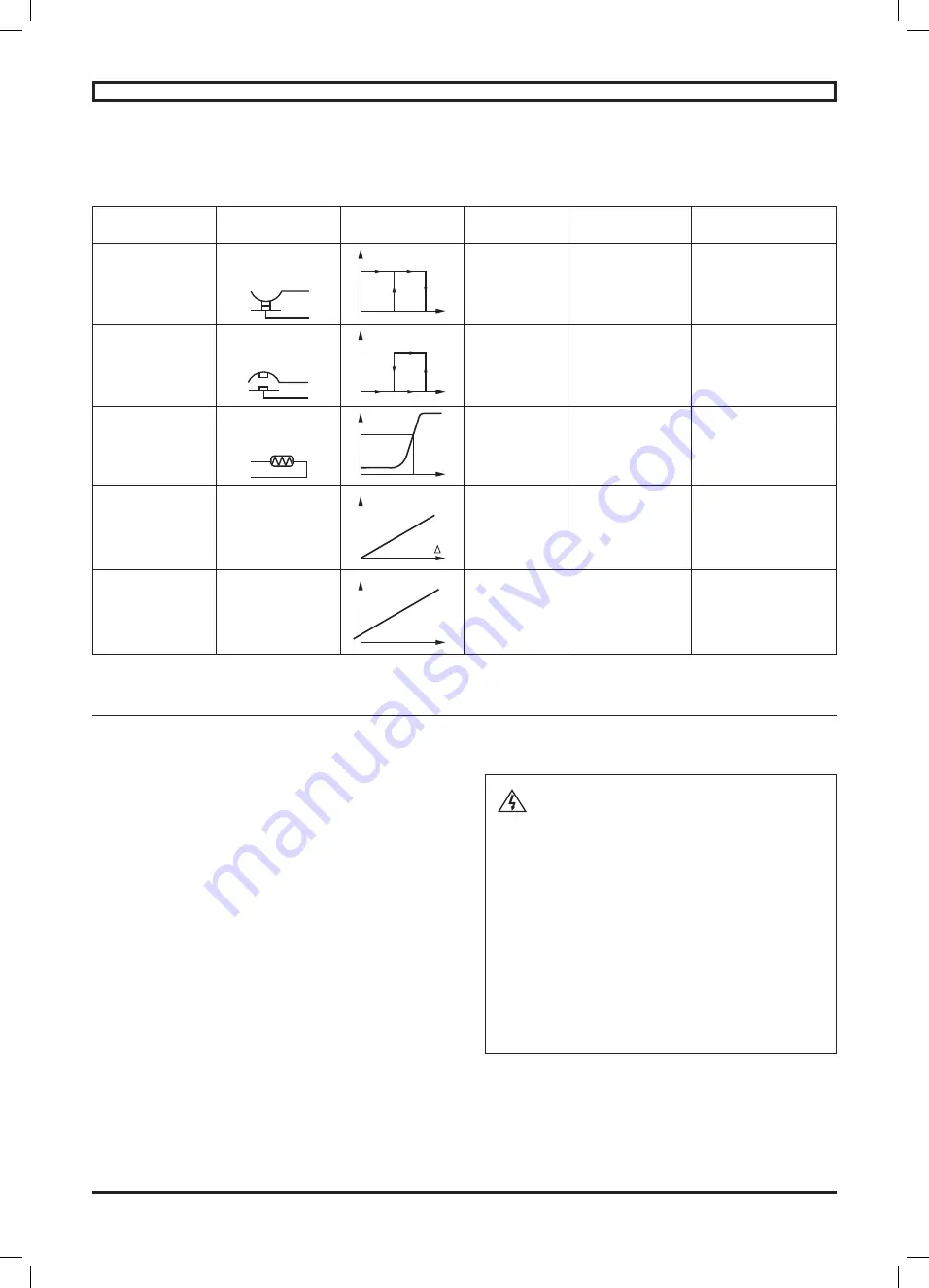
14
Installation guide -
(
F)LS (ES, IA, MV, PX), FCR
2908 en - 2017.08 / v
Alarm and early warning
All protective equipment may be backed up by another type of
equipment (with a different NRT). The first device will then act as an
«early warning» system (light or sound signals given without shutting
down the power circuits), and the second device will be the actual
alarm, shutting down the power circuits.
Protection against condensation: space heaters
Identification: 1 red label
A glass fibre flexible resistor is fixed on 1 or 2 coil end turn(s) which
heats the machines when stopped and therefore prevents any
condensation inside the machines.
Power supply: 230 V single phase unless otherwise requested by the
customer.
The drain plugs underneath the motor should be opened
approximately every six months. They should then be replaced to
ensure IP -- motor protection.
Thermal magnetic protection
The motor must be protected by a thermal magnetic device, sited
between the isolating switch and the motor. These protective devices
safeguard motors fully from non-transient overloads.
This device can be fitted with a fused circuit-breaker.
Built-in direct thermal protection
For low rated currents, bimetallic strip-type protection may be used.
The line current passes through the strip, which shuts down or restores
the supply circuit as necessary. The design of this type of protection
allows for manual or automatic reset.
Built-in indirect thermal protection
The motors can be equipped with optional heat sensors; these sensors
can be used to monitor temperature rises at «hot spots»: overload
detection, cooling check, monitoring strategic points for installation
maintenance.
It must be emphasized that these sensors cannot ever be used to
directly control the motor operating cycles.
Thermal protection
Caution: whatever the type of protection, (PTO or
PTF), its NRT must not exceed:
• 150 °C max for the stator and 120 °C max for the shields if the
maximum surface temperature = 125 °C.
• 160 °C max for the stator and 130°C max for the shields if the
maximum surface temperature = 135 °C.
• 170 °C max for the stator and 140 °C max for the shields if the
maximum surface temperature = 145 °C.
If using sensors with variable resistances or thermocouples,
the associated equipment must stop the motor at a
temperature of:
• 150 °C max for the stator and 120 °C max for the shields if the
maximum surface temperature = 125 °C.
• 160 °C max for the stator and 130 °C max for the shields if the
maximum surface temperature = 135 °C.
• 170 °C max for the stator and 140 °C max for the shields if the
maximum surface temperature = 145 °C.
Line protection: setting the thermal protective device
This must be set at the level of current shown on the motor nameplate
for the voltage and frequency of the connected mains supply.
2.6 - Electrical advices
Thermal protection and space heaters
Type
Operating
principle
Operating
curve
Breaking
capacity (A)
Protection
provided
Mounting
Number required*
Normally closed
thermostat
PTO
Bimetallic strip,
indirectly heated,
with N/C contact
2.5 at 250 V
with cos
j
0.4
general surveillance for
non-transient overloads
Mounted on control
circuit
2 or 3 in series
Normally open
thermostat
PTF
Bimetallic strip,
indirectly heated,
with N/O contact
2.5 at 250 V
with cos
j
0.4
general surveillance for
non-transient overloads
Mounted on control
circuit
2 or 3 in parallel
Positive temperature
coefficient thermistor
CTP
Variable non-linear
resistor,
indirectly heated
0
general surveillance for
transient overloads
Mounted with associated relay
on control circuit
3 in series
Thermocouples
T
(
T
< 150 °C)
Constantan copper
K
(
T
< 1000 °C)
Copper-Nickel
Peltier effect
0
continuous surveillance
at hot spots at regular
intervals
Mounted on control panels
with associated reading device
(or recording device)
1 per hot spot
Platinum resistance
thermometer
PT 100
Variable linear
resistor,
indirectly heated
0
high accuracy continuous
surveillance at key hot
spots
Mounted on control panels
with associated reading device
(or recording device)
1 per hot spot
- NRT: nominal running temperature
- The NRTs are chosen according to the position of the sensor in the motor and the class of temperature rise.
* The number required affects the protection of the windings.
I
O
NRT
T
I
F
NRT
T
R
NRT
T
V
T
R
T
INSTALLATION - (F)LS (ES, IA, MV, PX), FCR
Содержание Nidec FCR Series
Страница 2: ......
Страница 21: ...es F LS ES IA MV PX FCR Instalación Motores freno asíncronos trifásicos cerrados Referencia 2908 es 2017 08 v ...
Страница 27: ......