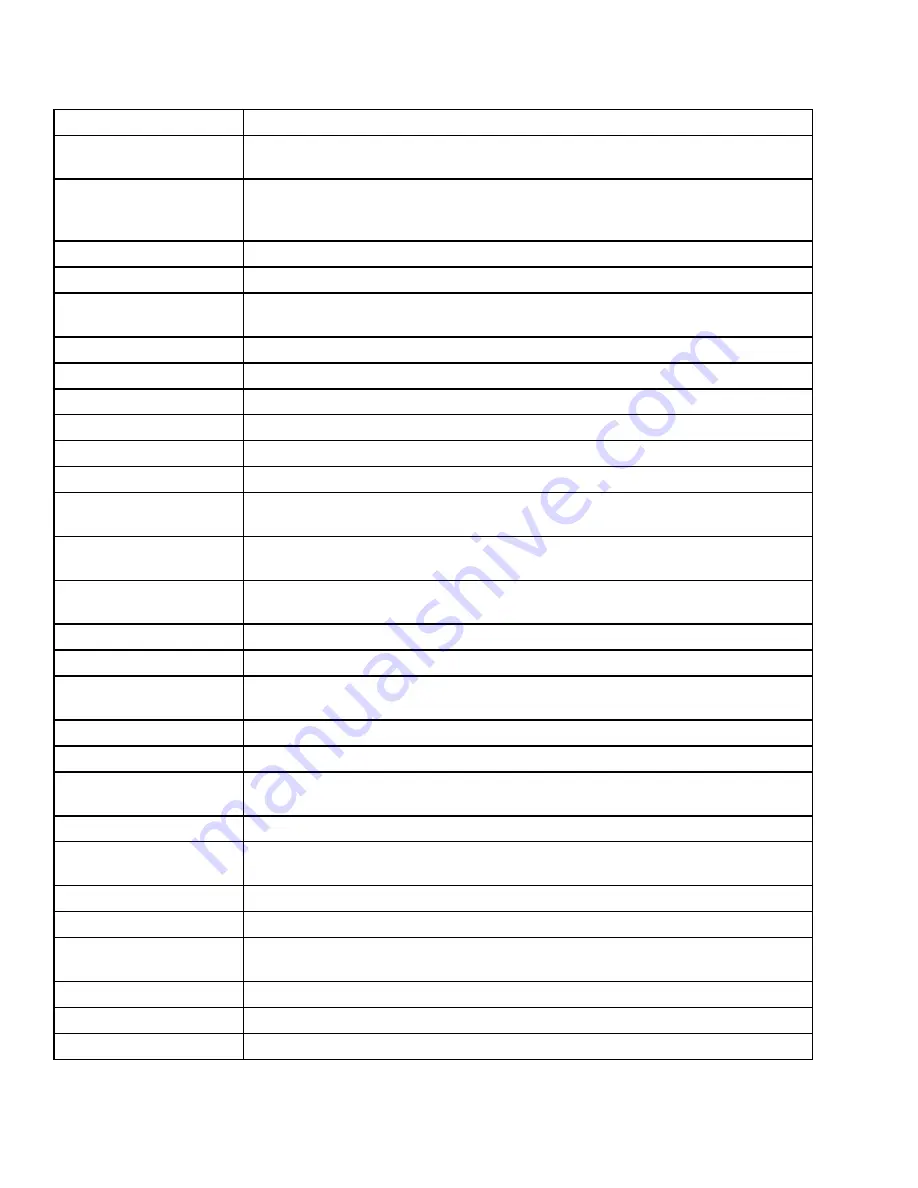
Term
De
fi
nition
Header
A machine that cuts and lays crop into a windrow and is attached to a
self-propelled windrower
Hex key
A tool of hexagonal cross-section used to drive bolts and screws that have a
hexagonal socket in head (internal-wrenching hexagon drive); also known as an
Allen key and various other synonyms
HDS
Hydraulic deck shift
hp
Horsepower
JIC
Joint Industrial Council: A standards body that developed standard sizing and
shape for original 37°
fl
ared
fi
tting
Knife
A cutting device which uses a reciprocating cutter (also called a sickle)
M1 Series windrower
MacDon M1170 and M1240 self-propelled windrowers
MDS
Mechanical deck shift
n/a
Not applicable
Nut
An internally threaded fastener that is designed to be paired with a bolt
N-DETENT
The slot opposite the NEUTRAL position on operator’s console
NPT
National Pipe Thread: A style of
fi
tting used for low pressure port openings Threads
on NPT
fi
ttings are uniquely tapered for an interference
fi
t
ORB
O-ring boss: A style of
fi
tting commonly used in port opening on manifolds, pumps,
and motors
ORFS
O-ring face seal: A style of
fi
tting commonly used for connecting hoses and tubes
This style of
fi
tting is also commonly called ORS, which stands for O-ring seal
rpm
Revolutions per minute
R Series header
MacDon R80 and R85 rotary disc headers
RoHS (Reduction of
Hazardous Substances)
A directive by the European Union to restrict use of certain hazardous substances
(such as hexavalent chromium used in some yellow zinc platings)
SAE
Society of Automotive Engineers
SCR
Selective catalytic reduction
Screw
A headed and externally threaded fastener that threads into preformed threads or
forms its own thread into a mating part
SDD
Single-draper drive
Self-Propelled (SP)
Windrower
Self-propelled machine consisting of a power unit with a header
SK
Single knife
SKD
Single-knife drive
Soft joint
A joint made with use of a fastener where joining materials are compressible or
experience relaxation over a period of time
spm
Strokes per minute
Tension
Axial load placed on a bolt or screw, usually measured in Newtons (N) or pounds (lb.)
TFFT
Turns from
fi
nger tight
214053
30
Revision A
Содержание M1240
Страница 29: ...SAFETY 1 11 Safety Sign Locations Figure 1 31 Safety Sign Locations 214053 17 Revision A ...
Страница 40: ......
Страница 116: ......
Страница 246: ......
Страница 352: ...MAINTENANCE AND SERVICING Figure 5 175 Main Fuse Panel Decal MD 207815 214053 340 Revision A ...
Страница 353: ...MAINTENANCE AND SERVICING Figure 5 176 Relay Module Fuse Panel Decal MD 207816 214053 341 Revision A ...
Страница 355: ...MAINTENANCE AND SERVICING Figure 5 178 Roof Headliner Fuse Decal MD 207819 214053 343 Revision A ...
Страница 370: ......
Страница 388: ......
Страница 487: ......